Welcome to the Rare Woods USA Woodworker Sessions interview series. Here, we hope to discover more about what makes our woodworkers tick, how you became involved in the craft, how and why you build your pieces and maybe learn a few secret techniques and tips along the way!
Our interviewer, a woodworker since the age of 8, Tobias Lochner is no stranger to the workshop. Find out more about him here.
In this, the 7th issue of our Woodworker Sessions USA, we are truly honored to welcome William (Bill) Brown, founder of The Maine Coast Workshop in Camden, Maine.
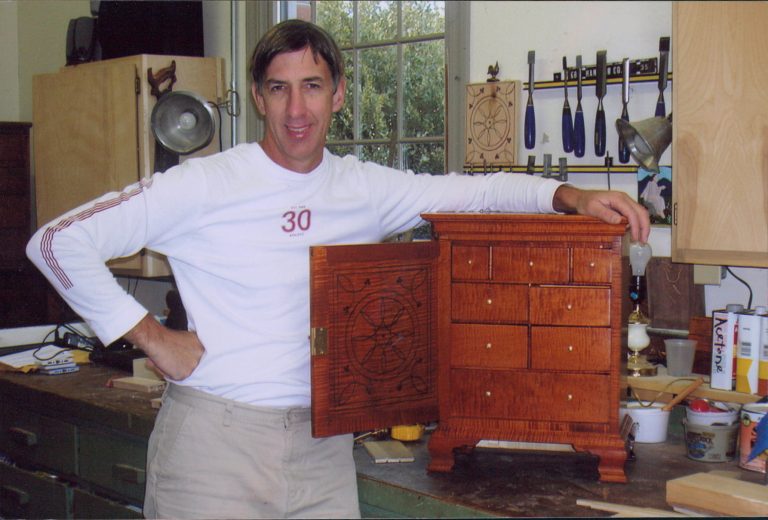
Question #1
Tobias: Hi Bill. Thank you for taking time out of your increasingly busy schedule to chat to us. Please could you tell us a bit about yourself, what is/was your career and a little about your family and how you became a woodworker.
William: I have been making high end reproduction furniture for 40 years. After graduating from Haverford College (in PA) with majors in music and biology, I thought I wanted to get my doctorate in molecular biology. After the first 12 rather miserable months spent with test tubes in the lab, I learned a lot about myself. Firstly, that I needed to be a generalist academically. Secondly, having been a tinkerer, growing as a musician, and possessing an artistic bent since toddlerhood, I realized that I absolutely needed to work creatively with my hands. I had a very strong sense that I wanted to work with wood and not any other media.
So I took a few years off, working at my dad’s tree nursery hoeing fields and digging trees and working in my brother’s landscaping crew. At the time (early 1980’s), there was almost nothing available in the way of woodworking classes. Having minimal funds, I sat down and wrote letters to furniture makers throughout the US, enquiring about working as an apprentice. No-one would take me!
I was however, very fortunate in convincing (“begging” is a more accurate description) a local Pennsylvania cabinetmaker, E. Townsend Moore, to let me into his shop. He had been a curator at DuPont’s Wintertur, outside Wilmington, DE and had learned his craft from a long line of Chester County period furniture makers. “Townie” Moore’s mentor was Thomas Treate Hogg, a well known Chester County reproduction furniture maker in the 1940’s -60’s. I worked 60 hours a week as a landscaper, but was at Townie Moore’s shop near Media, PA, every weekend. Because he saw the seriousness of my interest and he also did not have anyone to pass his skills on to, he really took me under his wing and gave me a lot of his valuable time. In return, as I had no money to offer, I did an extremely thorough cleaning of his shop after every work session, for which he was quite grateful.
Townie Moore was a wonderfully generous and patient teacher and I was an eager student who learned fast. After about a year, I was pretty much able to look at any photo of a period furniture piece and make what I saw.
What I found was that many professionals were just not all that happy! Making a living as an artisan is very hard work and many of the folk were not doing what they really wanted to, but were instead fixing broken chairs and repairing shabby Victorian dressers.
While I was out hoeing the fields in the hot sun at work one day, I decided that I’d apply to medical school and gain a more secure career, whilst pursuing furniture making on the side, any way I could. I already had a strong background in biology and chemistry at Haverford and I was also doing volunteer work with brain-injured patients at the Bryn Mawr Rehabilitation facility in Malvern, PA.
It took many years and about 10 different workshops for me to get things going properly. I have memories of using one of those toxic fume spewing “Ready Heaters” in my sub-zero garage in Watertown (far upstate) NY, where it was so cold that I had to wear gloves in the shop for many years.
To cut the story short, I went on to become an anesthesiologist and continued to be a passionate student of period furniture making. I simply used every opportunity to gain more skills and I kept learning about woodworking through the years. Over some 35 years, I slowly acquired a full shop of third-hand tools. My passion for furniture making and carving has continued to increase over the years.
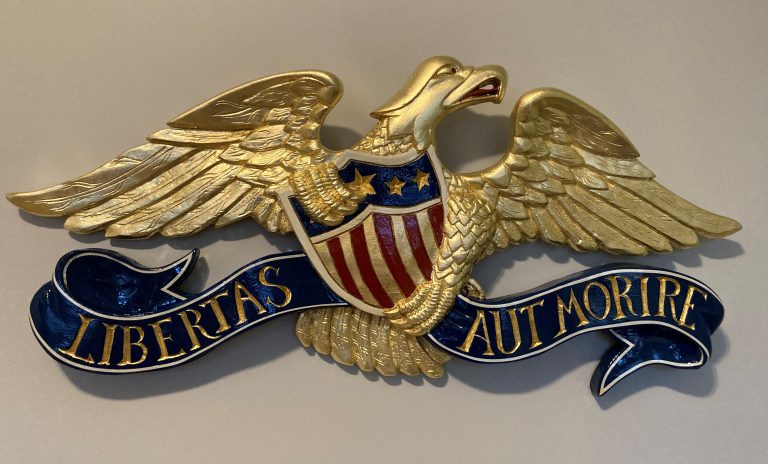
Question #2
Tobias: How did you get started doing woodwork and how long have you been a woodworker?
William: Tobias, I beat you to it! (See my answer to Question #1)
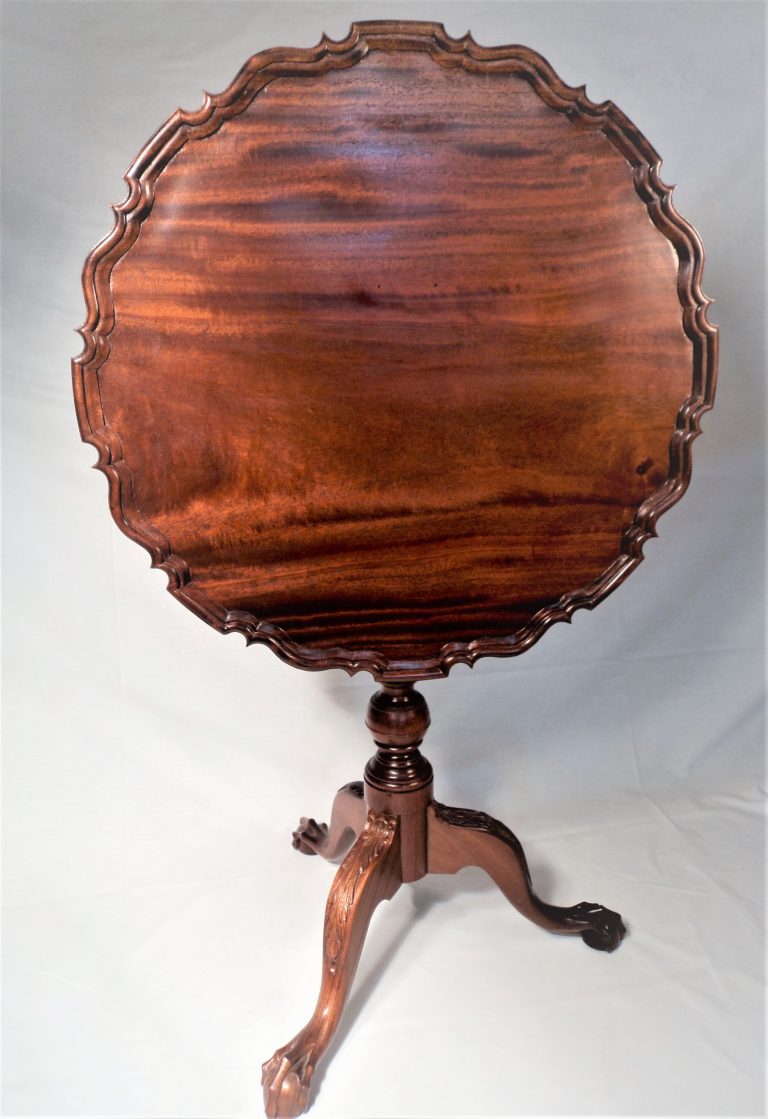
Question #3
Tobias: What was the first item you ever made and which is your favorite piece?
William: My first piece was a walnut Kentucky End Table that I made with Townie Moore as his apprentice in 1981. He wanted me do do some turning right off the bat! The piece involved most of the basic joinery required for any future furniture project. The drawer was cock-beaded, and I added the inlay more recently.
My favorite piece….I am not sure, but my wife loves my Alton Hall Serpentine Chest of drawers the most! I wrote an article in the last edition of “Period Furniture”, the annual journal of The Society of American Period Furniture Makers (SAPFM) on how to make the veneered serpentine drawers for this chest… (American Period Furniture (sapfm.org)
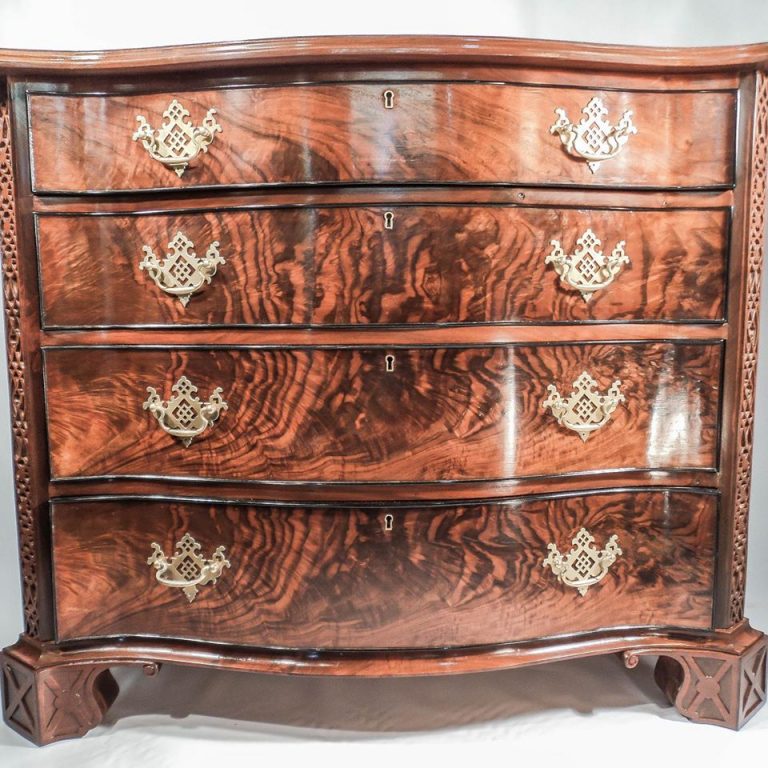
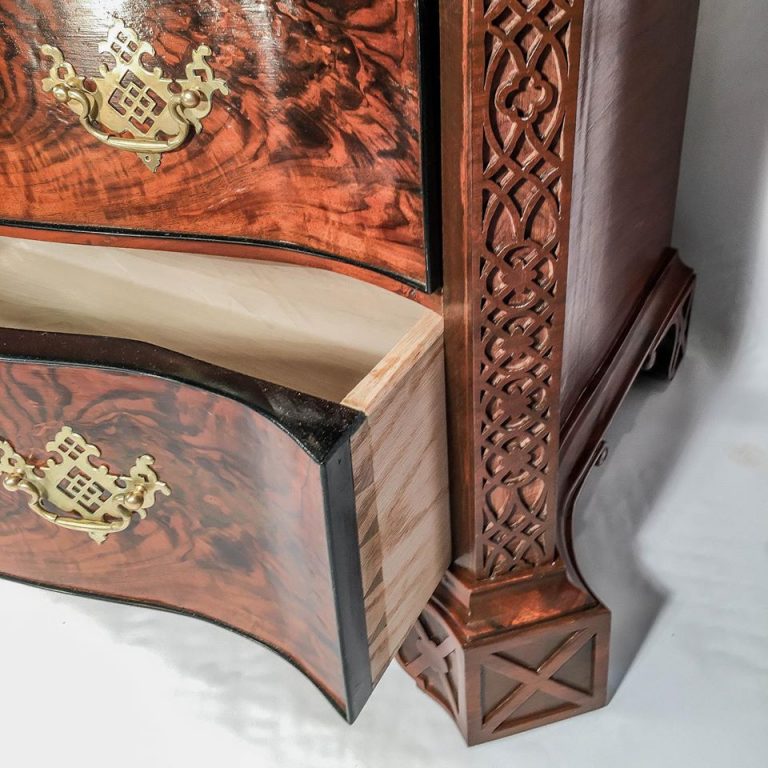
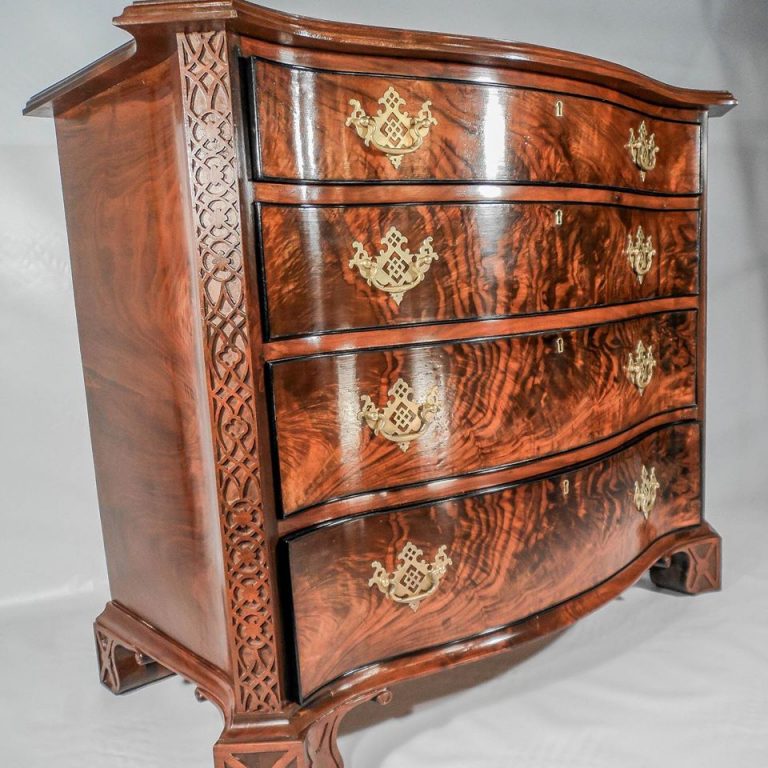
Question #4
Tobias: Which style of furniture do you enjoy building the most?
William: I prefer to make “historically informed” pieces. Unless specifically requested by a museum, my furniture pieces are not exact reproductions, but will incorporate design motifs and joinery that is representative of 18th and 19th century furniture. My work is created using similar hand-cut joinery and details, but each piece is my own design. Except for my museum and historic site reproductions where exact copies are desired, my furniture is one-of-a-kind, based on traditional design elements.
I enjoy the William and Mary period furniture very much and I incorporate ball feet in many of my projects, even contemporary ones. I have also been doing a lot of veneer and inlay work over the past 4-5 years with my Federal furniture. I really love carving and therefore Chippendale pieces are of special interest to me as are Queen Anne pieces. Shaker furniture also interests me and I hope to do some more pieces in this style in the near future. Most of my pieces are historically informed, but my own design.
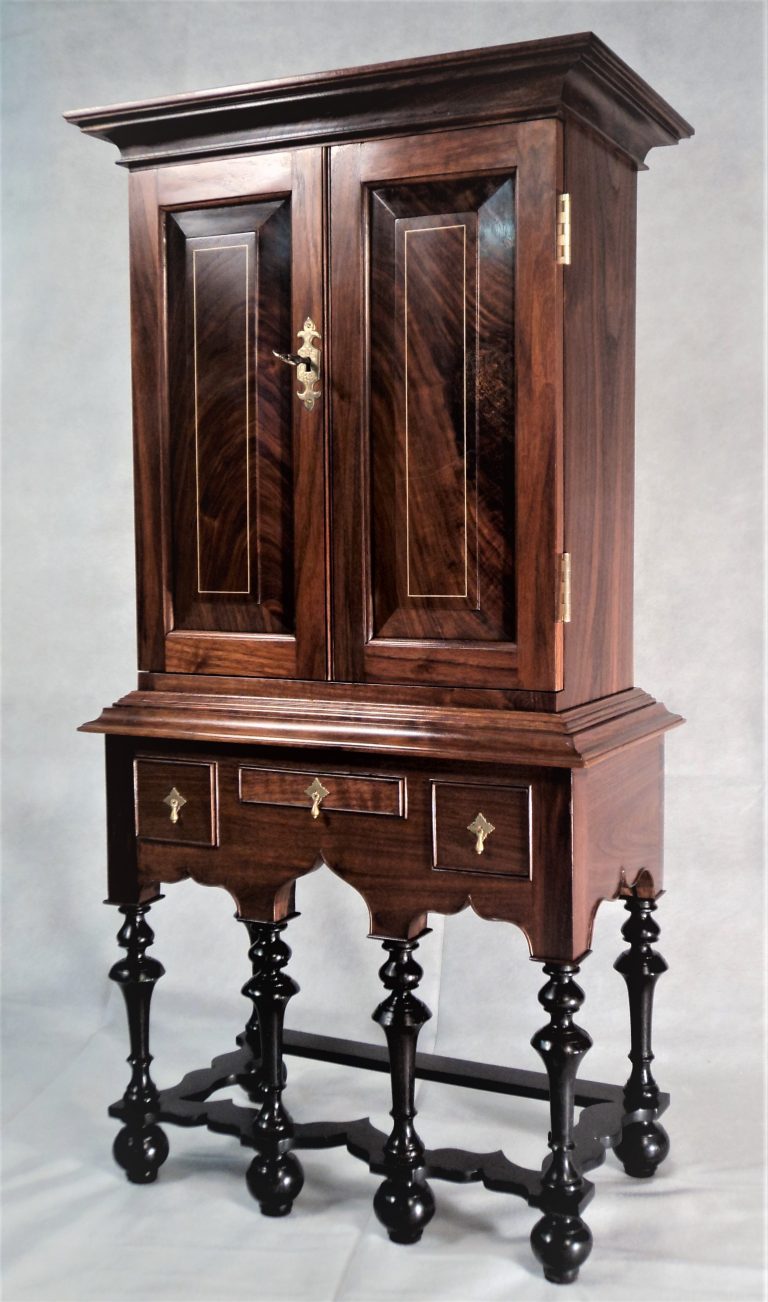
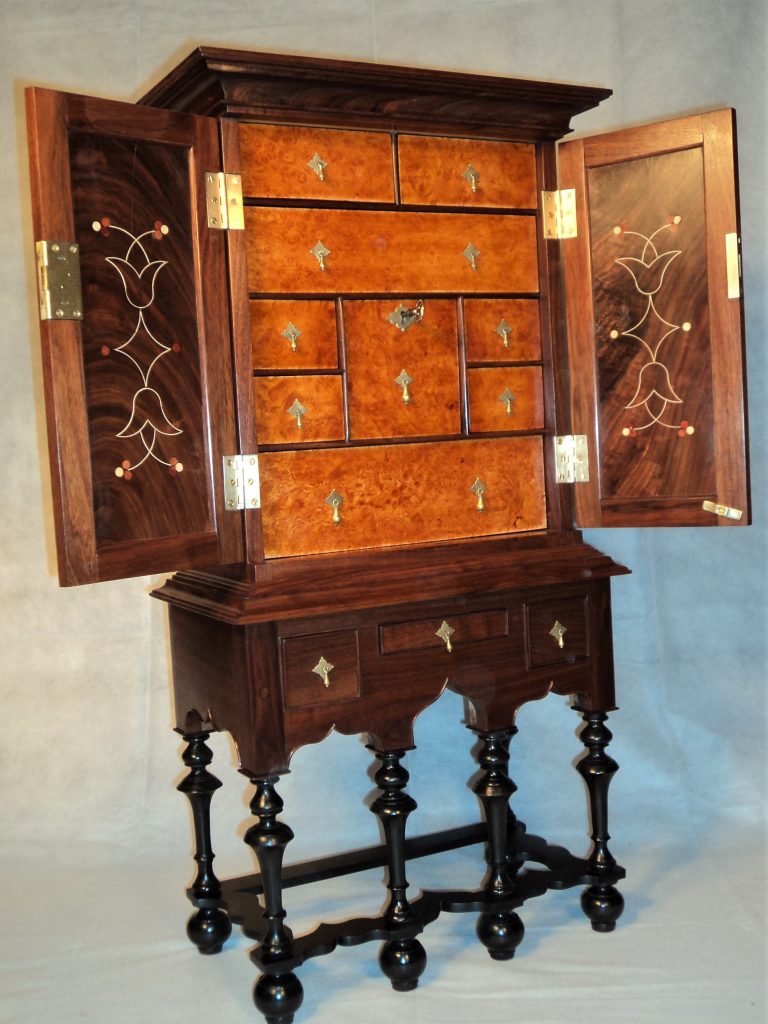
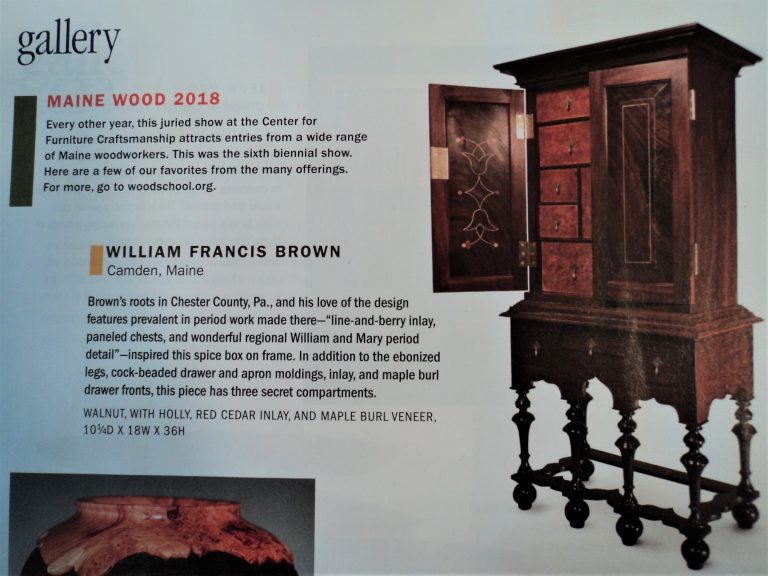
Question #5
Tobias: Which are your favorite local lumber species and which are your favorite exotics to work with?
William: I work predominantly with local hardwoods such as Walnut, Cherry, Maple, Pine and Poplar. I really enjoy figured varieties for my work and am always looking out for curly Maple, Walnut and Cherry. My Bellamy eagle carvings are mostly done in Pine and occasionally in Basswood. I use a lot of Holly, another local hardwood, for my inlay. It is the whitest of woods and contrasts beautifully with Walnut in particular. Cedar is local and is used for the berries in my line-and-berry inlay work.
I use a lot of exotic species, for reddish wood, I use Padauk and I use Katalox as my Ebony substitute. I love using Macassar Ebony and ribbon-striped Mahogany for crossbanding. I also use many other species, both local and exotic, for crossbanding and inlay work.
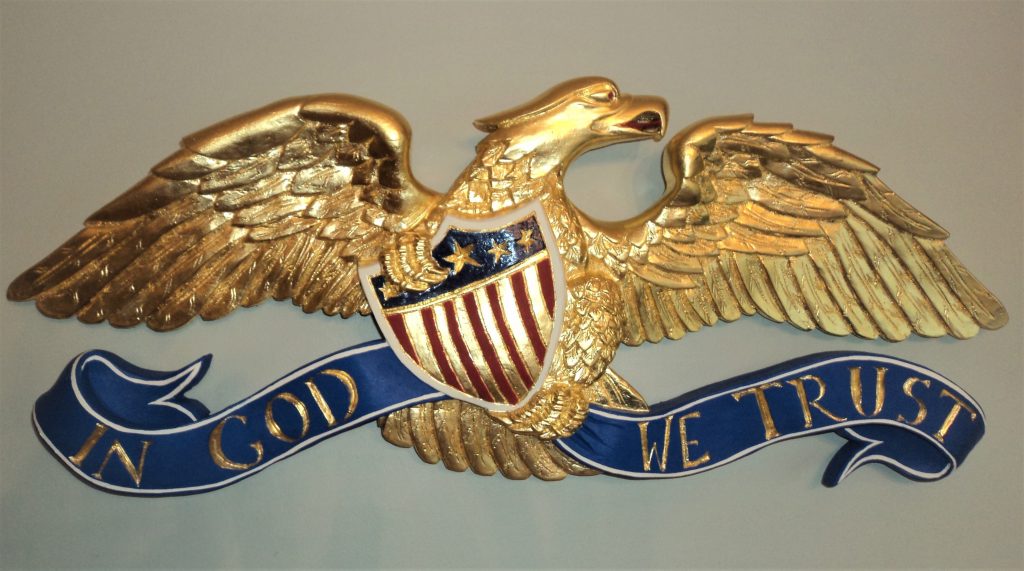
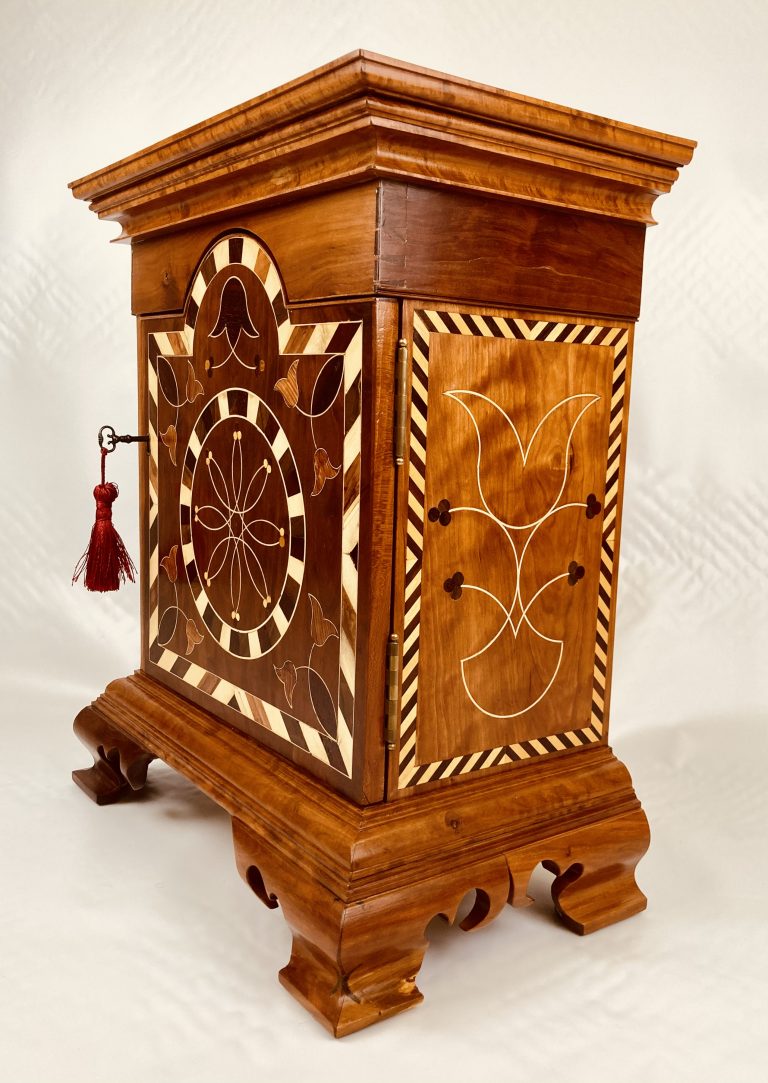
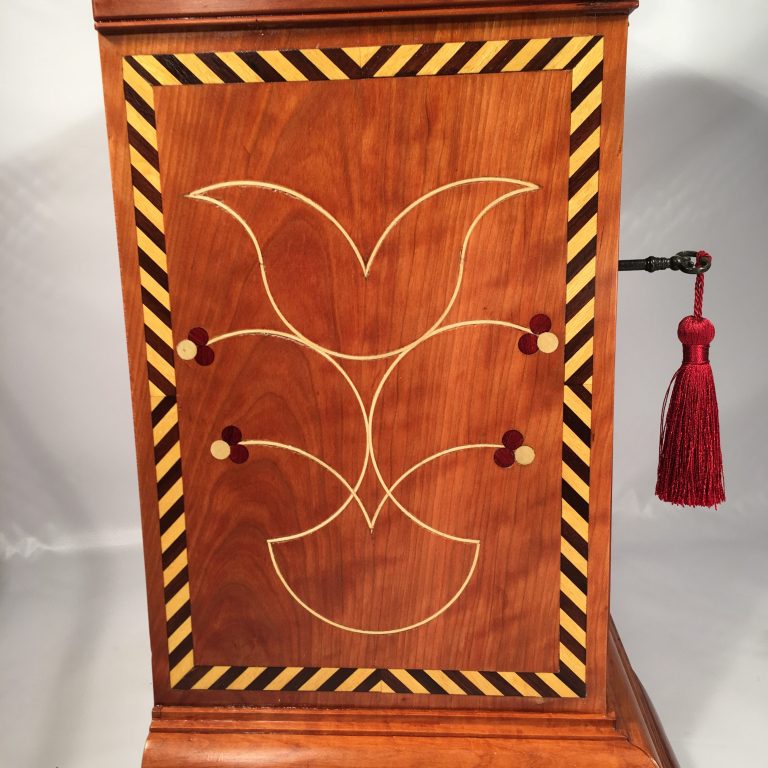
Question #6
Tobias: Please list your most used hand tools and tell us why they are your “go-to” tools.
William: I mainly use just a few hand planes. My Lie-Nielsen bronze block plane and their No.62 low angle jack plane handle almost everything I do. I also use a shoulder plane and a scrub plane at times and a set of Marples Blue Chip chisels handles all of my chisel requirements.
I have a Veritas dovetail saw and a Florip saw. I use the Lie-Nielsen radius cutter a lot for my inlay, it is an excellent and easy to use tool designed by my friend Steve Latta. I guess that I am just too cheap to buy mainly high end tools, so I keep mine well sharpened and honed and therefore they perform properly.
I have a distinct dislike for tool cabinets. My tool collection is fairly minimalist and I prefer to keep everything out and within easy and quick reach. My marking and layout tools all hang on my bench.
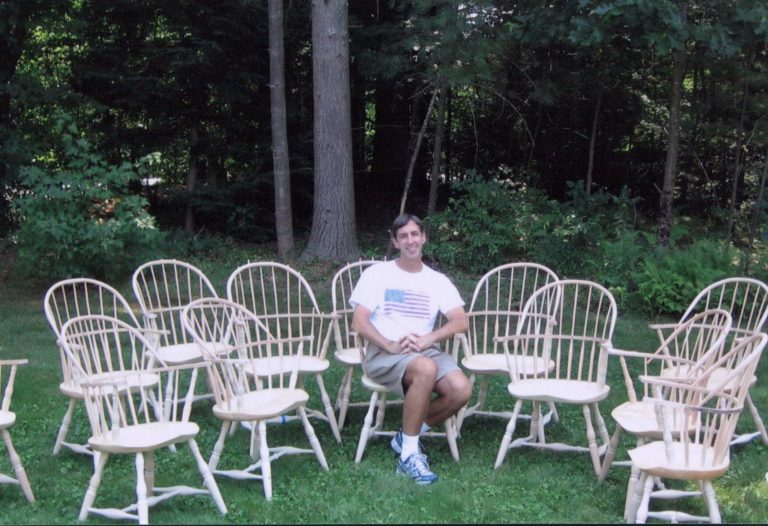
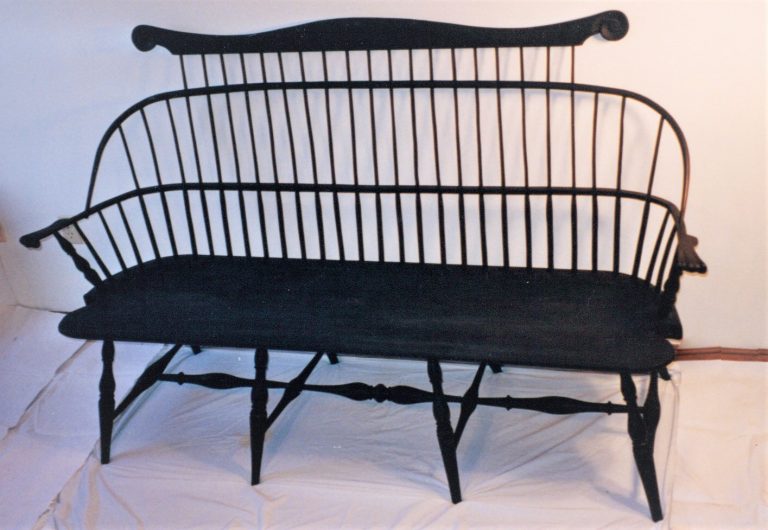
Question #7
Tobias: Can you list your favorite power tools and machines and tell us why?
William: No real favorites in this area. I have the basic set: 8″ General jointer (would love to have a 12″, but I am not sure how I would fit it into my shop). I did install a Byrd Shelix helical cutterhead into it, which I love. The planer is a 15″ Grizzly, also fitted with a helical cutterhead. I have a Grizzly table saw and a General drill press, as well. As a rather thrifty Scot, most of my tools were bought used. I often wish that I had a wide belt sander, but again, I unfortunately have a lack of available space.
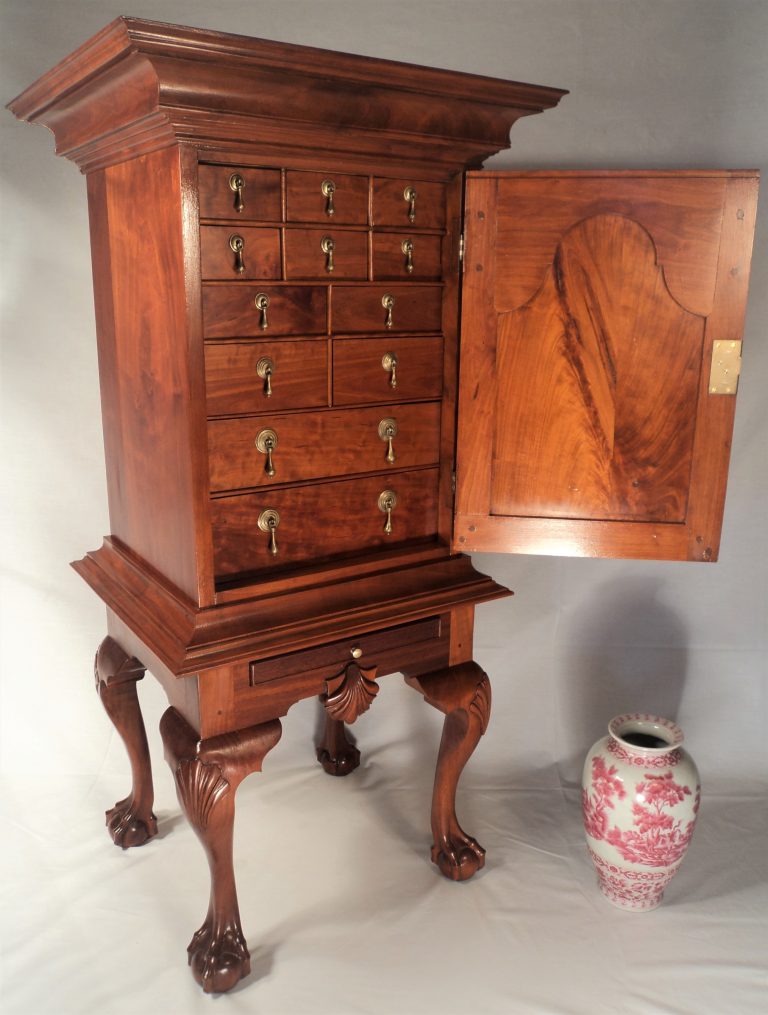
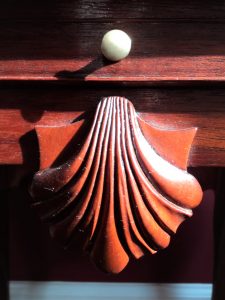
Question #8
Tobias: What is it about working with wood that you find most enjoyable?
William: I like to scour museum archives and study original pieces for ideas, patterns, moldings, inlay designs and proportions. I enjoy sketching details of Chester County pieces that I see in homes and exhibitions in my area. With time, one develops a trained eye. Craft is a combination of knowledge, skill and intuition all working together in harmony. It takes time and lots of effort to gain this, but it is great fun! A passion for excellence and beauty is why I love to make furniture.
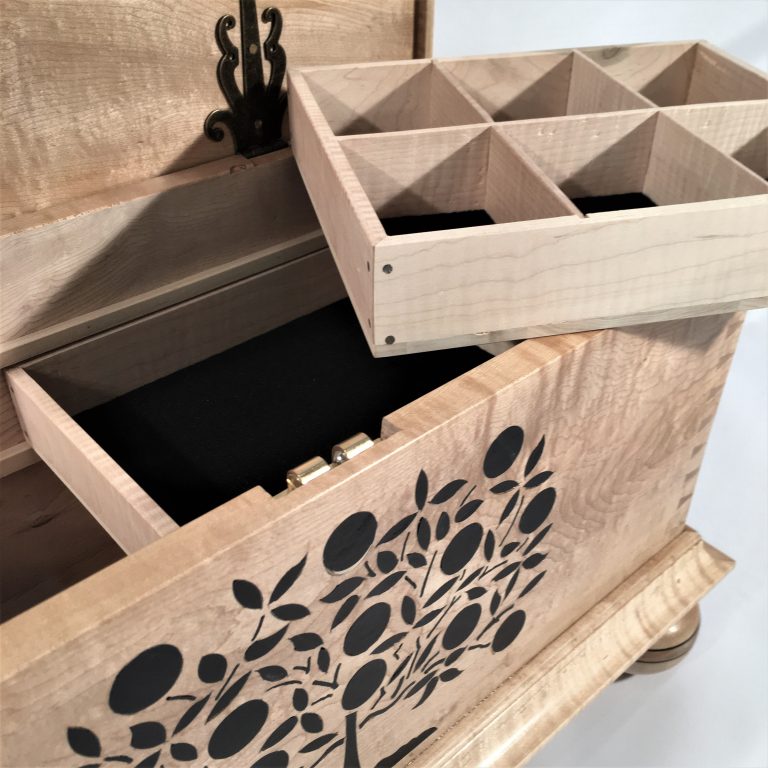
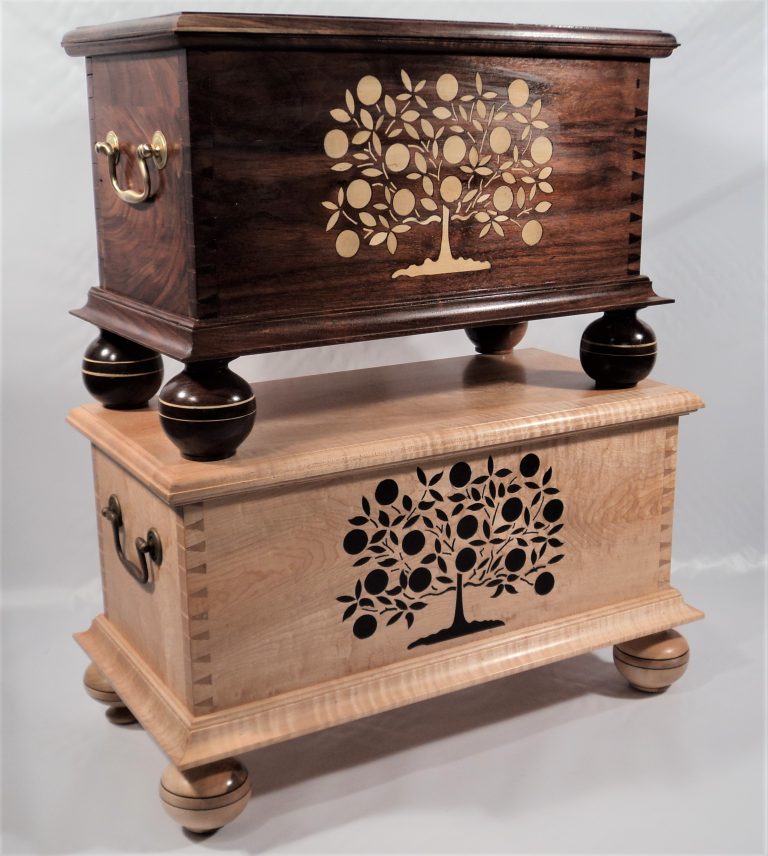
Question #9
Tobias: What type of workshop do you have, how has it evolved over time and why?
William: I have two workshops. My shop in Virginia is a 25′ x 30′ basement shop and is a “real” working shop where all my furniture is made.
My brand new 28′ x 28′ shop in Camden, Maine, is more of a boutique workshop where the Maine Coast Workshop classes will be held. This shop is all about comfort and aesthetics:
- 6 student benches with 2 vises each and a master’s instruction bench.
- Student hand tool and carving tool sets.
- Full slate of power tools and machines including an 8″ jointer and a 15″ planer.
- Comprehensive library of woodworking, carving and traditional arts books and videos.
- Pine floors throughout.
- Only three blocks from the picturesque Camden Harbor.
The Virginia shop has evolved over 35 years – I still have many of the original tools that I dragged around the country with various moves. Everything was in storage for about as many of those years in Mechanicsville., VA. You are right, our workshops always evolve, fine-tuning and tweaking is an ongoing process in the quest to make things more efficient and user-friendly. I don’t think that a month goes by, where I don’t make some improvement or alteration to the shop.
My layout allows for power tools to be on one side of the shop and my bench on the other. 90% of my shop time is spent at the bench. I like a lot of working surfaces and have modified a large desk that I pulled out of a dumpster and an old lab table that I got at an auction in upstate NY. Everything in the shop is on wheels, giving me an exceptionally versatile setup.
Last, but not least, my primary workbench was a $20 Craigslist find, which I have souped up and added to.
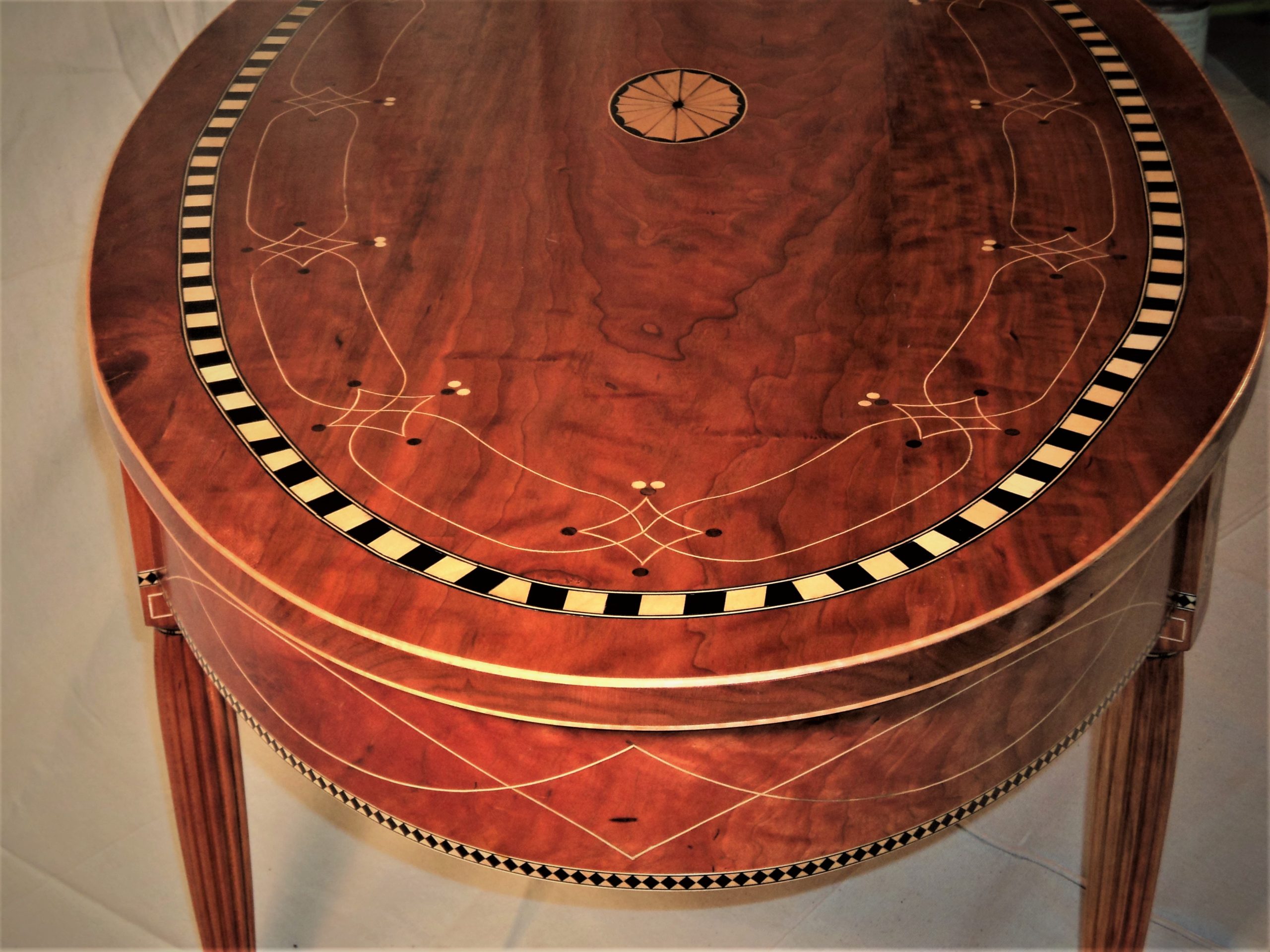
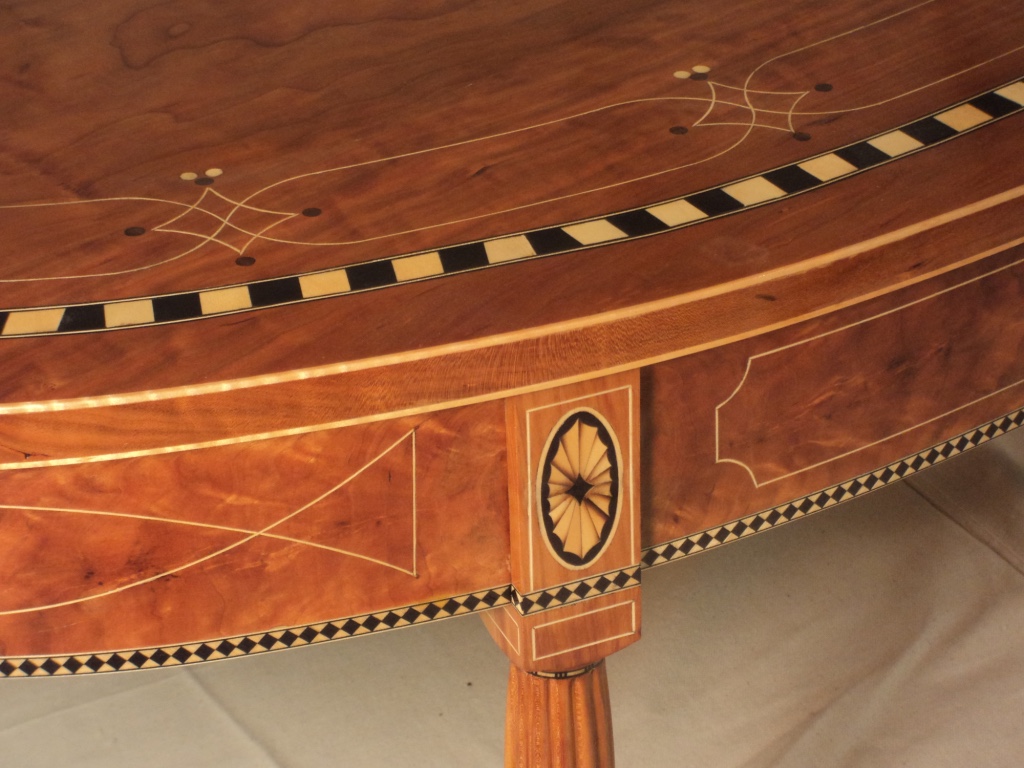
QUESTION #10
Tobias: What is your clamp line-up and why?
William: I love the Highland Hardware Quick Grip clamps. They are rugged and reliable and I use them for everything. I also found some wonderful and heavy Stanley clamps at Harbor Freight, which they no longer seem to carry. For larger glue-ups, I have the usual 1/2″ and 3/4″ pipe clamps with Jorgensen type fixtures. Also in the arsenal are a large quantity of small HF clamps which work fine and are super cheap. Most of my work consists of smaller pieces, so I don’t require a lot of larger clamps.
Question #11
Tobias: Which adhesives and glues do you use and why?
William: Yellow glue. I use white glue for Windsor chairs and when I require a longer set-up time. For veneer work, cold-press adhesive is my preference. I do have a glue pot, but I just have not quite caught onto using hot hide glue. I have played it a few times, but have not given it the full college try-out yet!
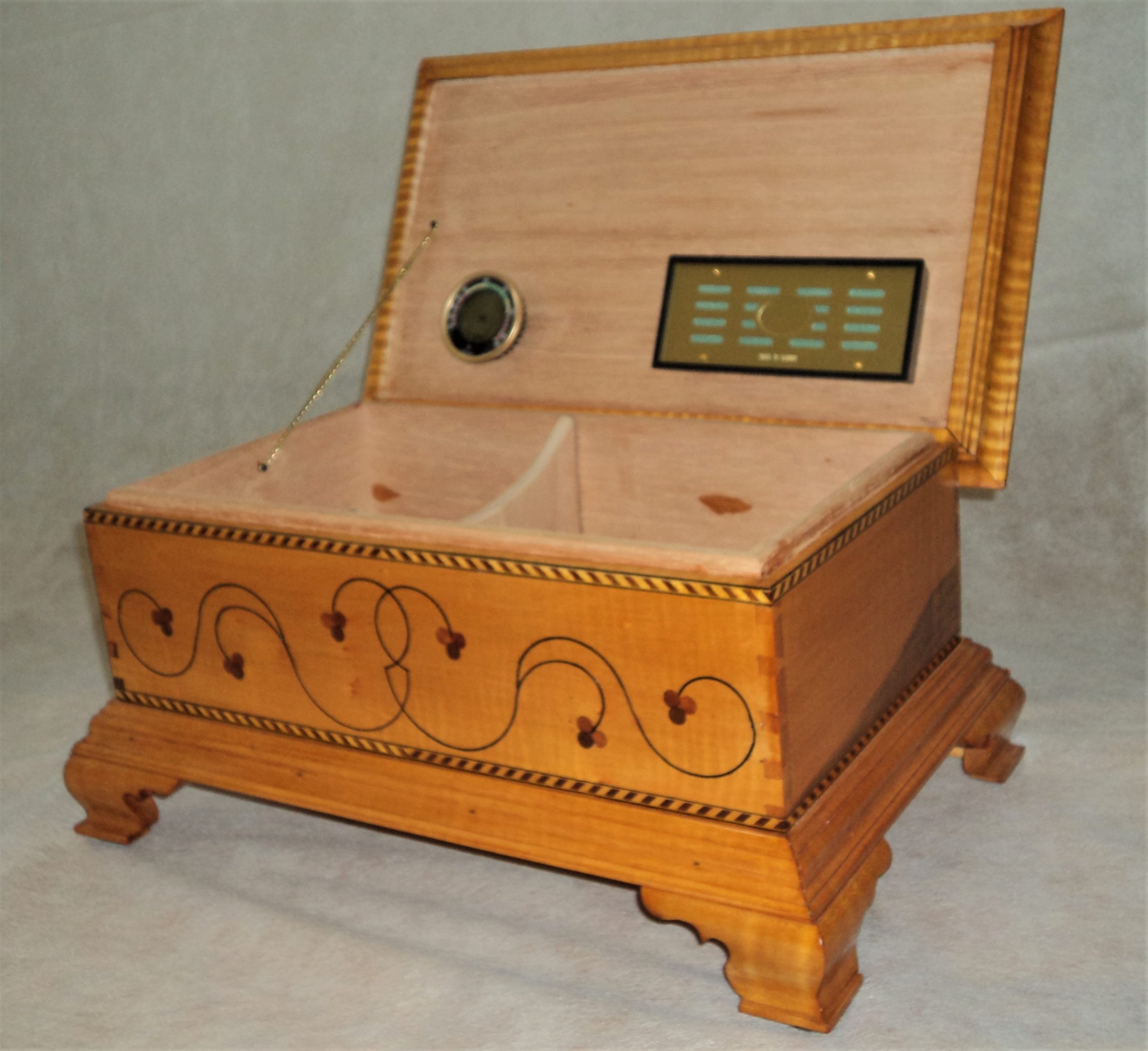
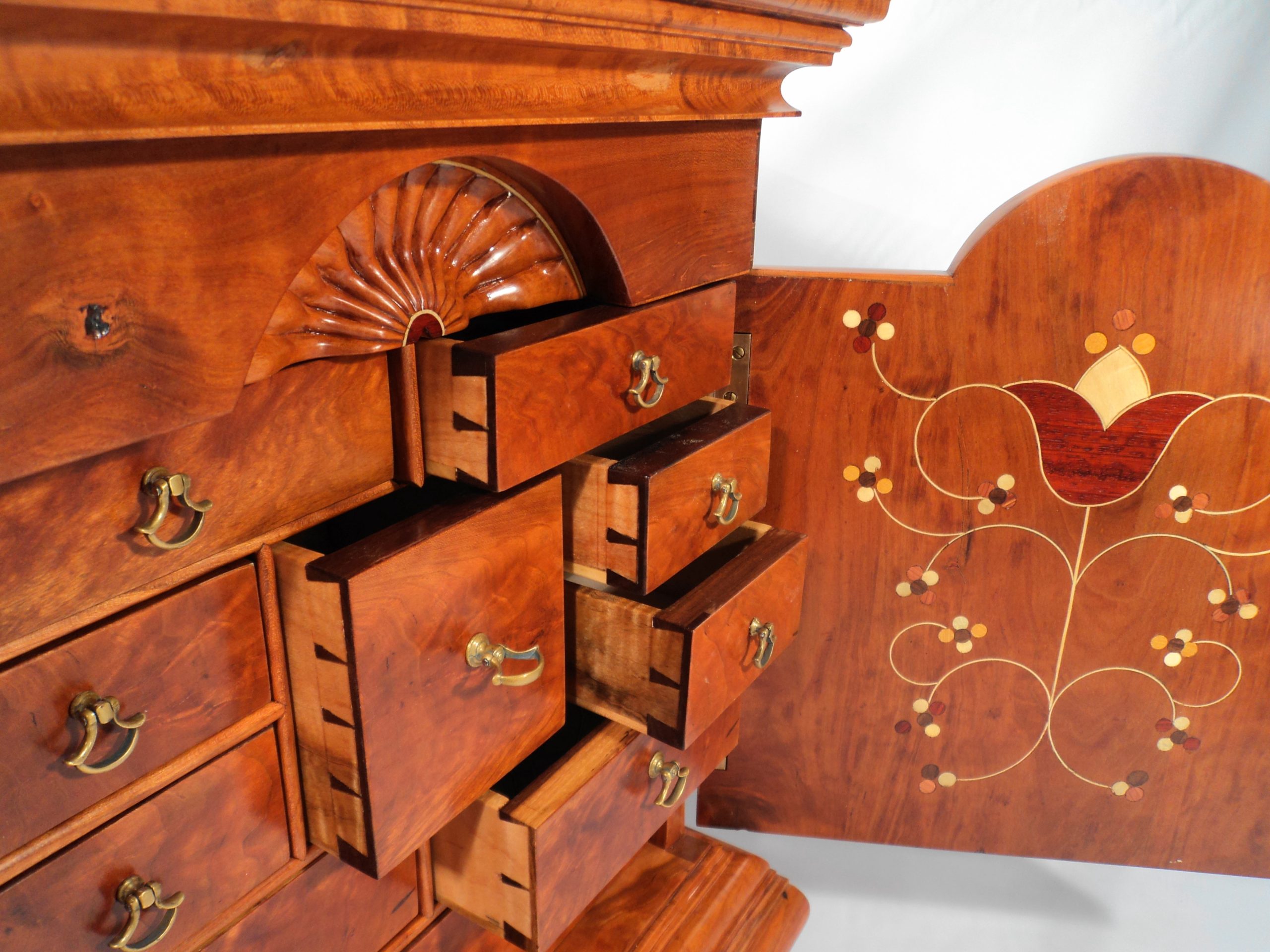
Question #12
Tobias: Which woods (exotic and local) have you not yet used and why are you interested in building with them?
William: See question #5 above. I really like spalted Maple, I have not used it yet, but I think that it could work very well in my “Tree of Life” keeping boxes.
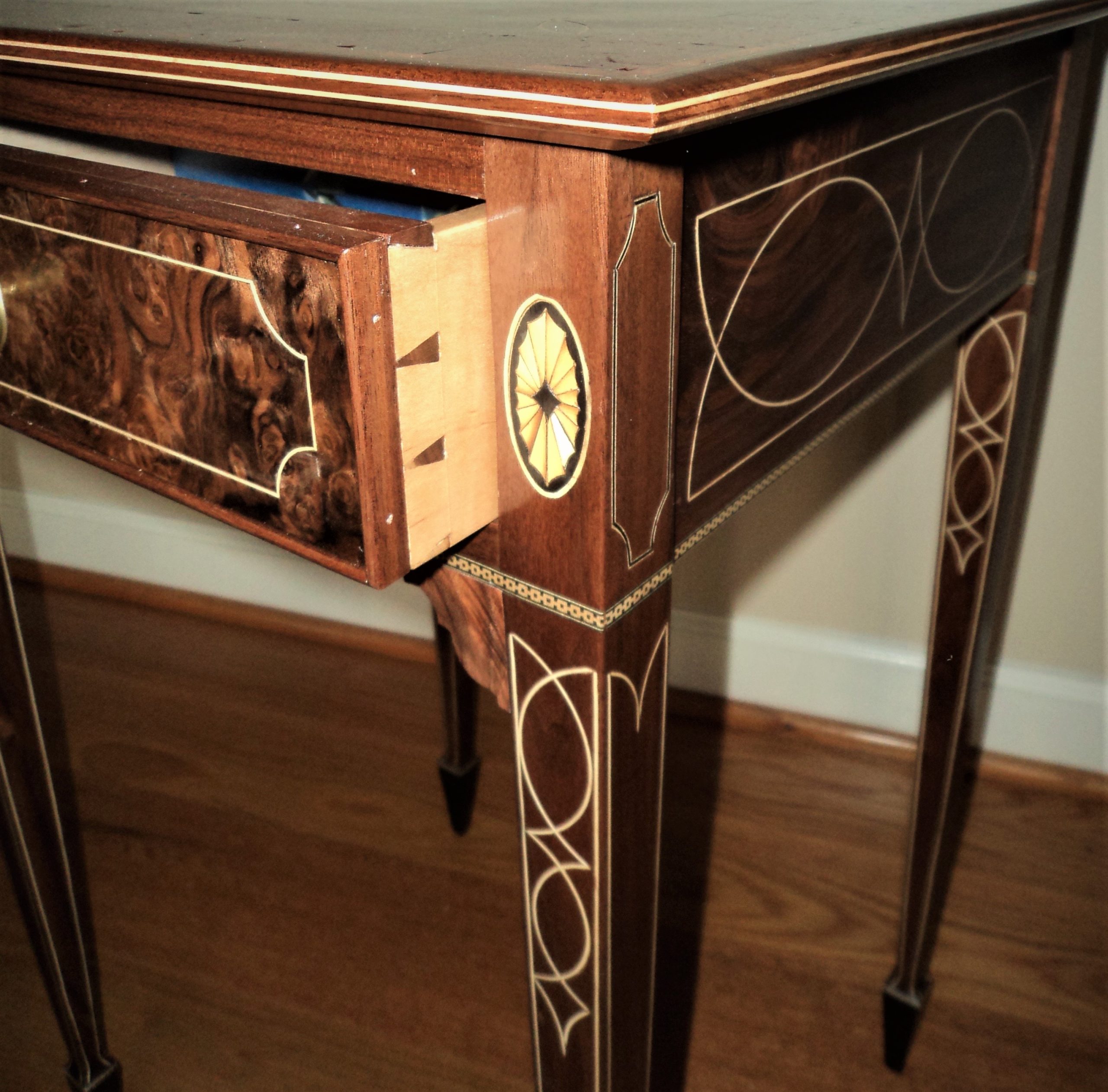
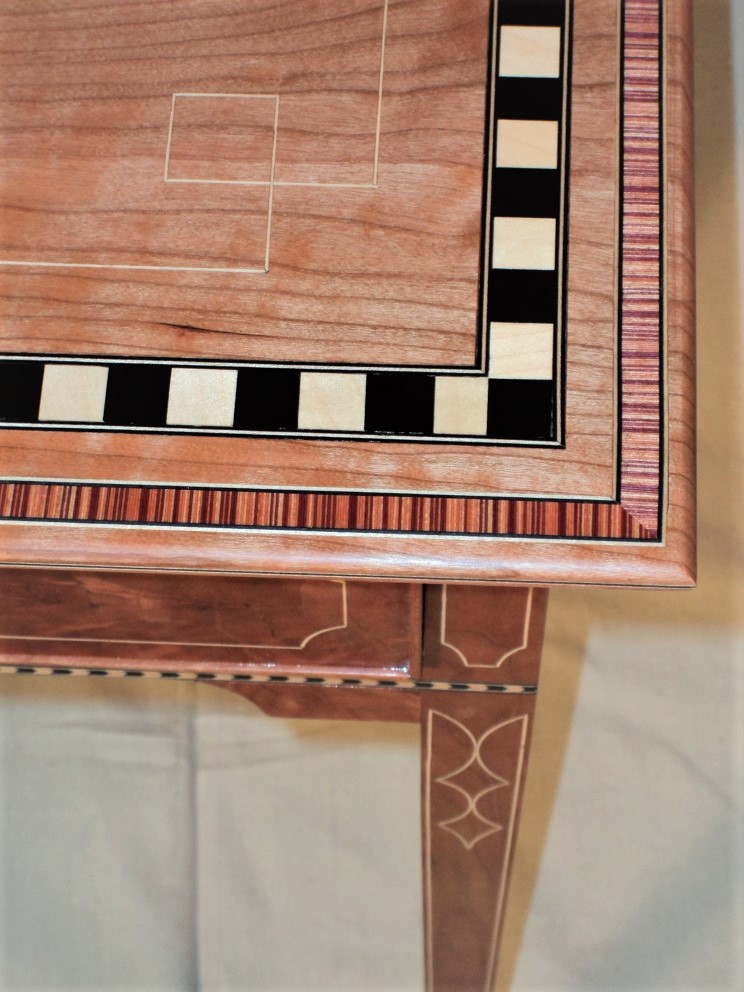
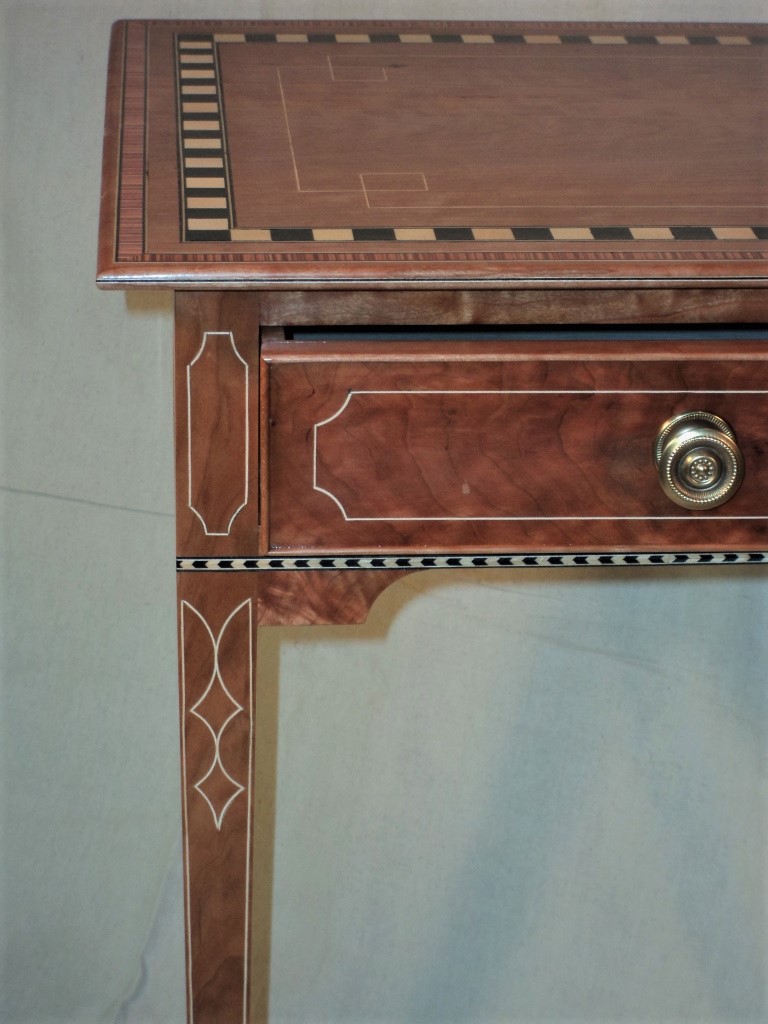
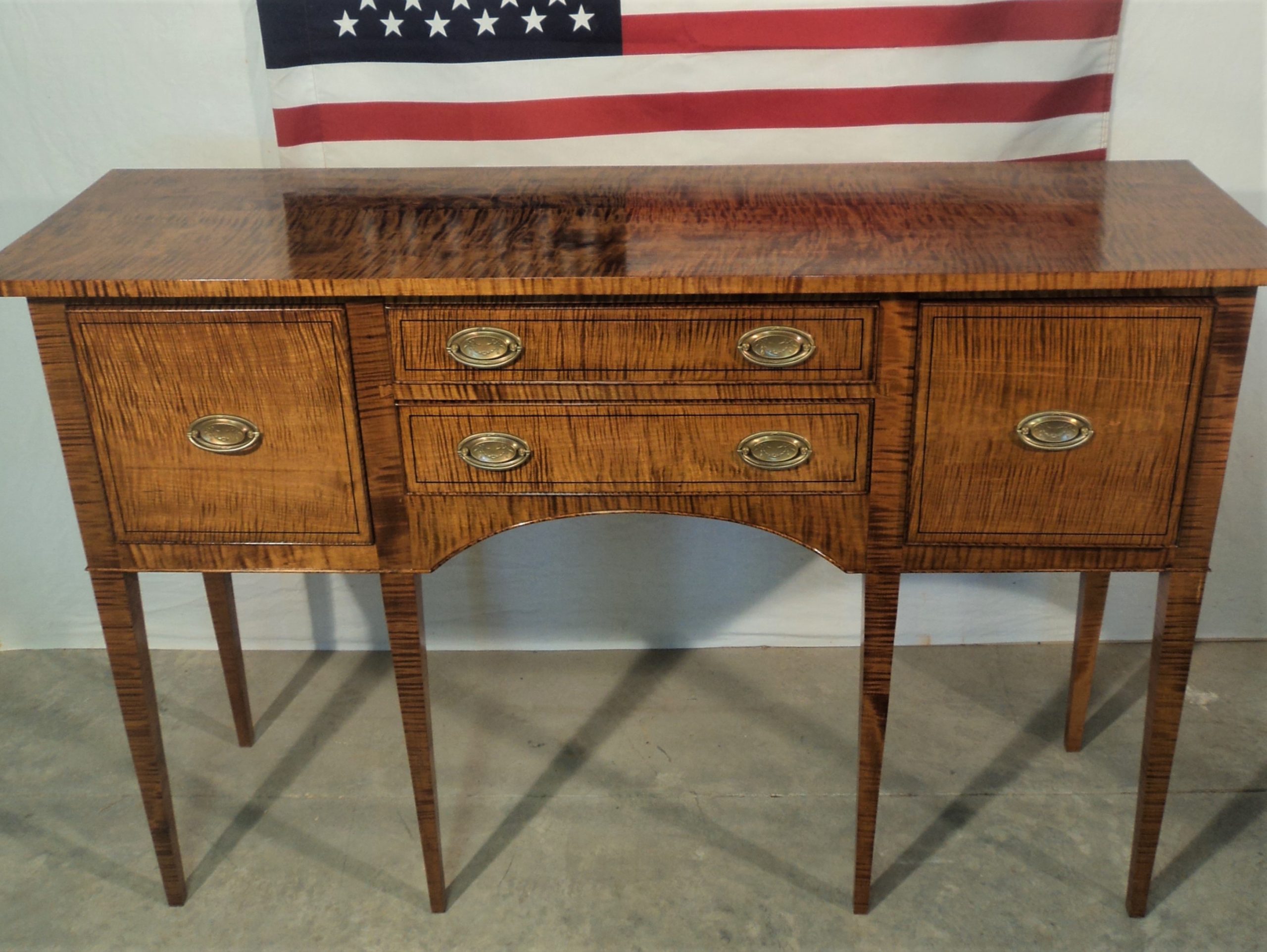
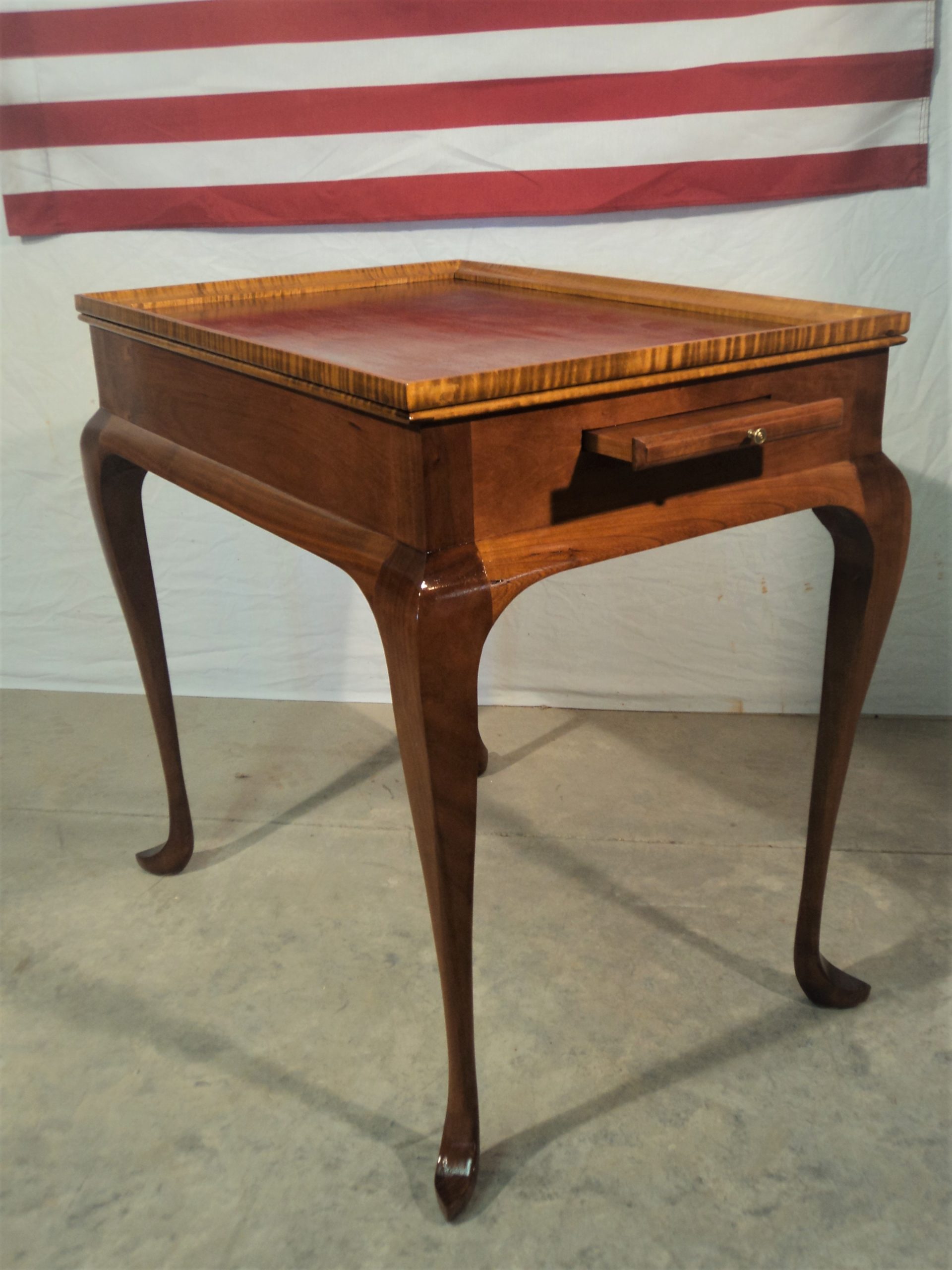
Question #13
Tobias: What and who are your sources of inspiration for your craft?
William: The who part is rather easy: Chuck Bender, Glen Huey, Steve Latta and the 18th century Chester County furniture makers. The what is much wider… museums, private collections and books!
Favorite woodworking books:
- Hand Tools: Their Way & Workings – Aldren Watson
- Country Furniture – Aldren Watson
- A Reverence for Wood – Eric Sloane
- Museum of Early American Hand Tools – Eric Sloane
- An Age of Barns – Eric Sloane
- The Vanishing Landscape – Eric Sloane
- For Spacious Skies – Eric Sloane
- Once Upon a Time (The Way America Was) – Eric Sloane
- The Spirit of ’76 – Eric Sloane
- Paint, Patterns & People: Furniture of Southeastern Pennsylvania 1725-1850 (Winterthur) – Wendy Cooper & Lisa Minardi
- American Furniture of the 18th Century: History, Technique & Structure – Jeffrey P. Greene
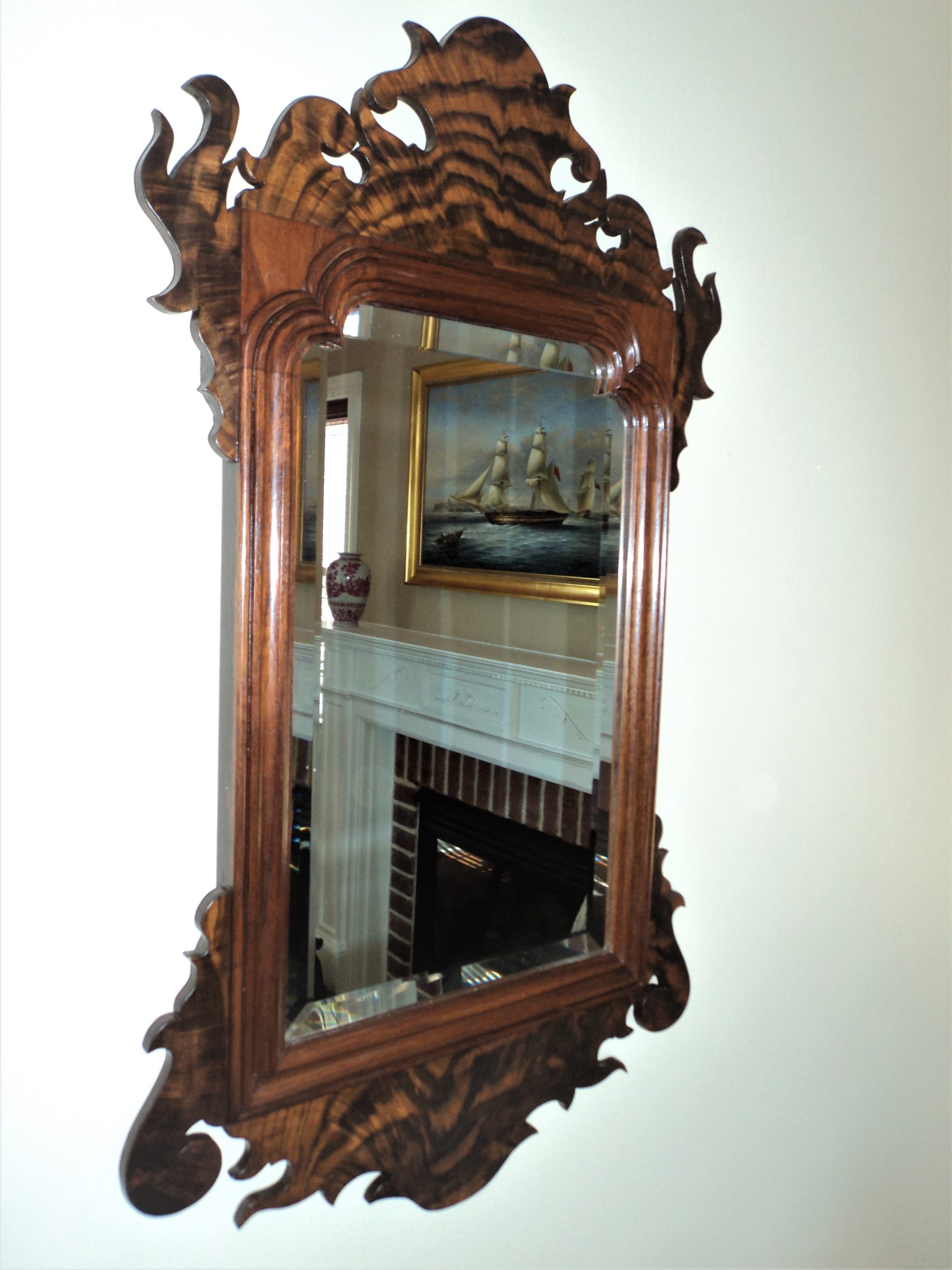
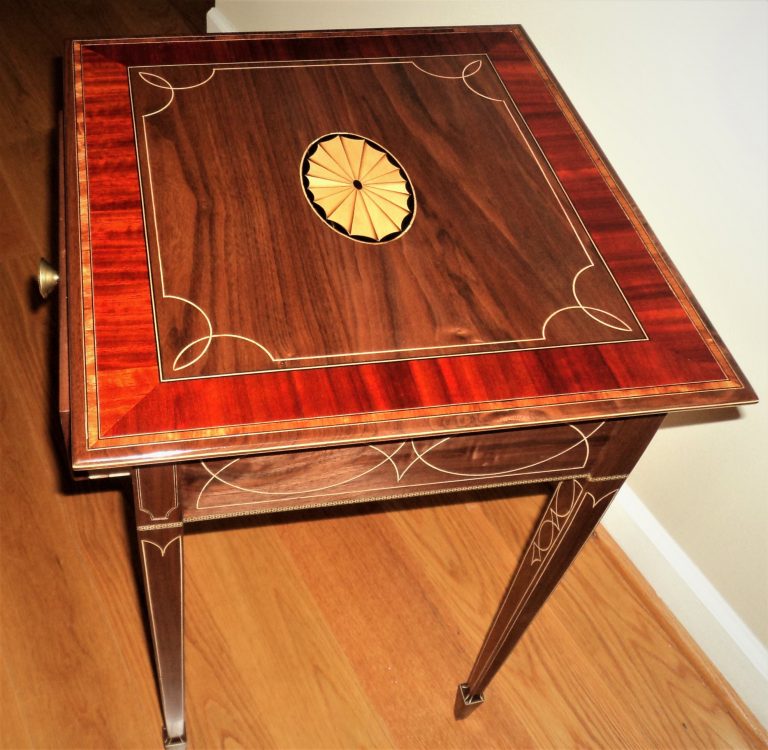
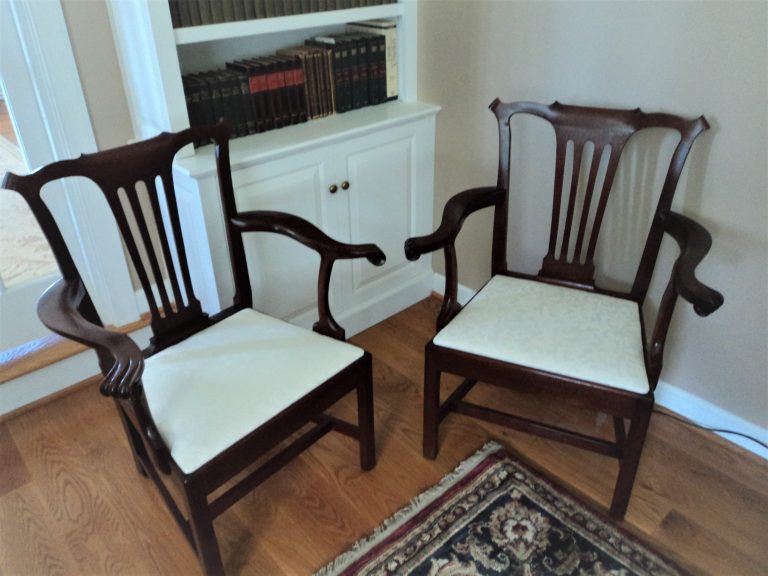
Question #14
Tobias: How do you design your pieces? Do you use CAD or SketchUp? Do you sketch out by hand?
William: I look at photos everywhere and anywhere! I take photos at museums and historic sites. I am much more of an artist than an engineer and do not make plans. Typically, I start with a sketch to get the proportions looking good and then I just start milling wood. I will always make little sketches as I go, for the details and moldings. I keep a file for each project with all my relevant notes and sketches.
I have tried working from plans made up by others, but I find it confusing and rather difficult.

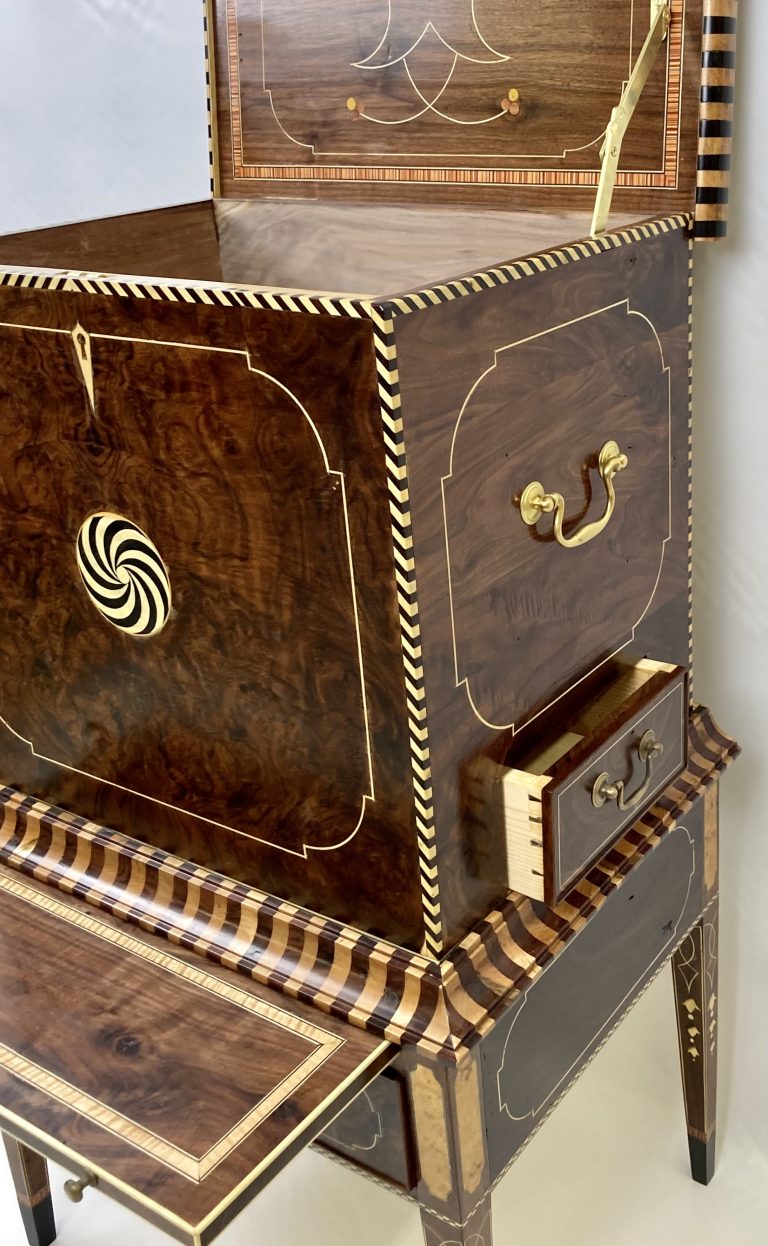
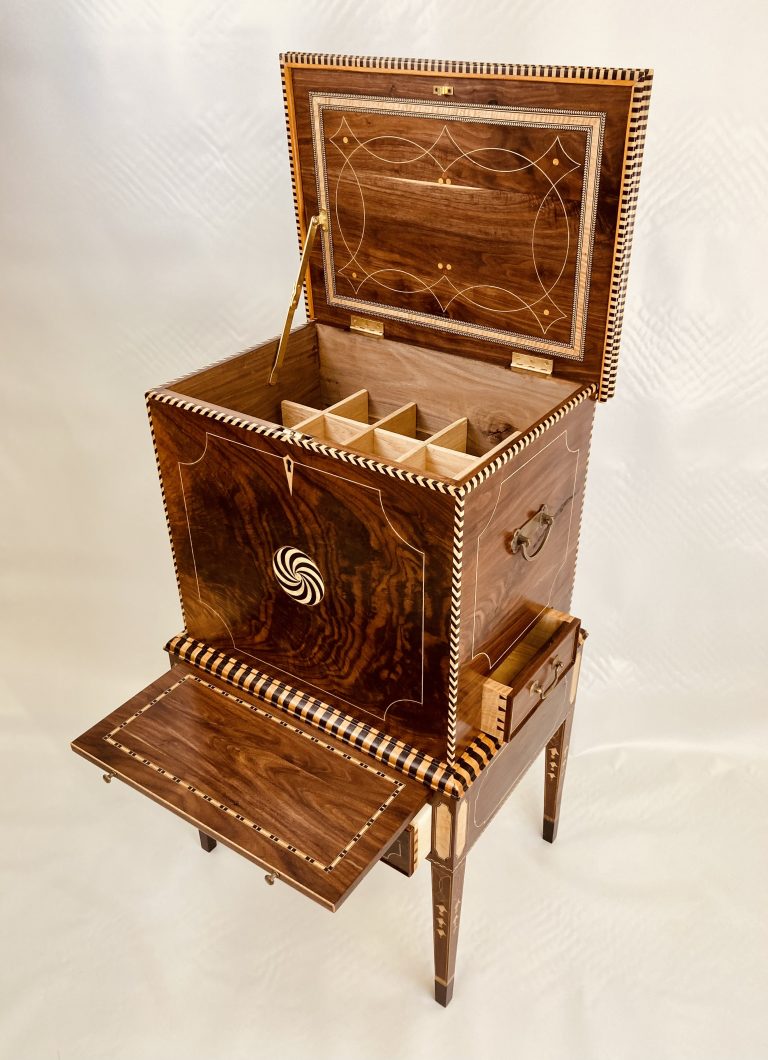
Question #15
Tobias: What are your finishing regimes, what products do you use and which are your favorite processes?
William: I use oil and shellac for almost every project. Since I work with beautiful and highly figured woods, I rarely add color. If I have used inlay in a piece, especially Holly, I definitely do not want to obscure or “yellow” it with dyes or other coloring agents.
My process is almost always to use boiled linseed oil followed by shellac. Although boiled linseed oil will darken Walnut considerably, it creates a striking contrast with the Holly inlay. If I require a perfectly clear chatoyance, I use Zinsser Sealcoat and will also sometimes add varying amounts of “Clear” or “Amber” to achieve the patina that I am looking for.
After the finish has properly cured, I usually rub out the shellac with 4-0, steel wool, then 6-0 steel wool, followed by Renaissance Wax which is my favorite due to it’s high content of carnauba wax.
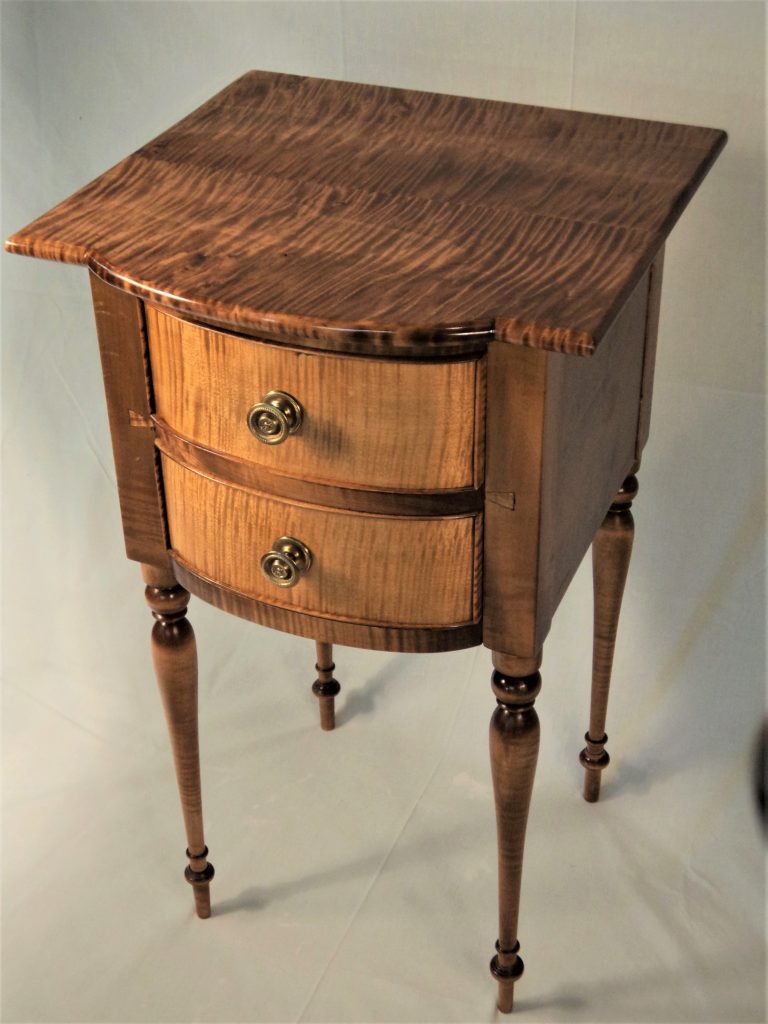
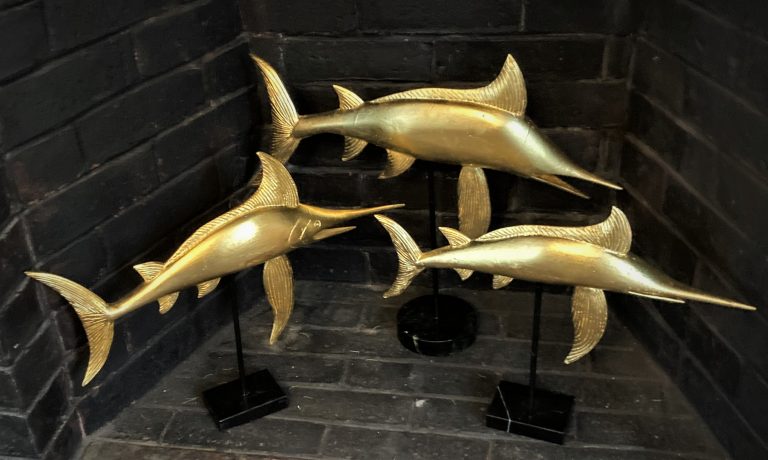
Question #16
Tobias: Which parts of working with wood do you dislike the most?
William: I like all aspects of working wood. I don’t do very much sanding, so I can’t offer the stock answer here!
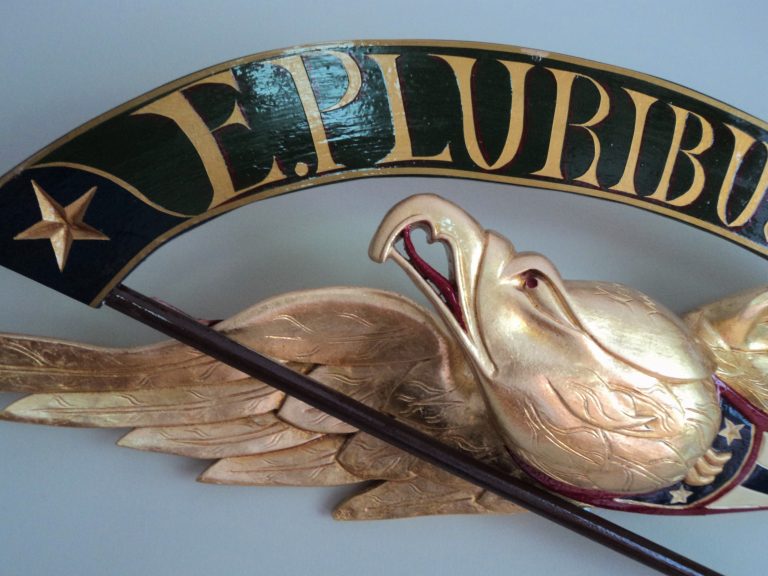
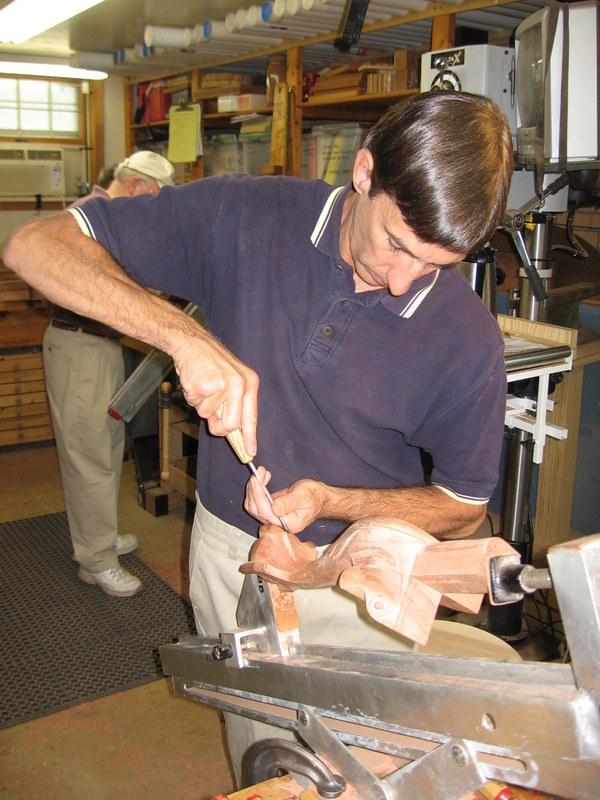
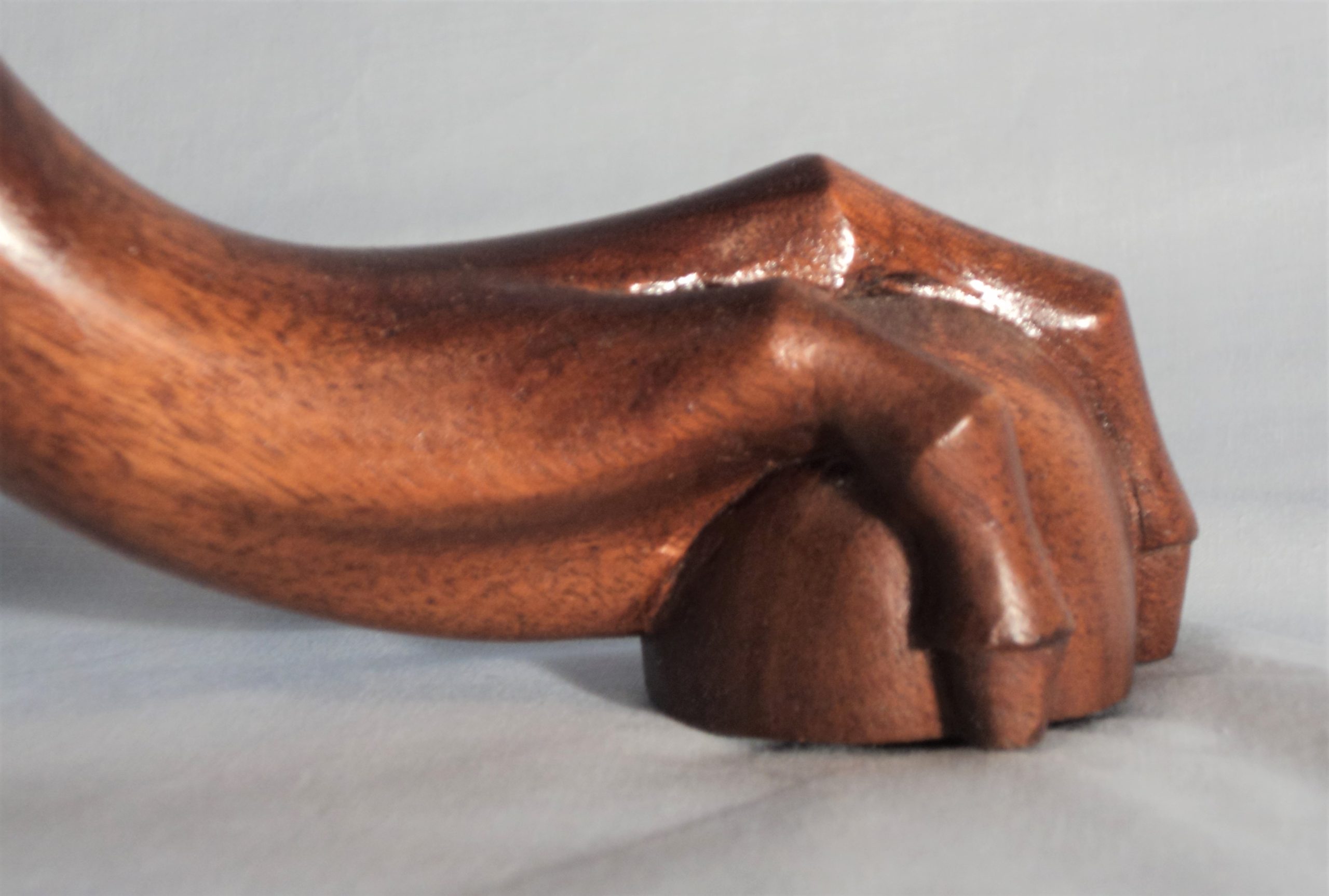
Question #17
Tobias: What is your favorite music to listen to whilst working in your shop?
William: I am a guitarist and have my own YouTube channel. I enjoy folk, celtic, Leo Kottke and John Fahey style guitar, classical and 60’s-70’s British rock including Genesis, Emerson. Lake & Palmer, Yes, Jethro Tull, etc. I also enjoy podcasts as well – history, political, Bible, sermons and audio books. I am currently going through C.S. Lewis and G.K. Chesterton.
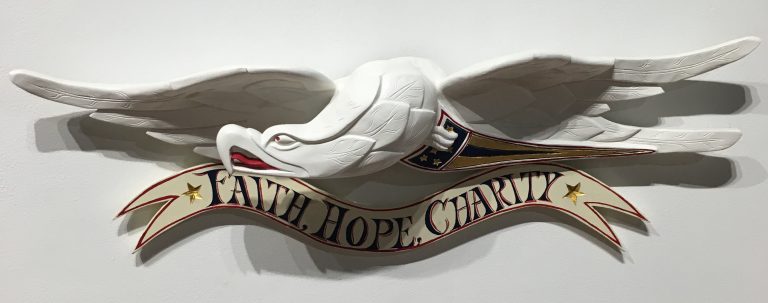
Question #18
Tobias: What is you tool sharpening regime?
William: I really hardly ever actually sharpen my tools!
99% of my tool touch-up is done on a honing machine that I made and will soon be bringing to market. I developed the machine as a natural evolution to keeping my carving tools sharp. It has MDF wheels which are impregnated with my own compound made from chromium oxide and tallow. I shape the wheels to accommodate various carving tools and mount them on a buffing machine arbor.
All I need to do is touch the edge to the wheel for a second and I am good to go. When a chisel or plane blade starts to drag, I touch it to the spinning wheel. With this process, I do not need to go near sharpening stones for ages at a time. When I do need to work on a stone, it will usually only be a few strokes on a 4000 grit or 8000 grit whetstone. Attached to my workbench is a horse-butt leather honing strip, on which I give a tool a few passes when needed.
Of course, if an edge is nicked or in really bad shape, I’ll go to a grinding wheel and work through the diamond or whetstone grits to sharpen it. I do all my sharpening free-hand. I am sure that I have read about and tried every sharpening method known to man! Sharpening is something that can be incredibly confusing to woodworkers. Now, I just don’t think about it.
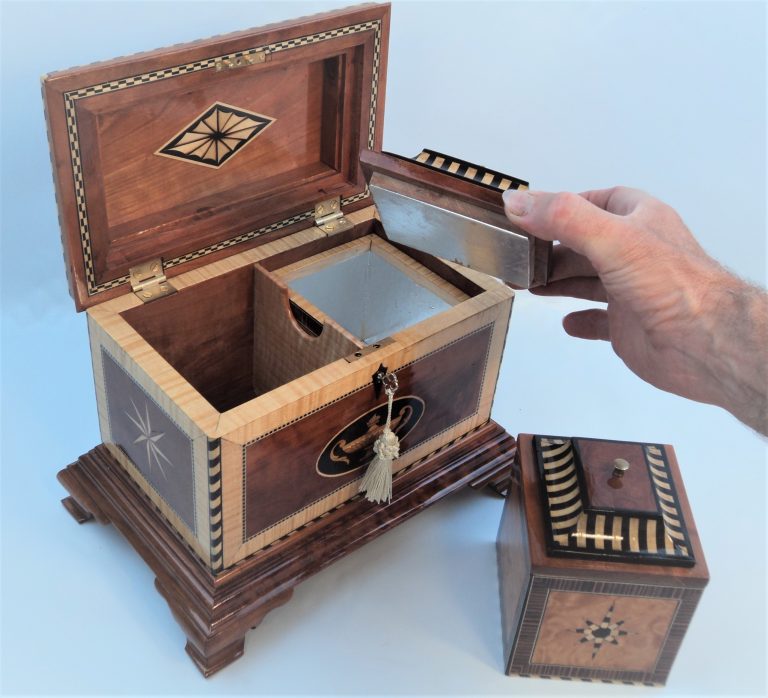
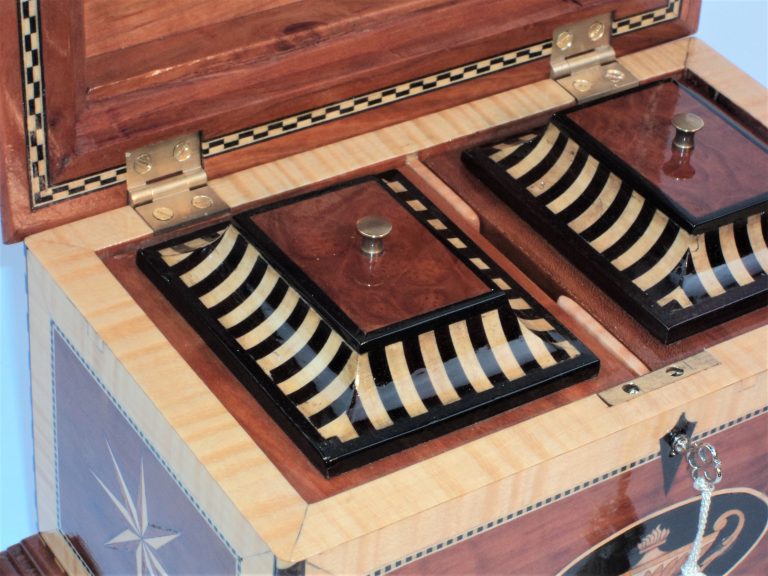
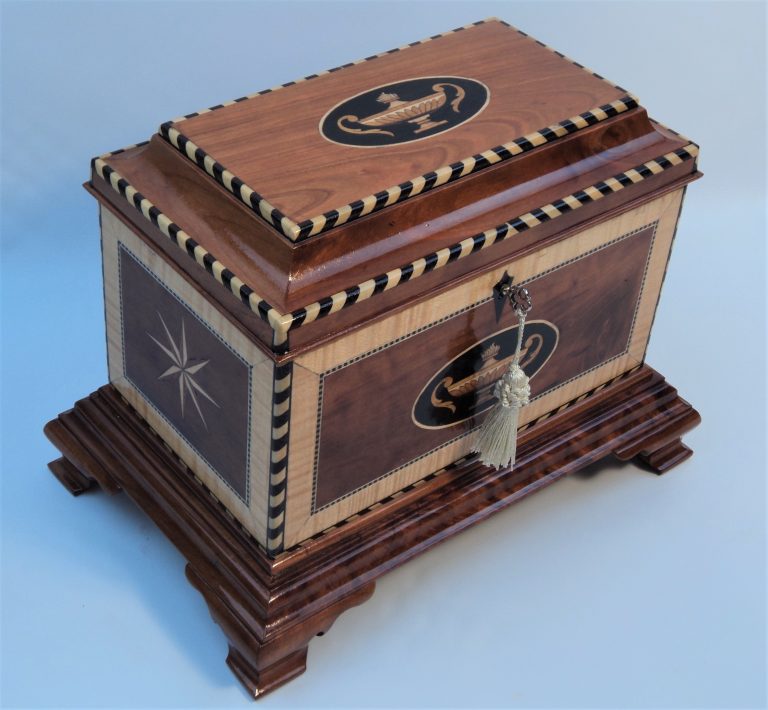
Question #19
Tobias: What custom jigs or tools have you developed for your woodworking?
William: I have all kinds of custom tools and jigs. I am always thinking of ways to make my processes easier, faster and safer.
For example, I found that cutting the sole off of roller blades makes a wonderful steady rest for turning thin parts, such as Windsor chair spindles.
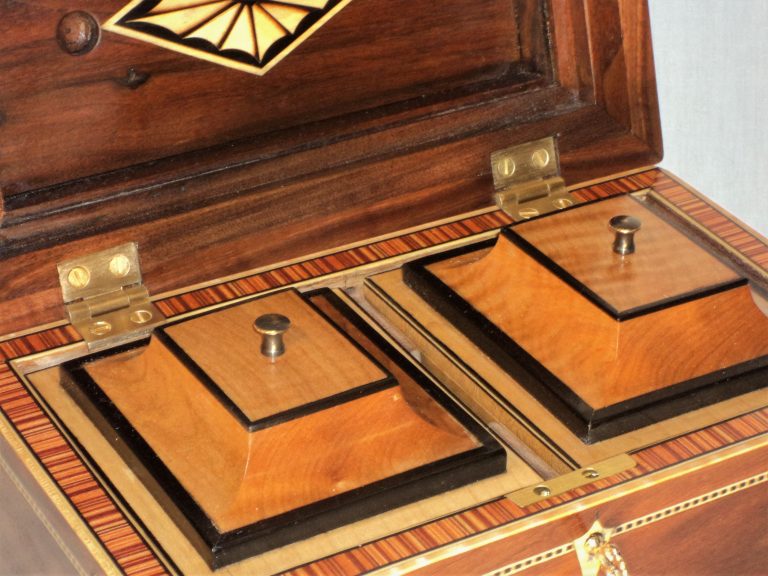
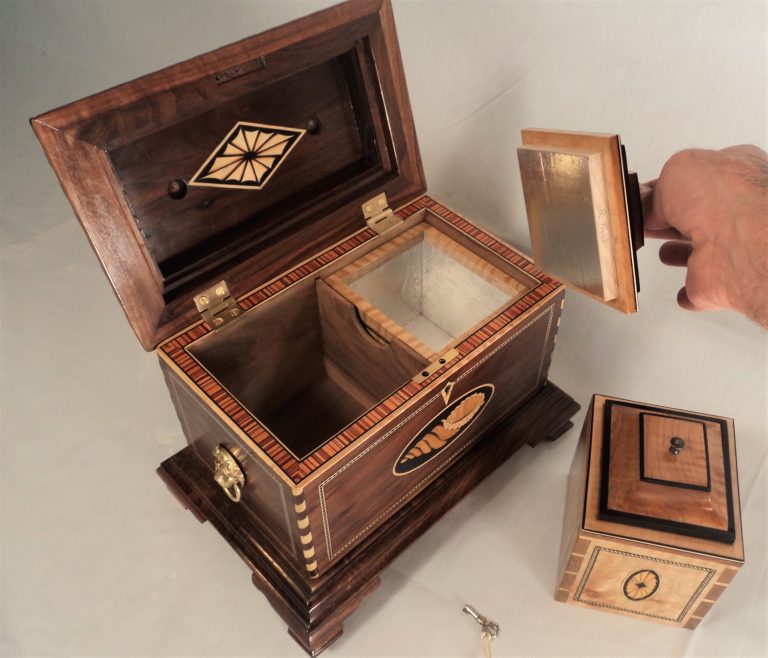
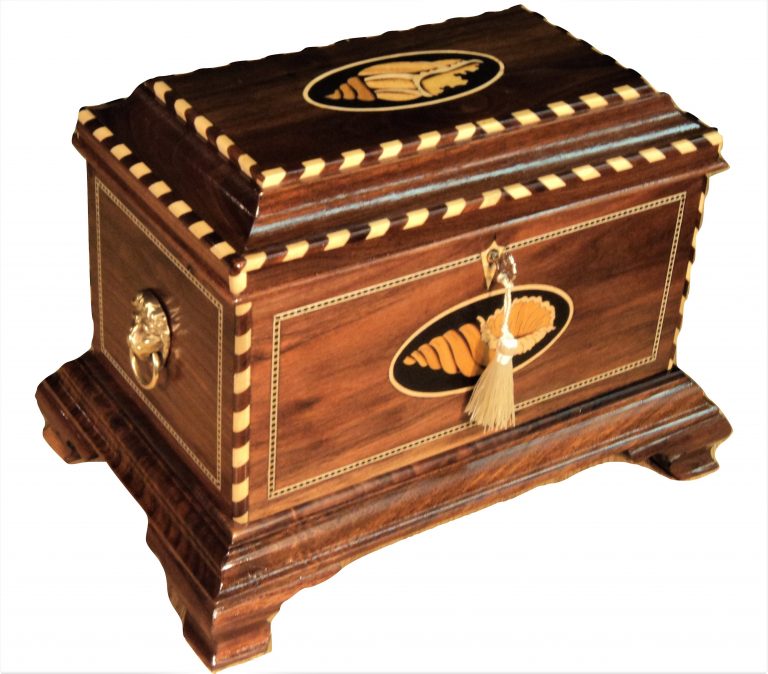
Question #20
Tobias: What is the next piece you are going to build and why?
William: I have another Bellamy Eagle commission currently on the go, as well as an order for a Thomas Jefferson Lap Desk that is going to an antiquarian bookseller in Alexandria. I often make duplicates that are available for sale on my website. as well as building a number of pieces on spec that go to various galleries.
Generally, I prefer to incorporate new techniques and learn new skills with each piece I build. I really enjoy the challenge of pushing myself out of the comfort zone and learning new things.
For example, I recently completed two Southern Cellarettes. For a long time, I had an idea floating around in my head for making bold striped moldings. I did not know how I was going to accomplish this, but had a clear picture of what I wanted the end result to be. I tend to just plow in and try to figure out a way to do something. Many times I have had to learn the hard way through various dead-ends, but more often than not I usually come upon a good way to achieve the result I am aiming for.
I have also wanted to make the Walker tea table featured at MESDA for some time, as I love the carving in the piece.
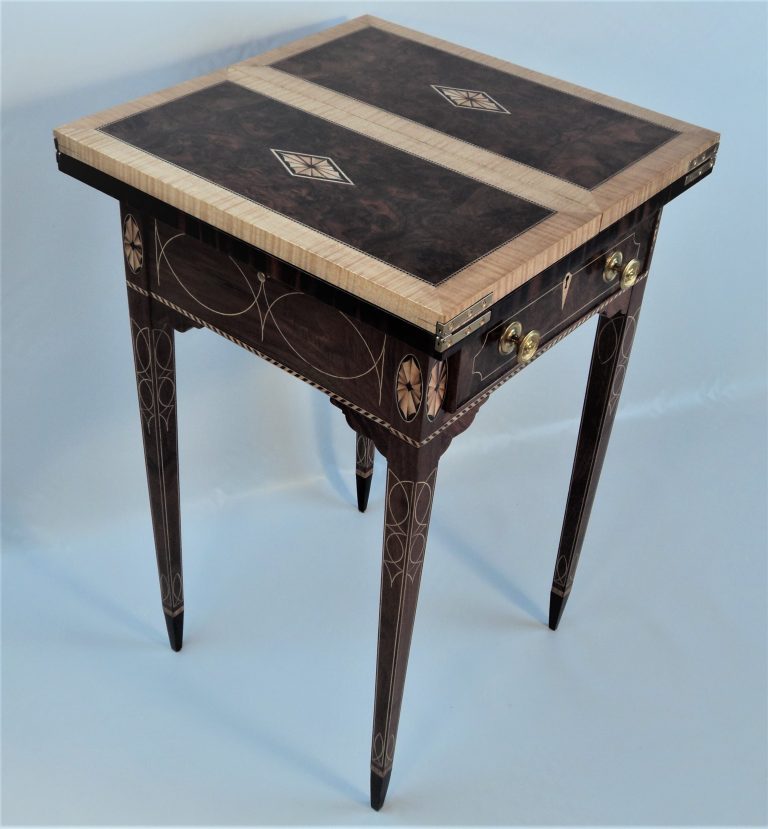
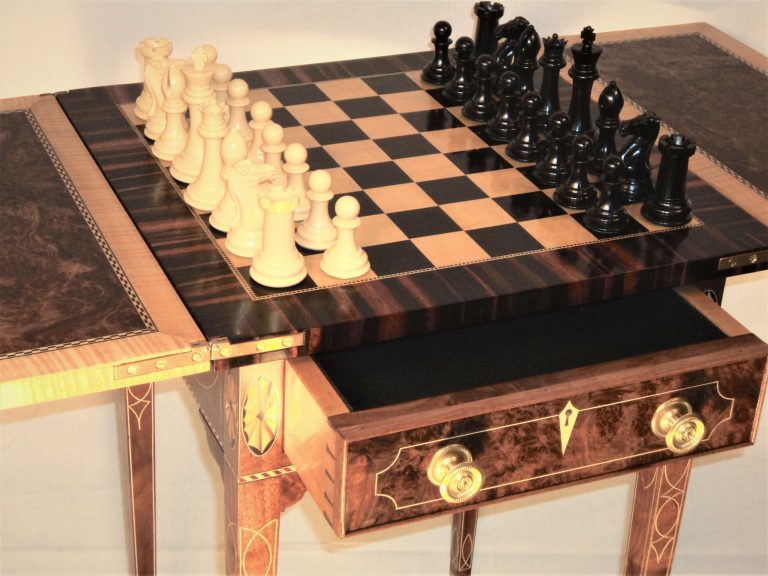
Tool Wishlist
- Any high-end small-maker woodworking tools, especially hand planes
- Anything made by Lie-Nielsen Toolworks!
- 12′ Jointer
- 20″ Planer
There is a growing number of small outfits now making incredible quality hand tools. I love using their tools, but many are becoming difficult to afford.
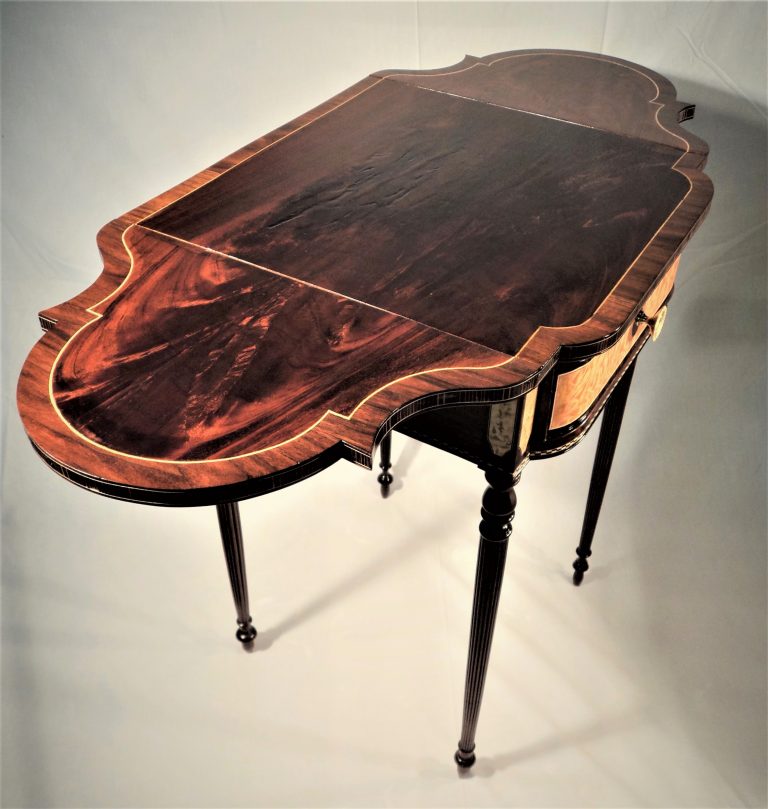
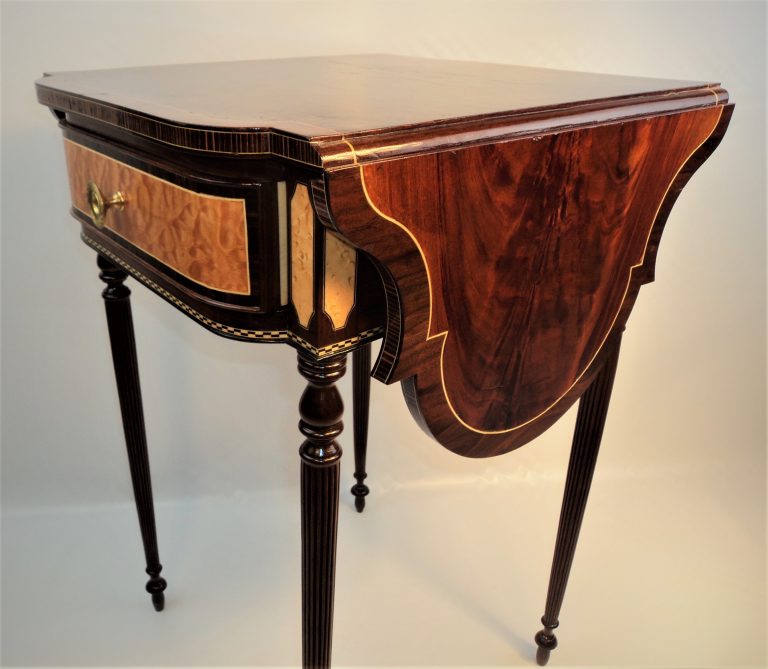
LUMBER Wishlist
- A large stash of Cuban mahogany!
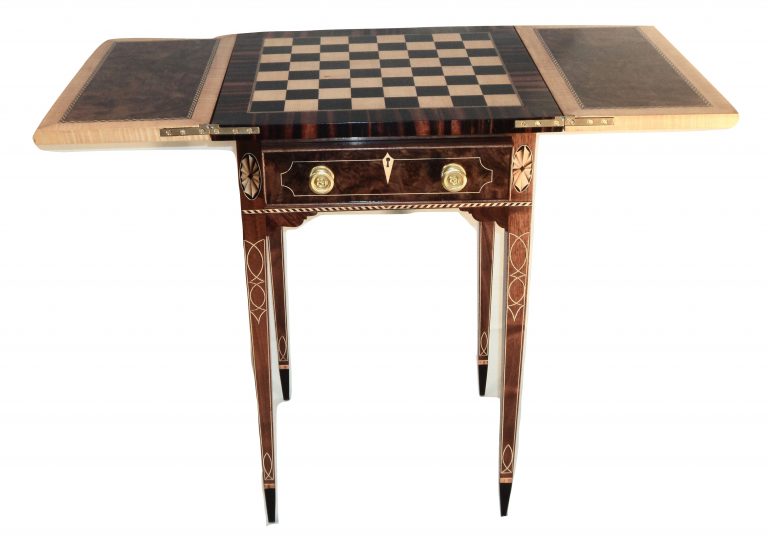
Maker with whom I would love to spend quality time
- Andrew Crawford – UK Boxmaker
- Frank Strazza – To make a workbench
- Chuck Bender – To make a Philadelphia Highboy
- Ray Journigan – As above, or any highly carved pieces
- Alf Sharp – Making a a highboy with lots of carving
links
- Woodworking School: www.mainecoastworkshop.com
- Website: www.lineandberry.com
- www.sapfm.org (Society of American Period Furniture Makers)
- Instagram Feed: www.instagram.com/williamfrancisbrown
- YouTube: Music Channel – www.youtube.com/user/wfbrown1234
- YouTube: Wood and Shop Video – Tour of William’s workshop
- YouTube: Wood and Shop Video: William Brown’s Incredible Furniture Tour
- YouTube: Wood and Shop Video: Amazing Tree of Life Chests with William Brown
It has been an honor to have been able to interview the indomitable William Brown. He shares his passion infectiously and we wish Bill and the Maine Coast Workshop woodworking school every success.
I am sure that Bill will have his hands full along with world class woodworking instructors Alexander Grabovetskiy, Alf Sharp, Mary May, Frank Strazza, Marty Leenhouts, Shawn Murphy, David Douyard, Graham Blackburn, Matt Kenny, Peter McKenna and Ray Journigan at the Maine Coast Workshop in picturesque Camden.
We wish The Maine Coast Workshop every success going forward and hope to welcome Bill to Rare Woods USA very soon.

Bill, I would add to the compliments, praise, and encouragement of all the others that I have seen observing your incredible talent and works. I desire to work and strive to the same level of expertise and precision in my work that you are exhibiting in yours now. I also appreciate and share the same desire to be expert in all aspects of woodworking and not just be known for specializing in one, i.e. Windsor Chair making, or Roubo Bench building, etc. But, in all this I would charge you with what I constantly remind myself with, that is, the need for humility. Notoriety can breed the wrong kind of pride, but in the same breath you can be justifiably Proud of all the incredible and beautiful work(s) that you done! John T. Willette
Thanks so much for your comment John.