Welcome to the Rare Woods USA Woodworker Sessions interview series. Here, we hope to discover more about what makes our woodworkers tick, how you became involved in the craft, how and why you build your pieces and maybe learn a few secret techniques and tips along the way!
Our interviewer, a woodworker since the age of 8, Tobias Lochner is no stranger to the workshop. Find out more about him here.
Our sincere thanks go to Christina Vincent (www.christinamvincent.com) of North Haven in Maine for sharing her passion and talent with us in the 6th issue of the Woodworker Sessions USA.
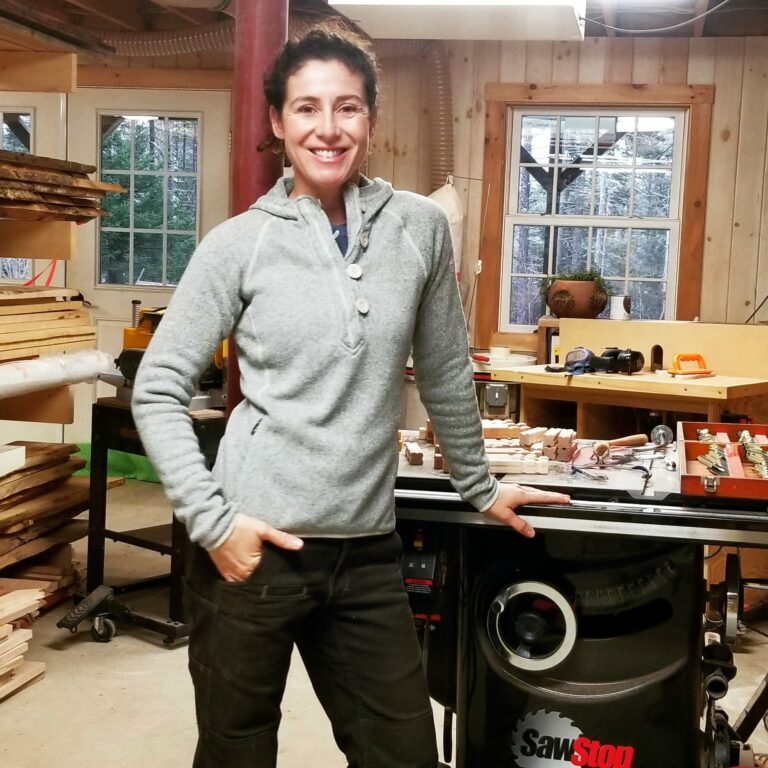
Question #1
Tobias: Hi Christina. Please tell us about yourself, your family and your career.
Christina: Hi. I’m Christina, designer and maker of Christina M. Vincent Fine Woodworking and Northshore, a garden and design company. I grew up in Monot, Maine. As much as I loved Maine, I could not wait to get away, go to college and travel. When I was in college, I decided to study abroad in Australia and simply fell in love with experiencing new cultures and places. Later, I was in Vermont working for an interior design company, when a friend asked me to come to North Haven for the summer and I am still here, 15 years later! I tried my hand at carpentry and it evolved over time into fine woodworking.
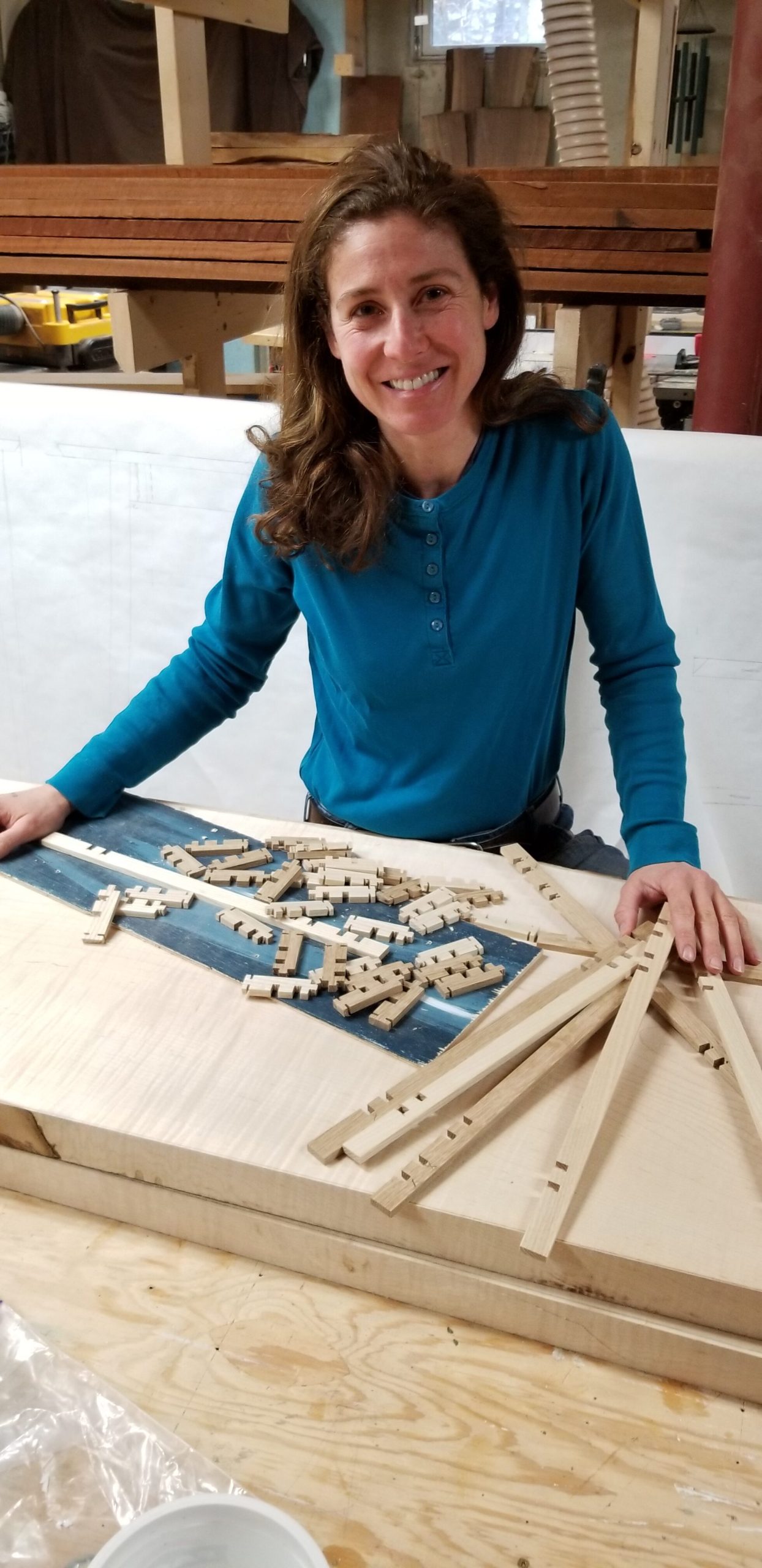
Question #2
Tobias: How did you get started doing woodwork and how long have you been a woodworker?
Christina: When I moved to North Haven, there wasn’t much need for my interior design and art background. Lobstering and carpentry were the jobs that paid the best. Since I had come to North Haven in the summer, I tried lobstering, which really did not grown on me, so I went into carpentry. That seemed to fit. For a few years I worked for a small company, built my own home, moved on to a larger company and after another few years, things evolved to the extent that I was doing mostly finishing work.
I wanted to incorporate my art and design background into my current work, but as a carpenter working mostly with power tools and nail guns, my creative urges were rather limited, so I decided to change course. I began by starting a garden design company and reached out to The Centre for Furniture Craftsmanship to further my education in fine woodworking. This was 2013 and I never looked back! I now have my own garden and design company and create custom woodworking pieces.
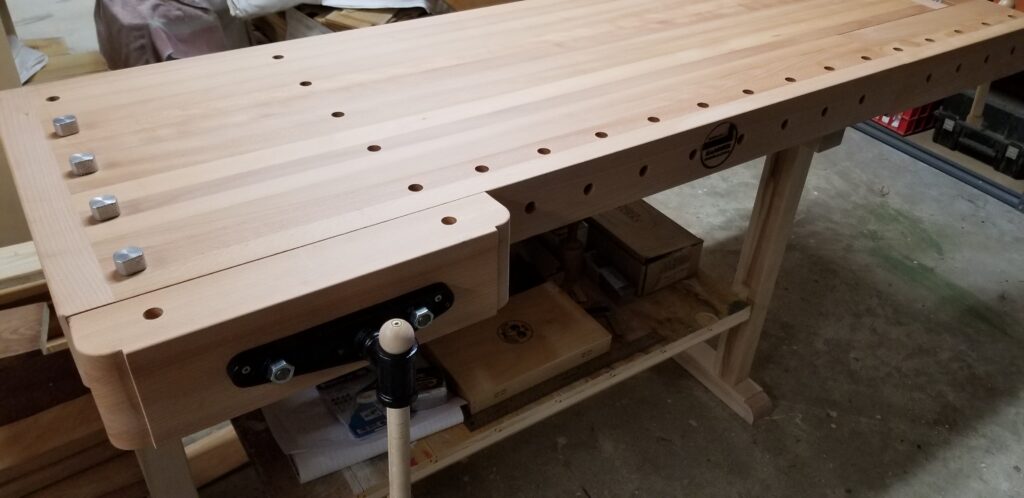
Question #3
Tobias: Which was the first item that you made and which is your favorite piece?
Christina: The first furniture that I ever made, was an outdoor table and chair set for the home were I was living when I first arrived on North Haven. The carpenter that I was working with was going on vacation and I asked to continue working in his shop. He agreed, although with some hesitation! I made the furniture from Maple branches and leftover pine boards for the seats and table top. The whole lot was held together with a lot of fasteners! I really loved this set and at the time as a complete novice, I was really proud of it!
Fast forward 12 years to the three month intensive course at the Centre for Furniture Craftsmanship where I created the Blue Heron stools that I am most proud of to date. At the school, there are always sharp blades, someone is always fine tuning all the machines, you have time to really create and there are many people to bounce ideas off – true bliss for any creative woodworker!
I created this pair of stools with a bent lamination supporting the frame, a coopered seat and great lines for aesthetic appeal. I long for the available time to re-create them.
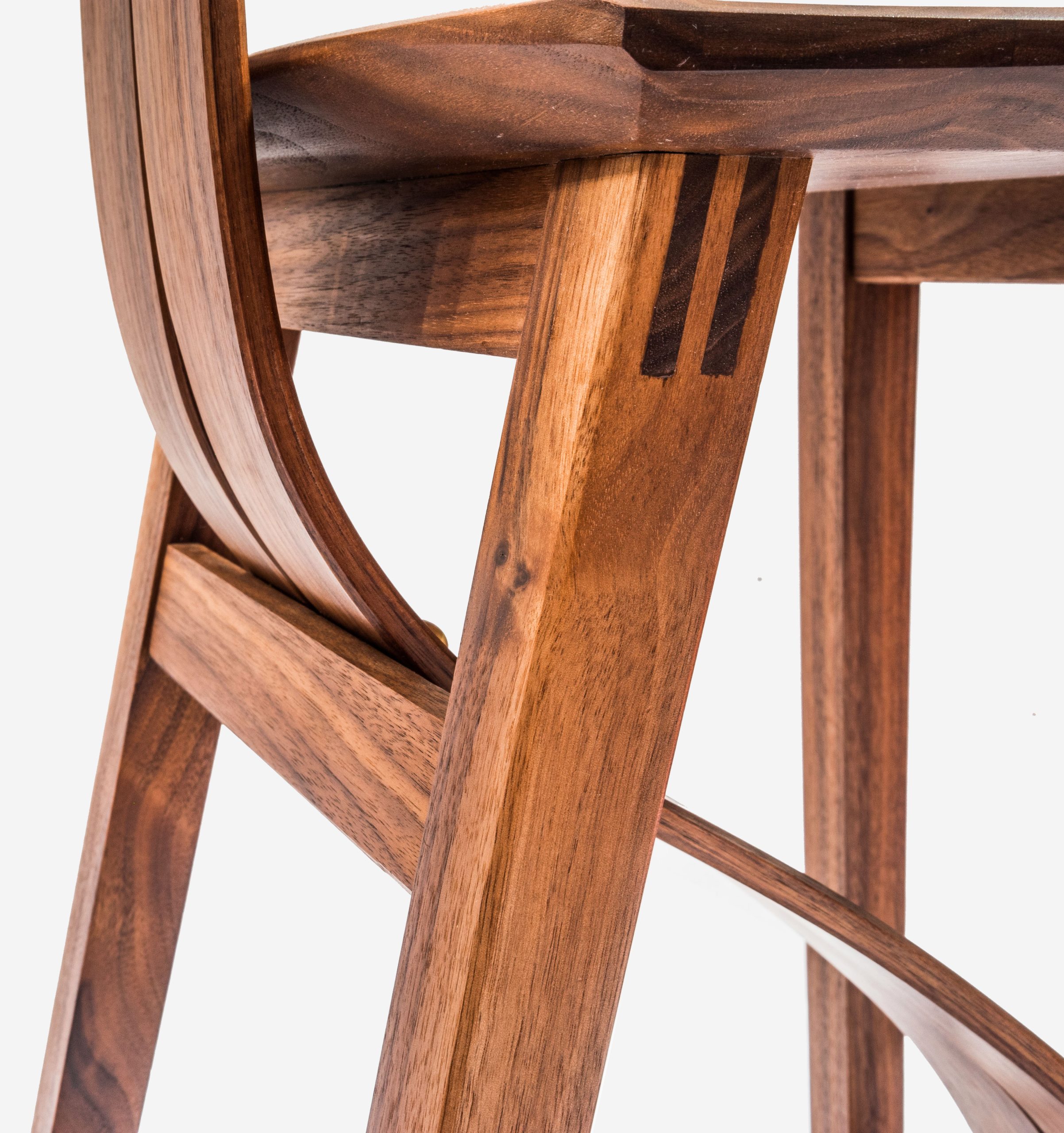
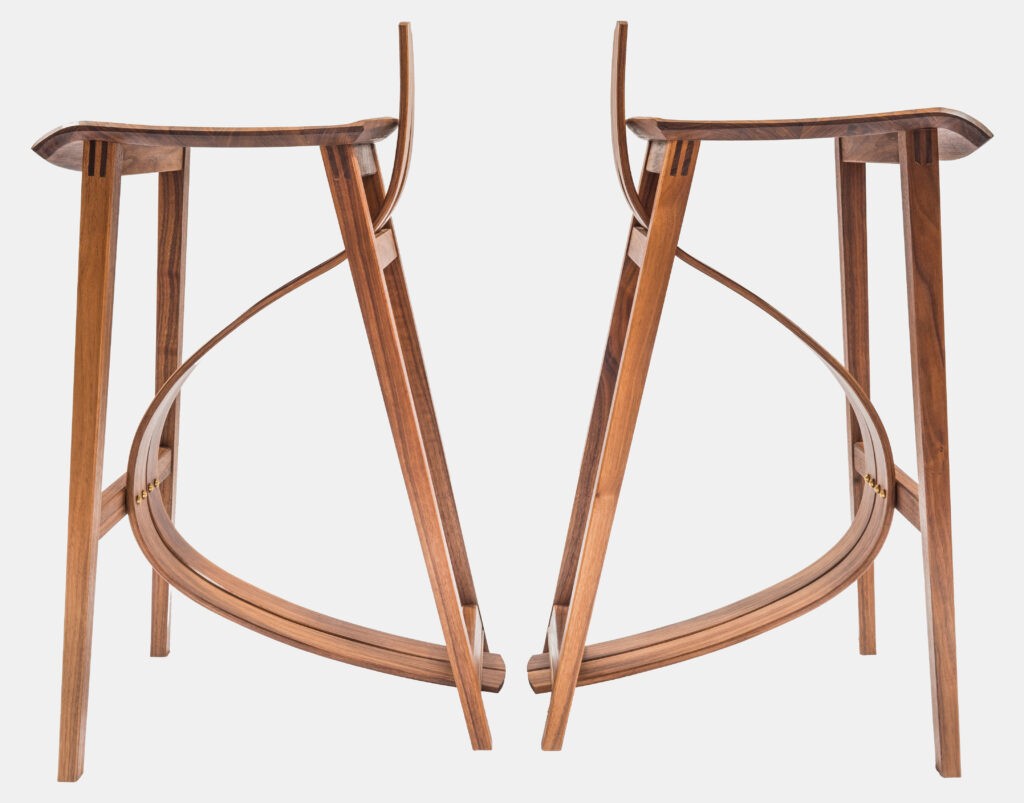
Question #4
Tobias: Which style of furniture do you enjoy the most?
Christina: I would say Scandinavian if I was forced to make a choice. My intentions of functionality, simplicity and minimalism, parallels that design style the most. However, I draw my inspiration from many different areas and prefer not to box myself into any particular style genre. I feel that my pieces are versatile, useful and long-lasting and hopefully they intrigue interest and engagement without being overwhelming.
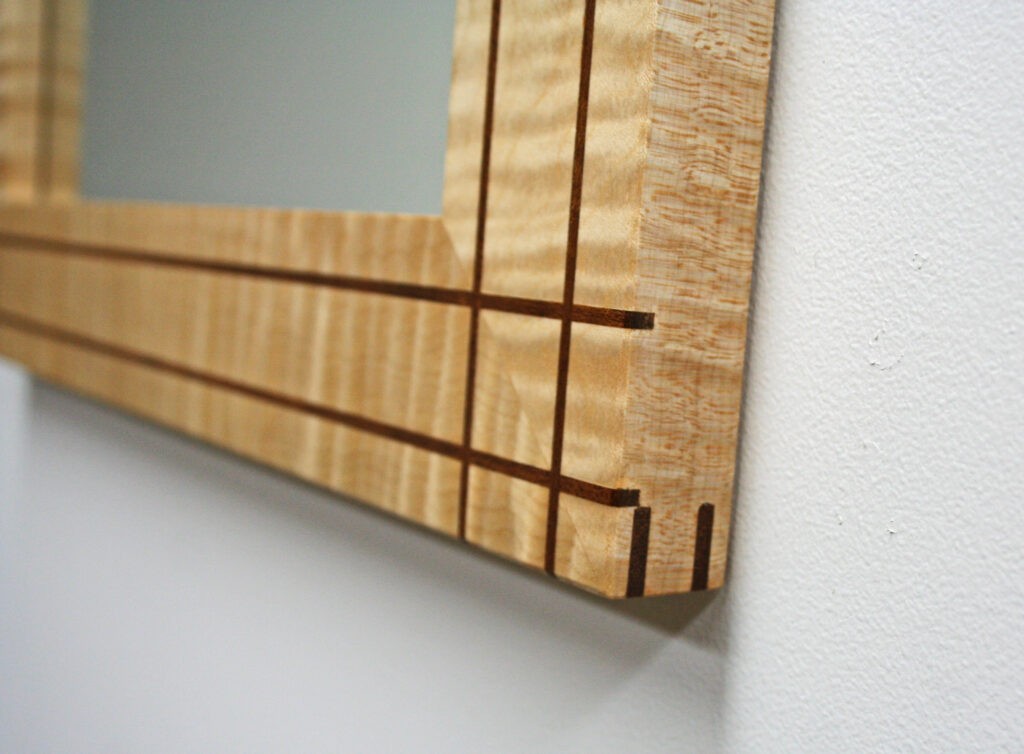
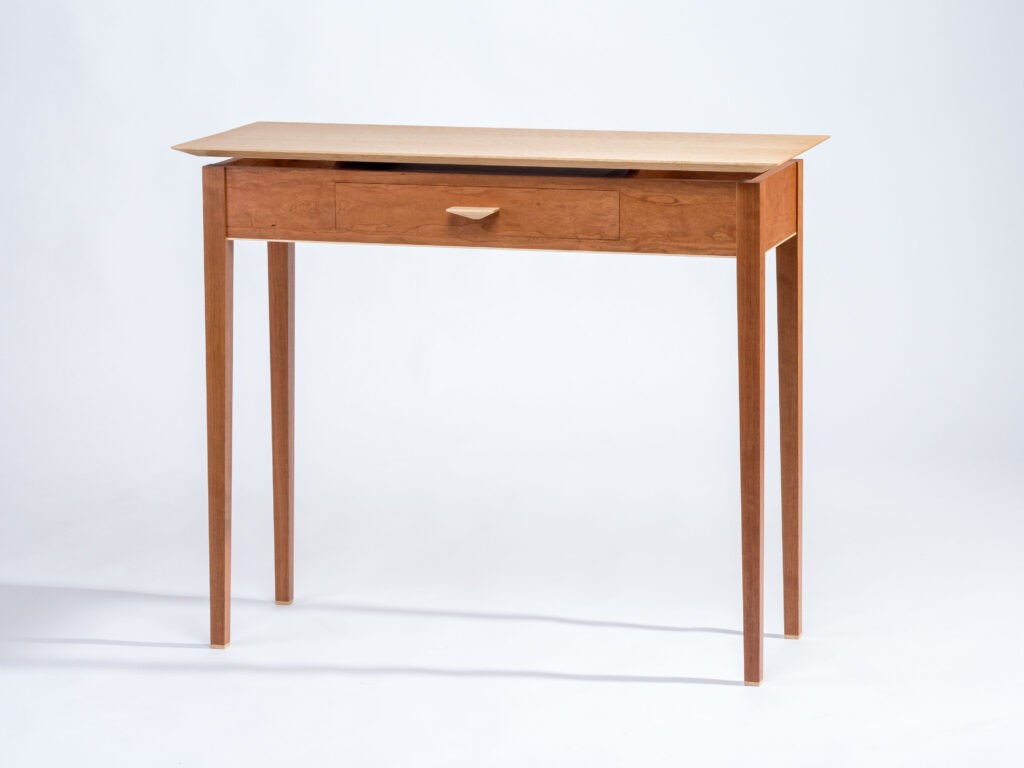
Question #5
Tobias: Which are your favorite local and exotic timbers to work with?
Christina: My favorite native woods are Black Walnut, Curly and Birdseye Maple and Ash.
Zebrawood is so much fun in some applications. I really enjoy the understated warmth and simplicity of European Beech and adore working with Sapele.
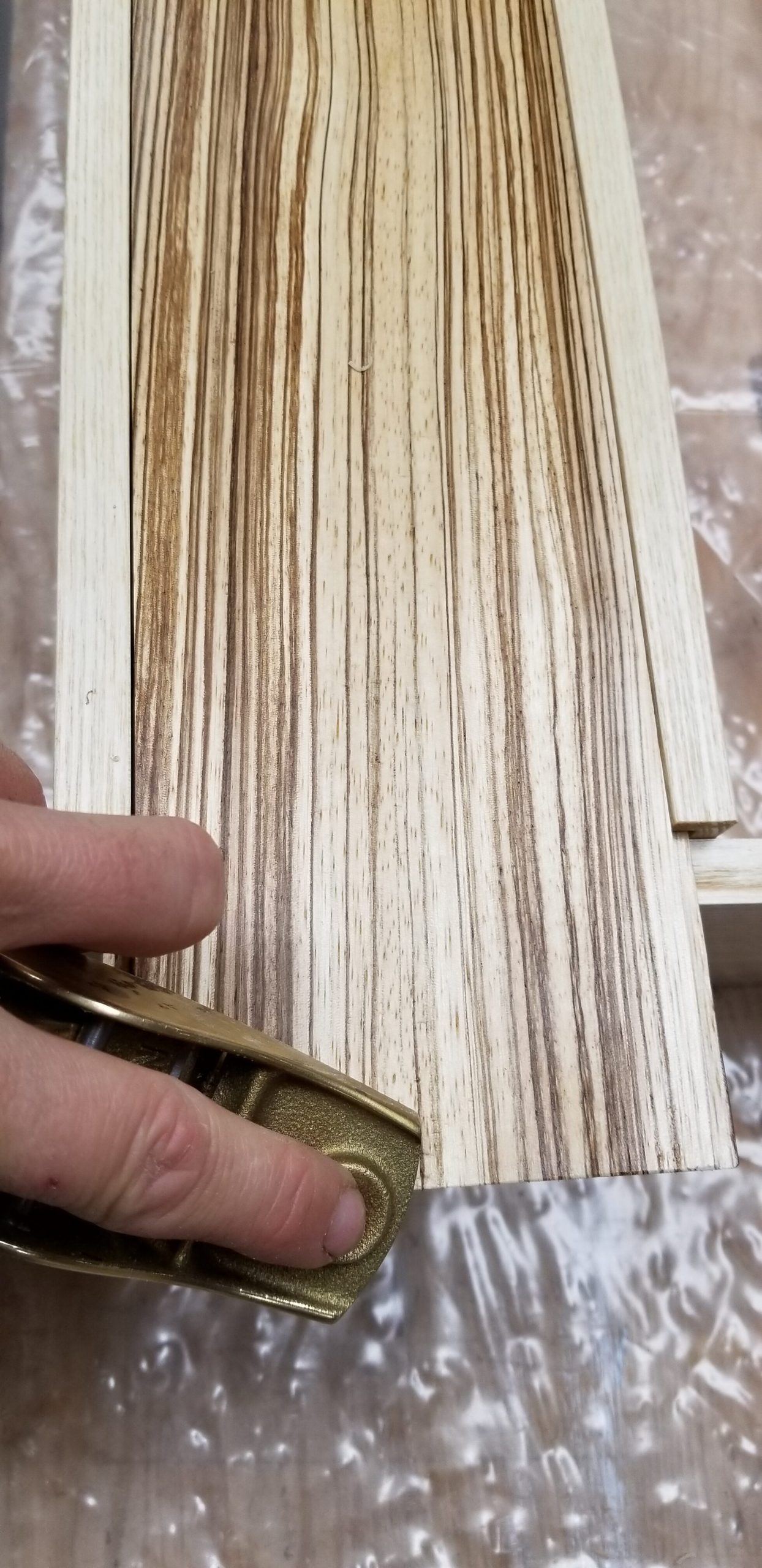
Question #6
Tobias: Please list your most used hand tools and tell us why the are your “go-to” tools.
Christina: As a fine woodworker, I would not be able to function without chisels, both bench work and carving, I use them daily for creating and fine tuning joints. My Glen-Drake Tite-Mark gauge is absolutely essential for laying out mortise and tenon joints. Also essential are my Starrett combination squares (I always have my 4″ handy for measuring and setting depths). My #102 Low Angle Block Plane is crucial in my work day, for trimming, and cleaning up, especially in tight areas. Last but not least are my Veritas Round Bench Dogs. I absolutely love them as the grip really well, holding my projects securely as I work.
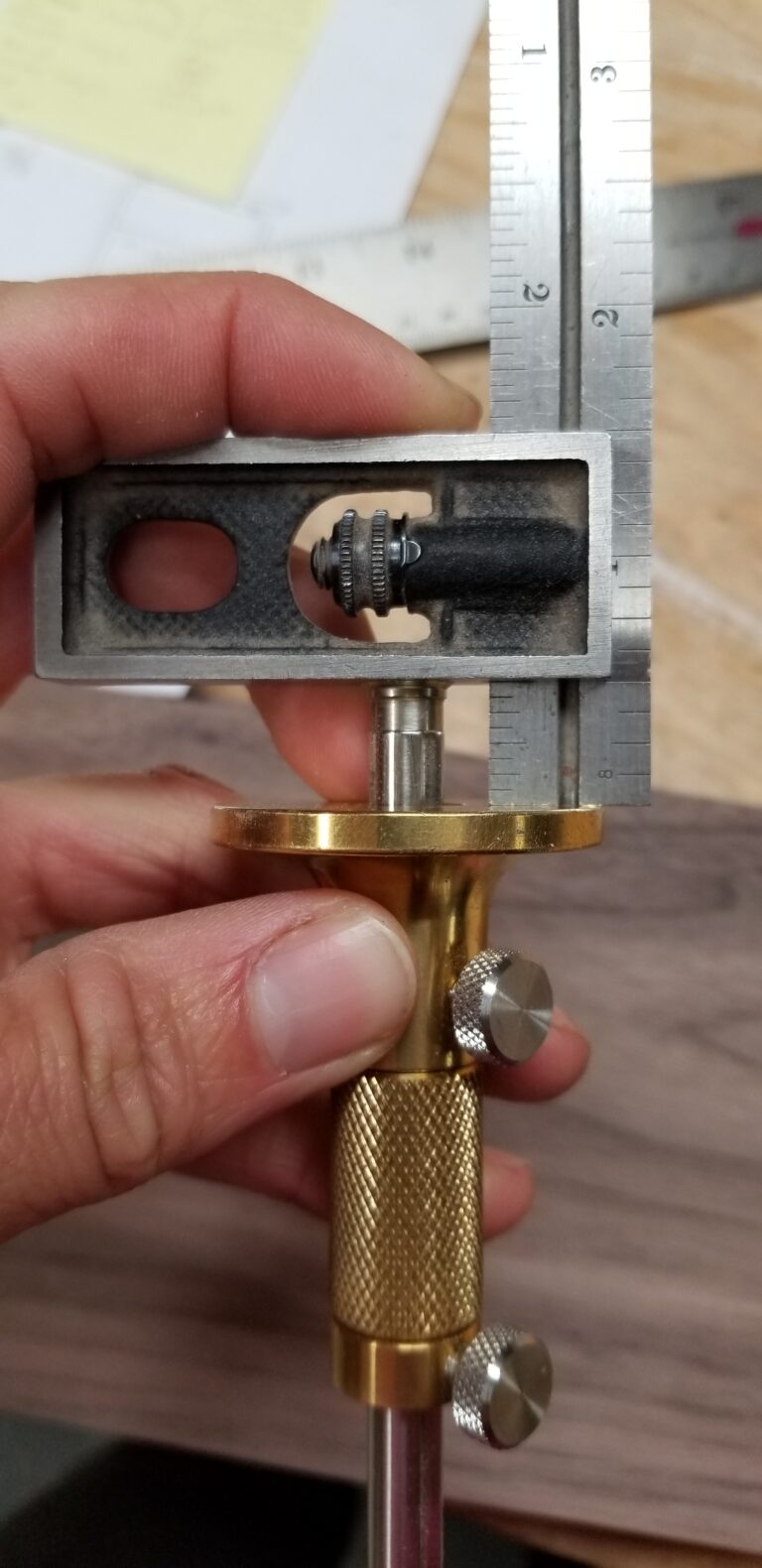
Question #7
Tobias: Can you list your favorite power tools and machines and tell us why?
Christina: The main powered tools in my shop are my Jet bandsaw, Sawstop table saw, Jet 8″ jointer, DeWalt 12″ planer and DeWalt hand-held router.
When making a piece of furniture, you are basically going from a large piece of wood and cutting it into smaller pieces and for me, the bandsaw is the first stop on that journey. Second, you need to flatten the boards using the jointer to removed twist and warp. Next up to achieve the desired thicknesses of my boards is the thicknesser.
When all of these processes are complete, I lay out whichever joints I am going to employ and most of the time I use the table saw to mill them.
The hand-held router is perfect for edge-routing, inlay work and keyhole slots for wall mounted pieces.
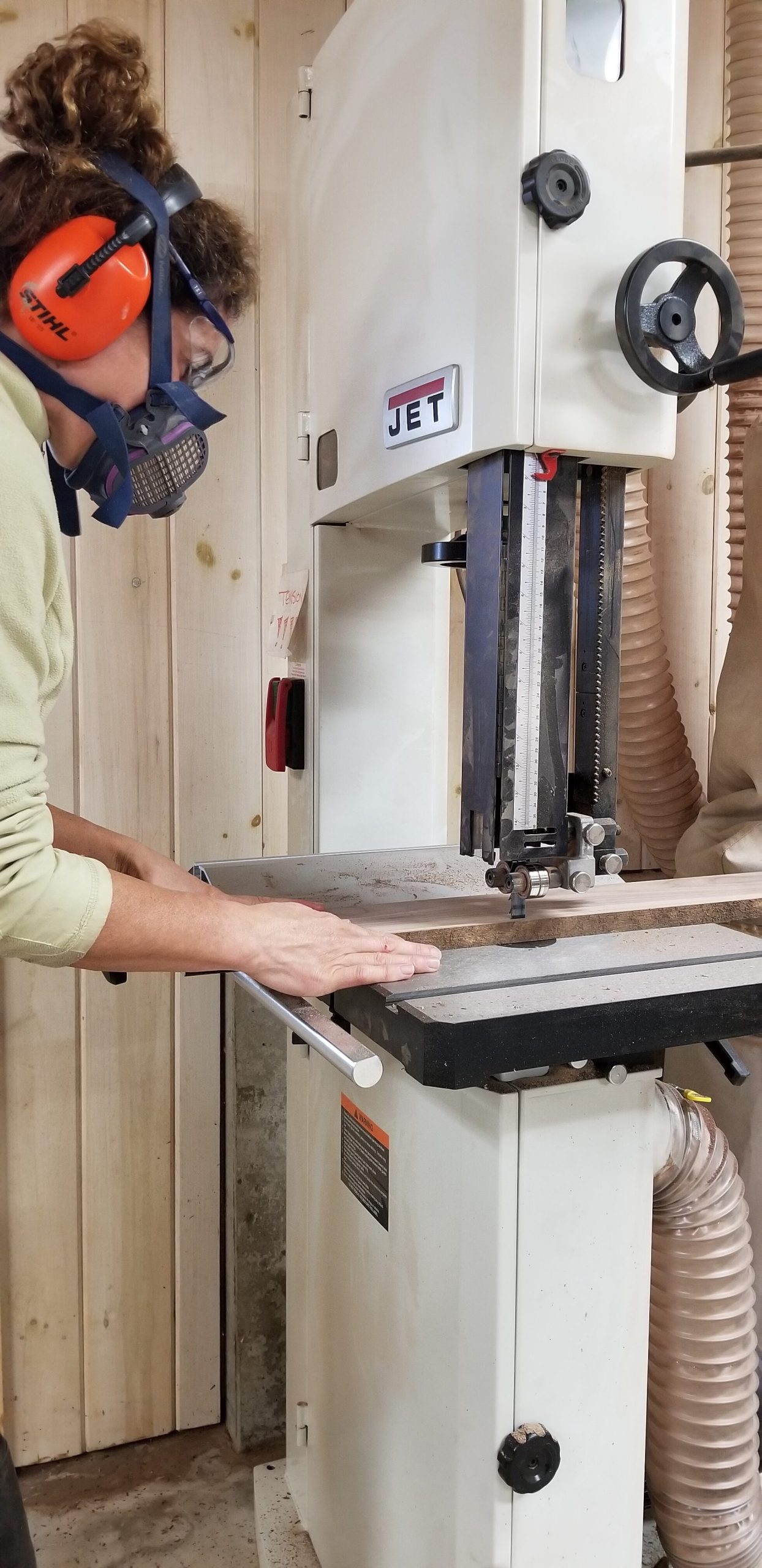
Question #8
Tobias: What is it about working with wood that you find the most enjoyable?
Christina: I that that it is the fact that you are working with a natural medium. It has unending characteristics and unique qualities such as color, texture, pattern, and in some cases has a scent. Wood is so incredibly versatile, it can be used in linear form , or manipulated to curve and bend with endless permutations.
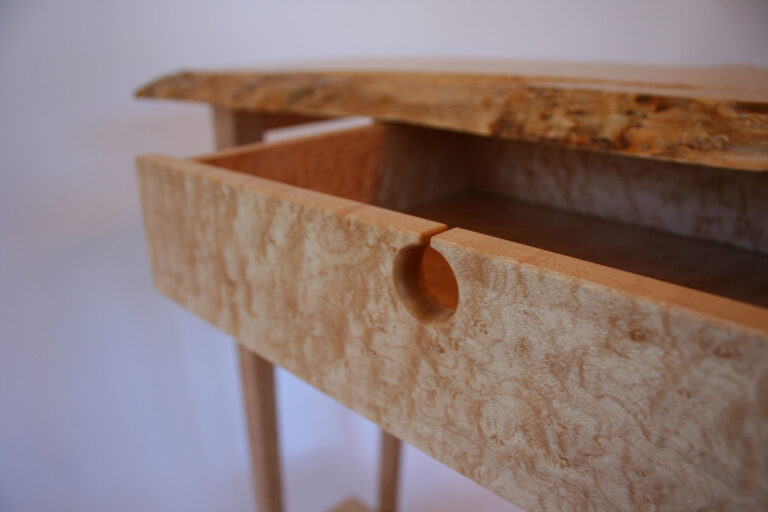
Question #9
Tobias: What type of workshop do you have?
Christina: At present, my shop is small, it is in my daylight basement. The flow is not great as the stairs tend to impede workflow quite a bit, however I have learned to work around them. Quite honestly, when I built my house, I really did not think that it would have a workshop as I was not at that point yet. I now utilize the stairs by having my lumber rack underneath them.
One side of the workshop houses my power tools and the other side has my workbench and glue-up/assembly/finishing table. I have a dust collection system and overhead LED lights combined with the daylight windows and windowed double door providing good illumination which is extremely important.
I built my assembly table at a height that is really good for me and have a wonderful Hoffman & Hammer workbench. I would recommend this bench to anyone as it is solidly built, heavy and durable.
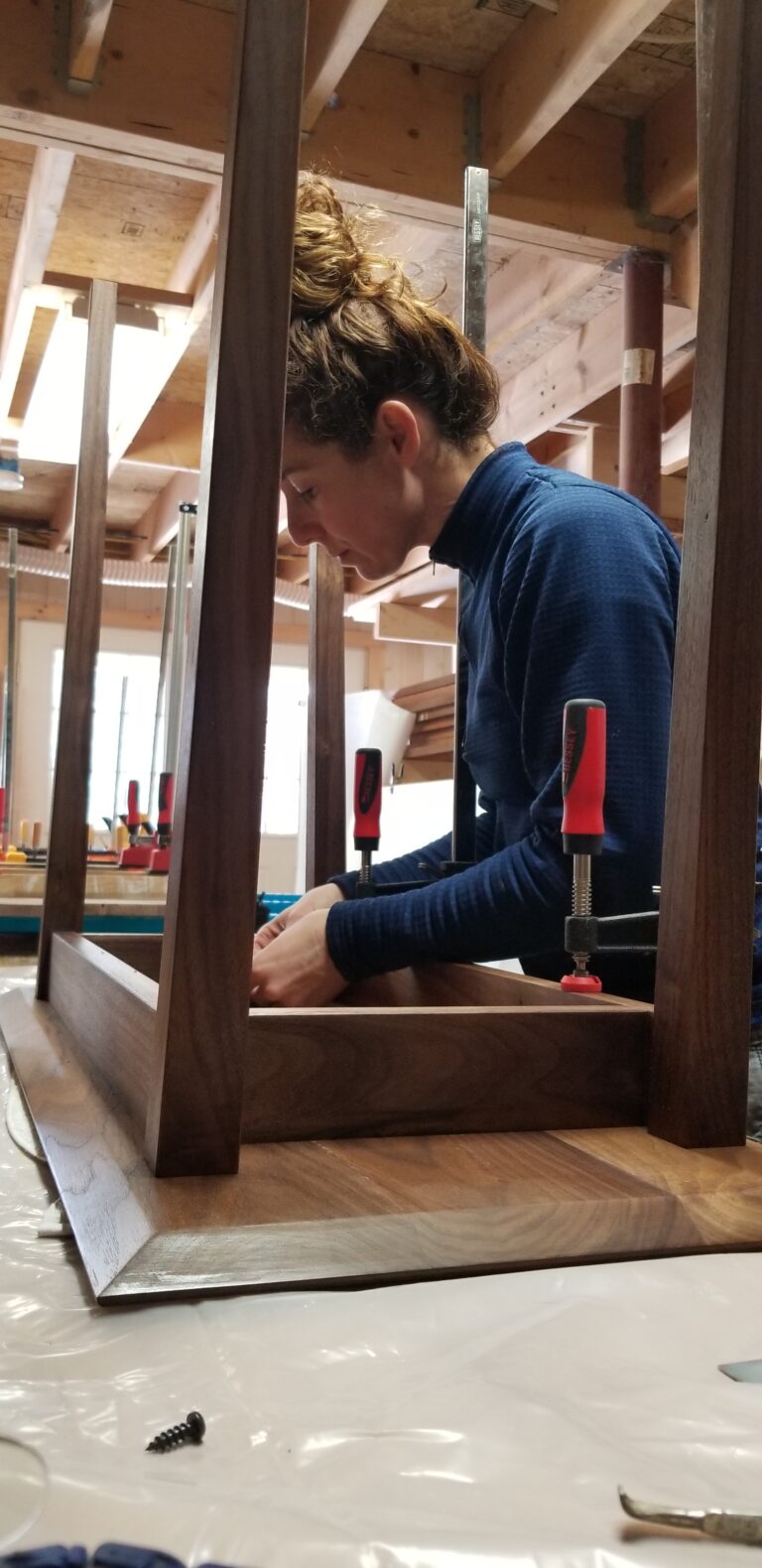
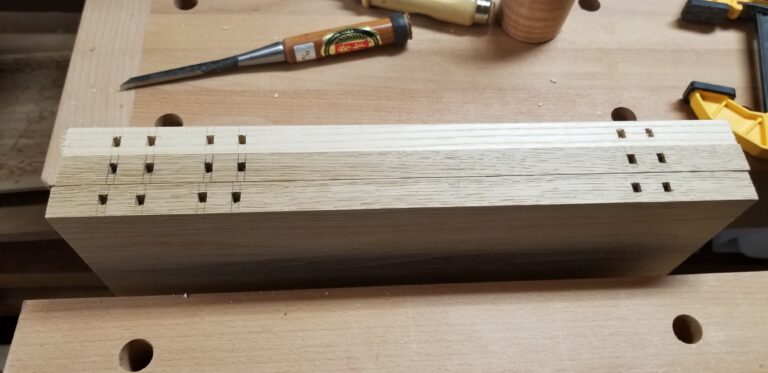
Question #10
Tobias: What is your clamp line-up and why?
Christina: In my clamp collection I have quite a few different styles of clamps.
Bessey K-Body clamps are my favorites as they are easy to adjust, tighten really well and do not slip or loosen, however they are sometimes not appropriate for the project at hand, hence the others in my arsenal. I use Rockler Sure-Foot Clamps which are excellent for glueing up wider sections. I also use DeWalt trigger clamps which are remarkably handy when you need a quick hold and might only have one hand free! I also utilize Bessey F-Style clamps. I like them as they are lighter and often this can be an advantage, however if the price was better, I would definitely have more K-Body Bessey clamps.
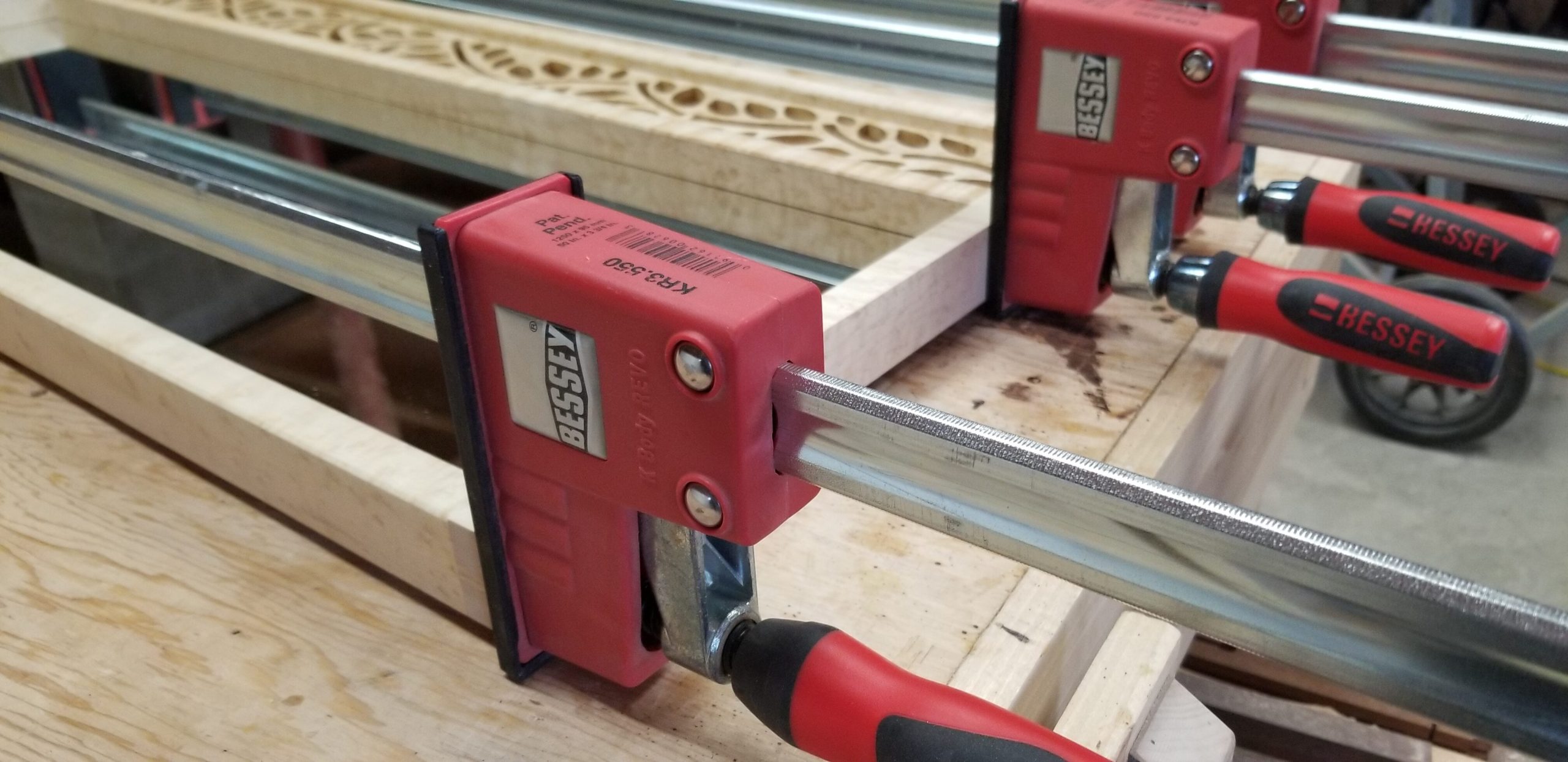
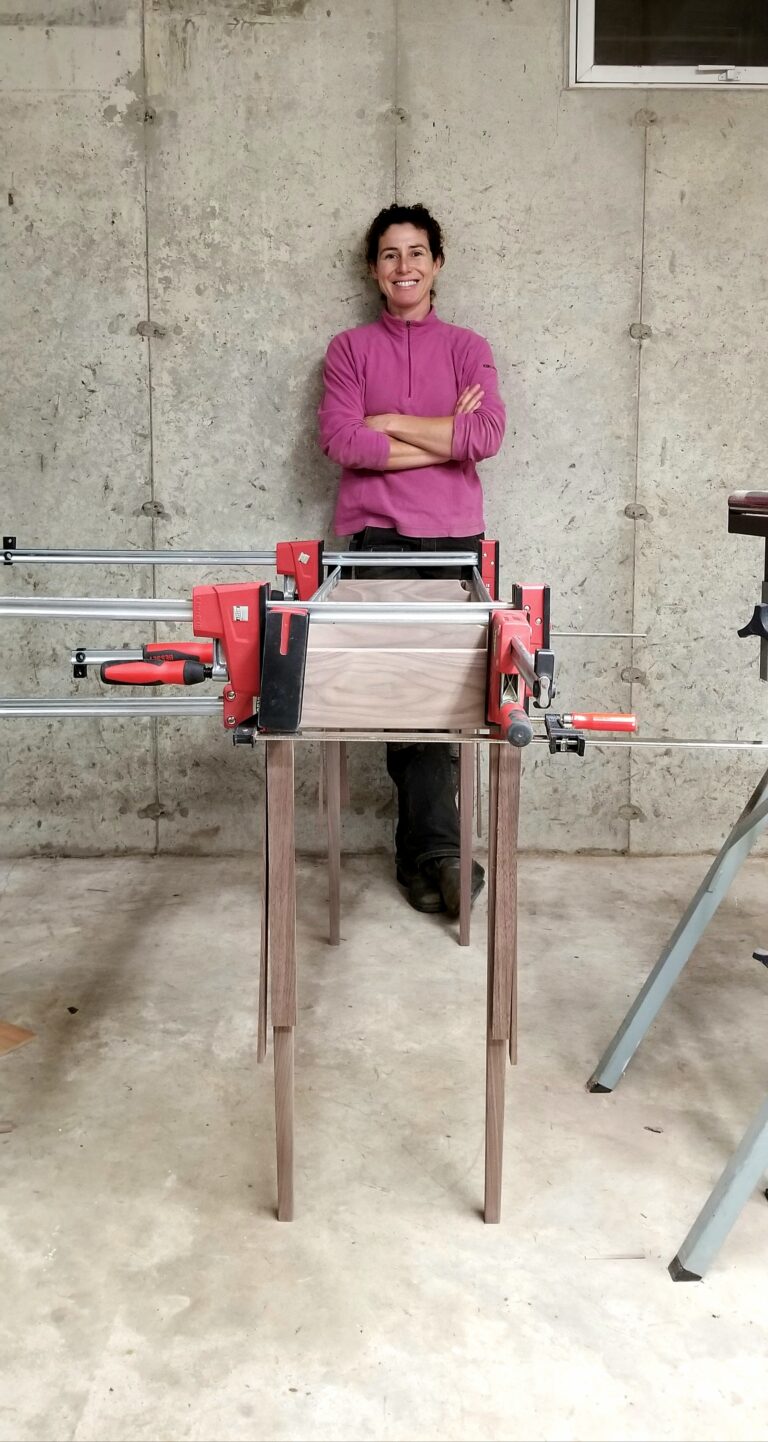
Question #11
Tobias: Which glues and adhesives do you use and why?
Christina: I mainly use Titebond I and Titebond III. The decision is mostly based on whether the joints need to be waterproof or not. I also use Titebond Dark Wood glue on Walnut.
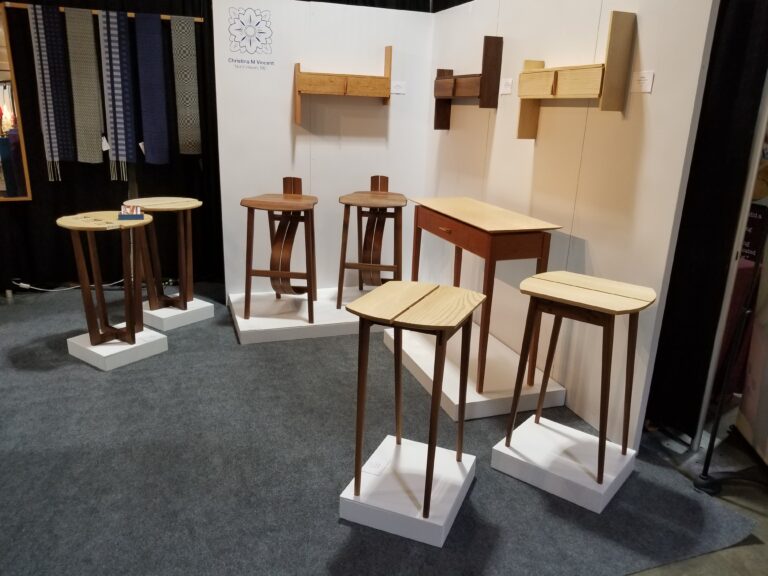
Question #12
Tobias: Which woods, local and exotic have you not yet used and why are you interested in building with them?
Christina: As I continue to learn and try different techniques, I would like to incorporate turned knobs and handles into my work. I think that Ebony would work beautifully for this purpose. It is such a statement wood, that it could make an otherwise simple piece stand out.
Another exotic that I would be interested in trying is Yellowwood, I would like to find a few really rich pieces, as I think that it would be another fun color to play with.
Hmm….. As far as native woods go….I have worked with a very wide range, so I would pick White Oak. Not that I have not worked with this species, but have not worked with it very much. It has a nice straight grain, is pretty water resistant and is a good wood for steam bending.
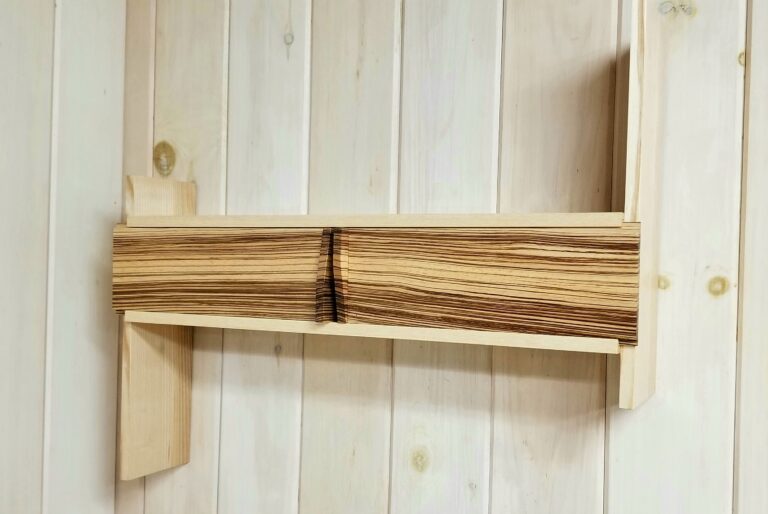
Question #13
Tobias: What and whom are your sources of inspiration for your woodwork?
Christina: I don’t really look to any particular people for inspiration. I may see something; an angle, or an aspect of a piece, something that just stands out to me, which then inspires me to create my next piece. Since plants and the outdoors is the other big part of my work, I often draw inspiration from the vast beauty of nature that surrounds me here on North Haven Island.
If I had to choose a woodworker to admire and be inspired by, it would definitely be George Nakashima. The way that he saw and created beauty and perfection in the imperfection and balance in the asymmetric was truly remarkable. He was a pioneer and shaper of woodworking as we know it today.

Question #14
Tobias: How do you design your pieces? Do you use CAD or SketchUp? Do you sketch out by hand?
Christina: In the first few years I would have an idea, really just a concept of something that I wanted to build. I would do a quick basic sketch on an 8×10 sheet of paper with rough measurements and from there on I would just wing it! Easy to deduce that there were always plenty of hurdles to overcome when things didn’t quite match up!
All in all, I got things to work out and the casual onlooker would have no idea.
Now, after my courses at the Centre for Furniture Craftsmanship, I hand draw each piece to scale. By doing so, I can avoid all the time consuming pitfalls by by having a full scale detailed plan on the bench. Drawing the piece out at full scale enables me to accurately gauge my proportions and aesthetic appeal.

Question #15
Tobias: What are your finishing regimes, which products do you use and which are your favorite processes?
Christina: I use Livos, both their interior finish and their decking oil. Livos “avoids manufacturing with pollutants and heavy metals, using only plant, earth and mineral pigments in finishes and oils”.
I like working with it because it has very low VOCs, almost no odor (the little odor that does exist is more pleasant than anything else I have used) and it produces a great end result.
When a piece is ready for finishing (final sanding is complete and the piece has been wiped down with a dust cloth and then a tack cloth), I hand-apply the finish with a lint free cloth, making sure that I coat the entire surface evenly. I then let is set for a few minutes and wipe of the excess going with the grain. I also lightly sand between coats. The second coat is applied in the same way. Prior to a coat, I check to see how the finish is looking. If I like like how the finish looks and feels, I use a white Brillo pad instead of sandpaper before the final coat. If I am not happy with the result, I repeat step 2 before moving on to the final coat.
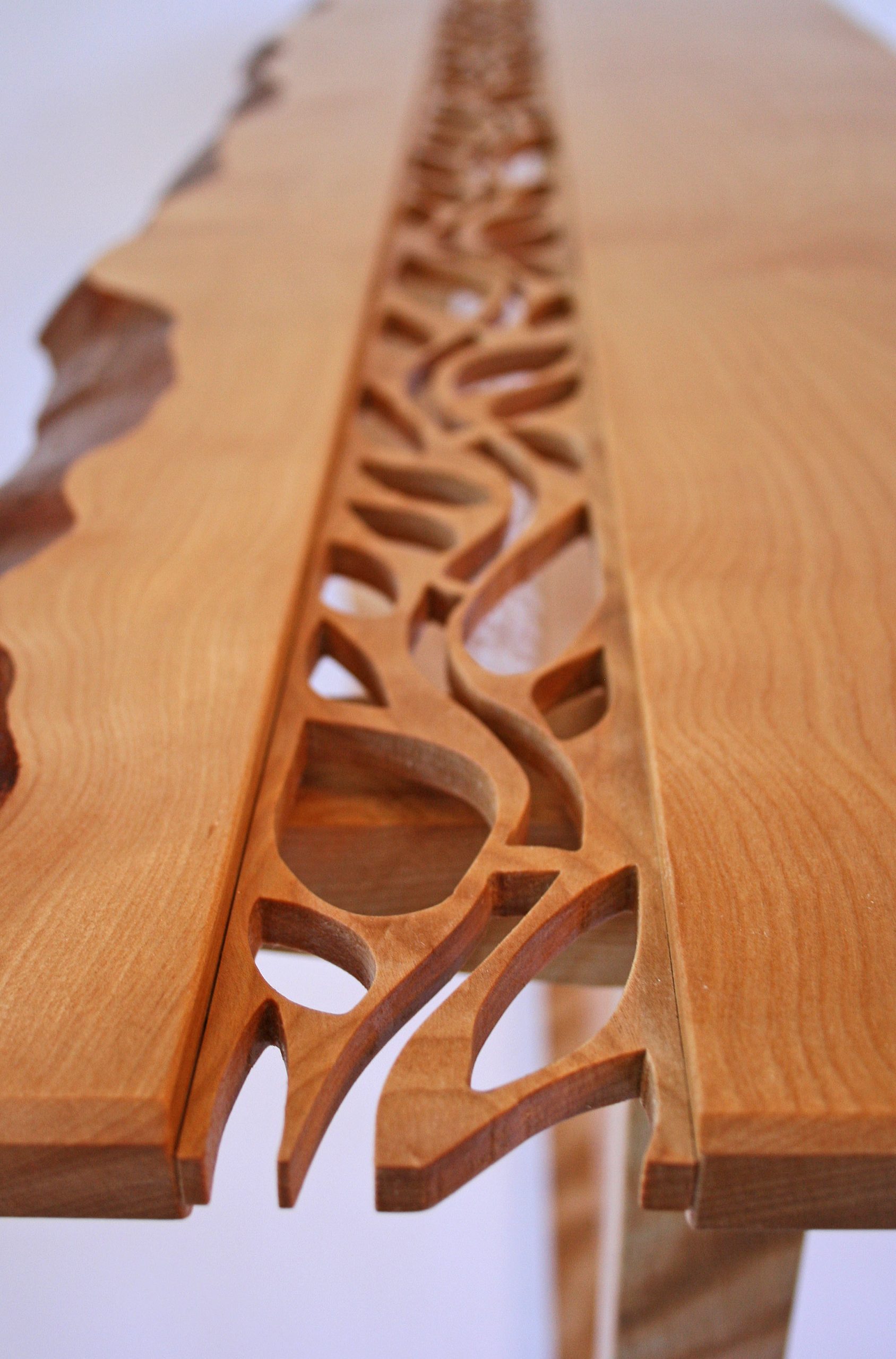
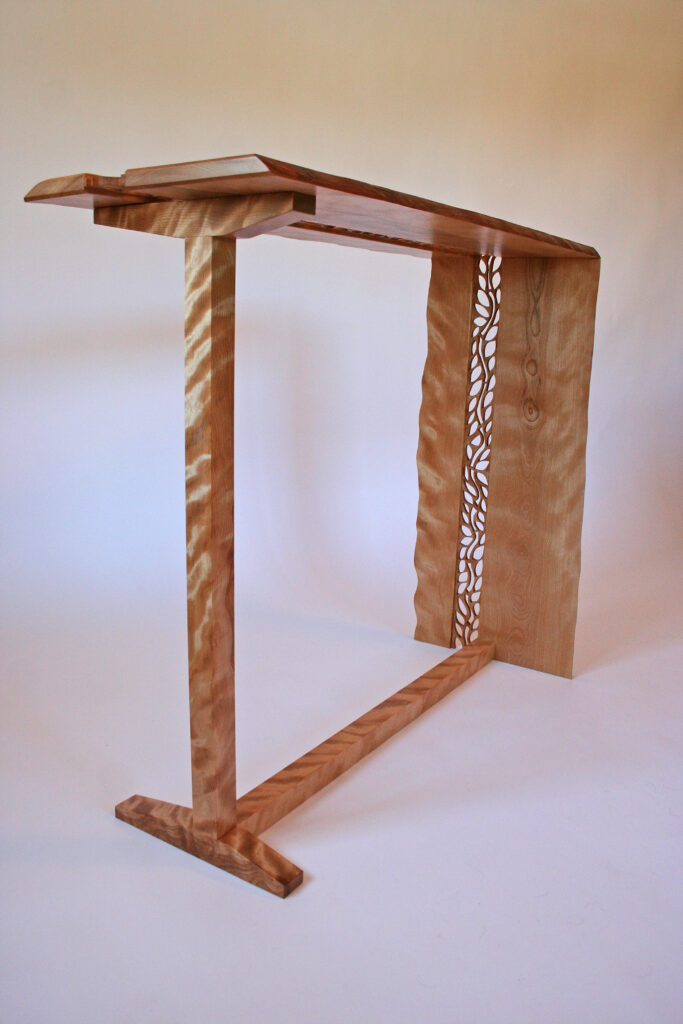
Question #16
Tobias: Which part of working with wood do you dislike the most?
Christina: The one thing that really gets me is when I have a beautifully figured piece of wood and when it goes through a machine, tear-out occurs. Right now, I only have straight blades on both my jointer and my thicknesser. Honestly, a helical head on these machines would reduce tear-out significantly. For now, I have to be on top of blade sharpness to avoid as much tear-out as possible.
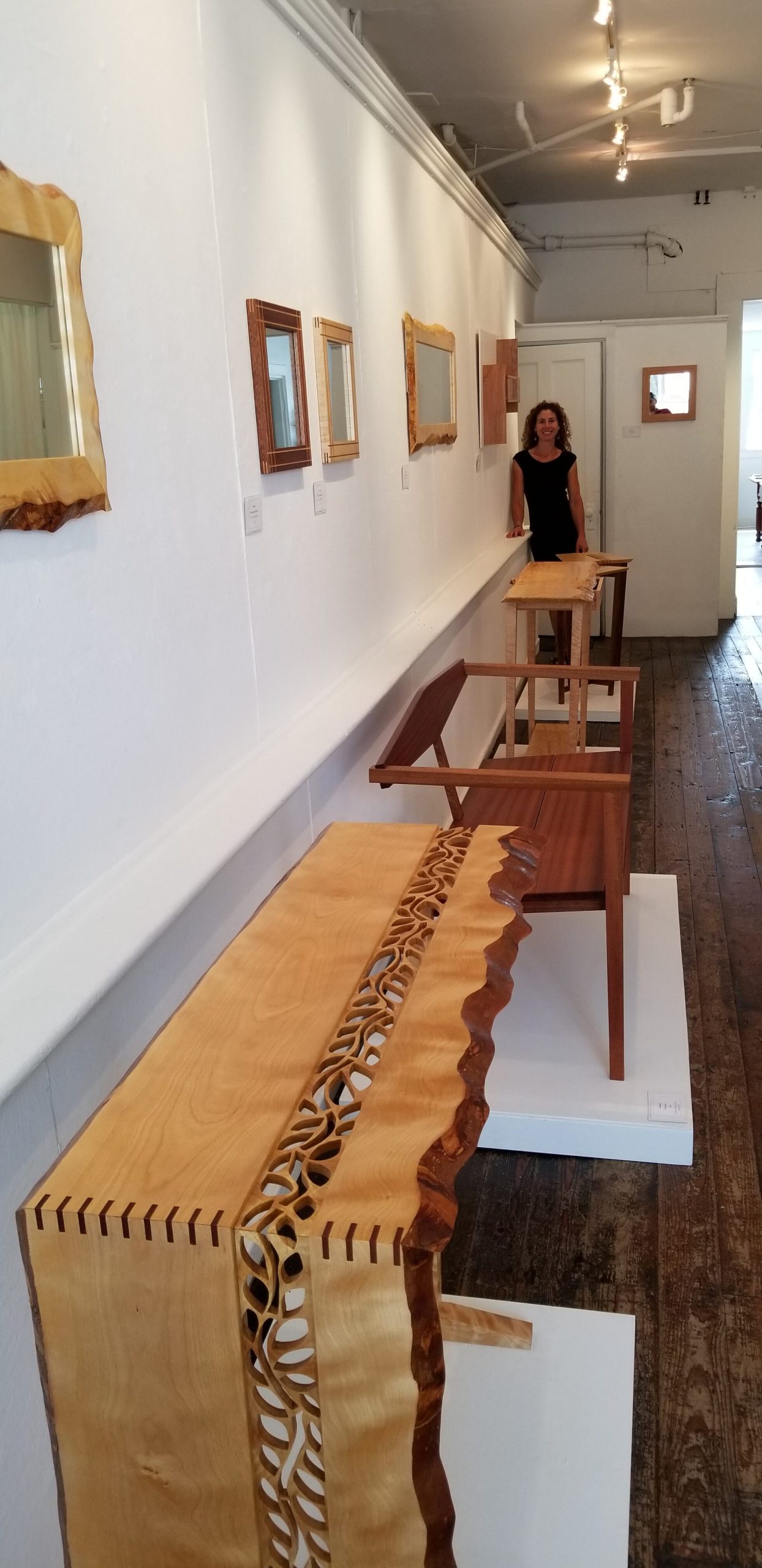
Question #17
Tobias: What is your favorite music to listen to while you work?
Christina: I only listen to music when I am at the final stages of my pieces. All of the other stages require more thought and concentration and it is very easy get into a song and make a wrong measurement or cut.
When I start sanding, glueing and finishing, that is when the music comes on! I enjoy a wide variety of music, so it is easier for me to tell you that I don’t listen to heavy metal, rap, twangy country, the new rap/country or religious music. Give me Bob Dylan, Fleetwood Mac, Janet Jackson or Bob Marley any day of the week!
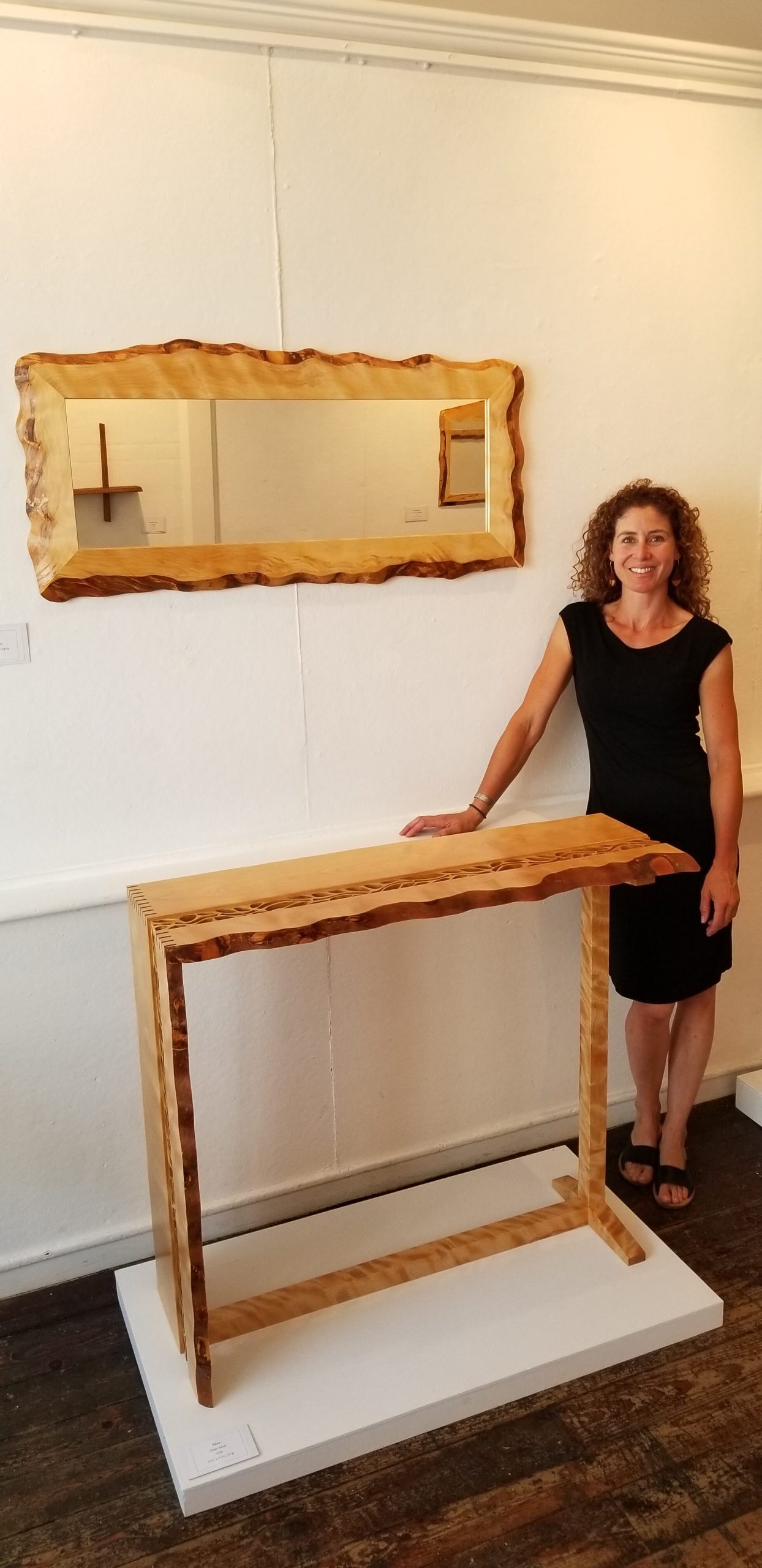
Question #18
Tobias: What is your tool sharpening regime?
Christina: I sharpen my chisels and plane blades with a Japanese water stone and use a Lie-Nielsen Honing guide for this process. I first make complete sure that the whetstone is absolutely flat by rubbing it with a diamond plate. I send my chop saw, table saw and jointer blades to Matthew Tool & Saw in Lewiston, Maine to be sharpened. I order new DeWalt blades for the thicknesser as these are not resharpenable. I also don’t bother resharpening band saw blades.
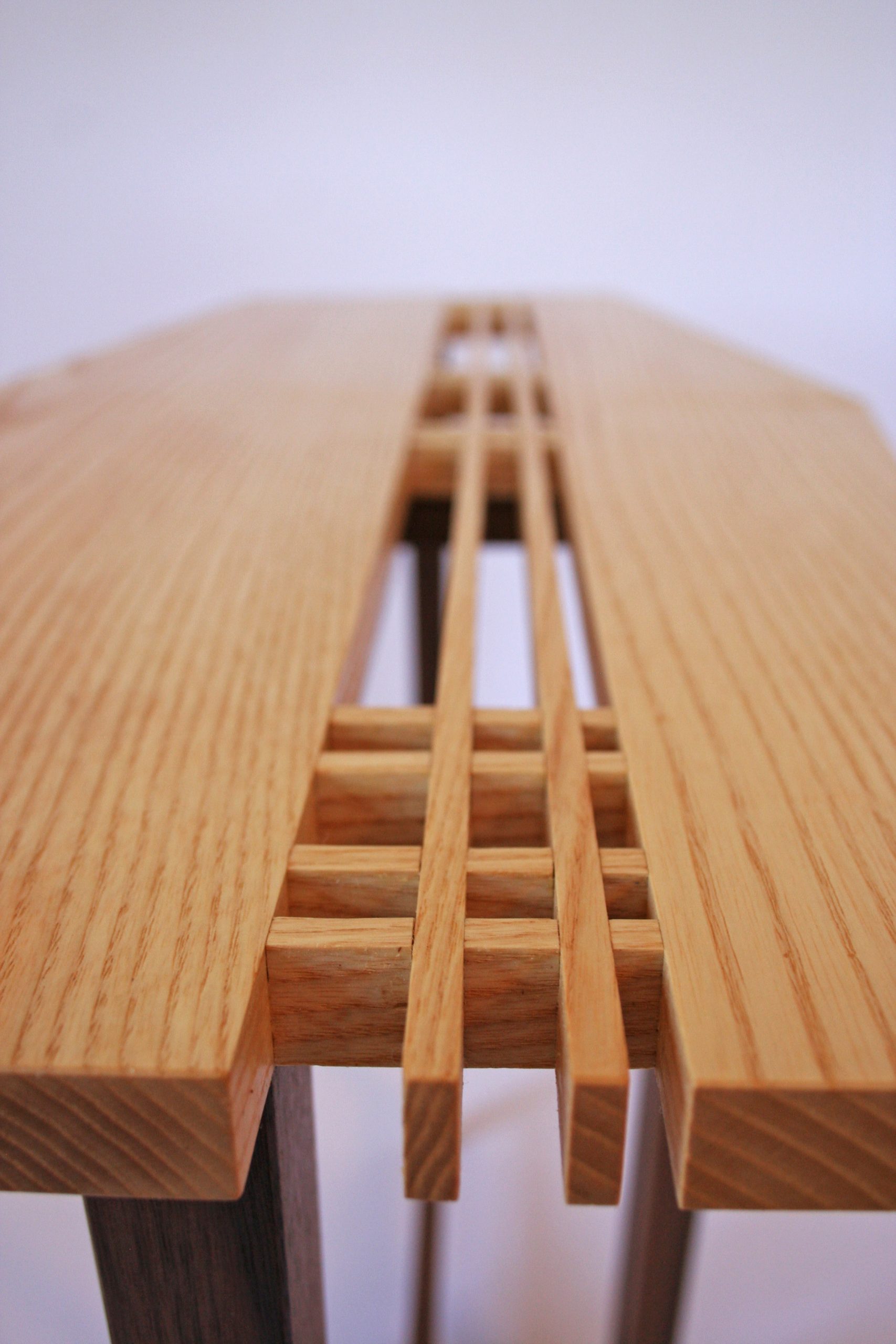
Question #19
Tobias: What custom jigs and tools have you developed for your woodworking?
Christina: As 95% of the items that I make are custom designs and one-of-a-kind pieces, I have not made many jigs. The one set of templates that I have created are for the Blue Heron stools allowing me to easily replicate the laminated curves for them.
I did build my clamping/assembly/glue-up bench at an appropriate height for me to work at. I have also custom built my router table/cabinet. I topped that off with a Bench Dog Pro Lift for my Bosch router. Random note: Prior to purchasing a Rockler tapering jig for my Sawstop table saw, I had built a tapering jig for my old “carpentry” table saw, which can still be pressed into service when required.
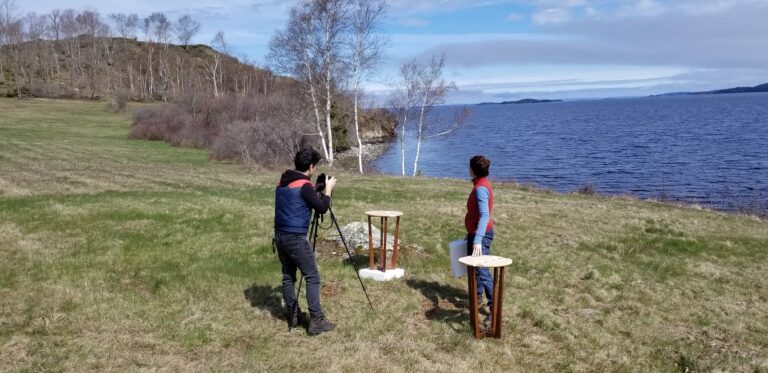
Question #20
Tobias: What is the next piece that you are going to build and why?
Christina: The next piece that I am going to build is a custom order that was recently placed. The clients had seen my Acadia II Bench and loved it, but unfortunately it had already been spoken for. The clients did decide upon a few modifications to fit their allocated space a little better and they also added scrollwork that they had seen on another piece that I had created.
The Acadia II has traditional mortise and tenon construction for exceptional strength and a lifetime of use. The tapered leg and arm details provide aesthetic appeal and a sense of movement and interest. The angle of the seat and backrest provides superior comfort. The bench will be built from solid Sapele.
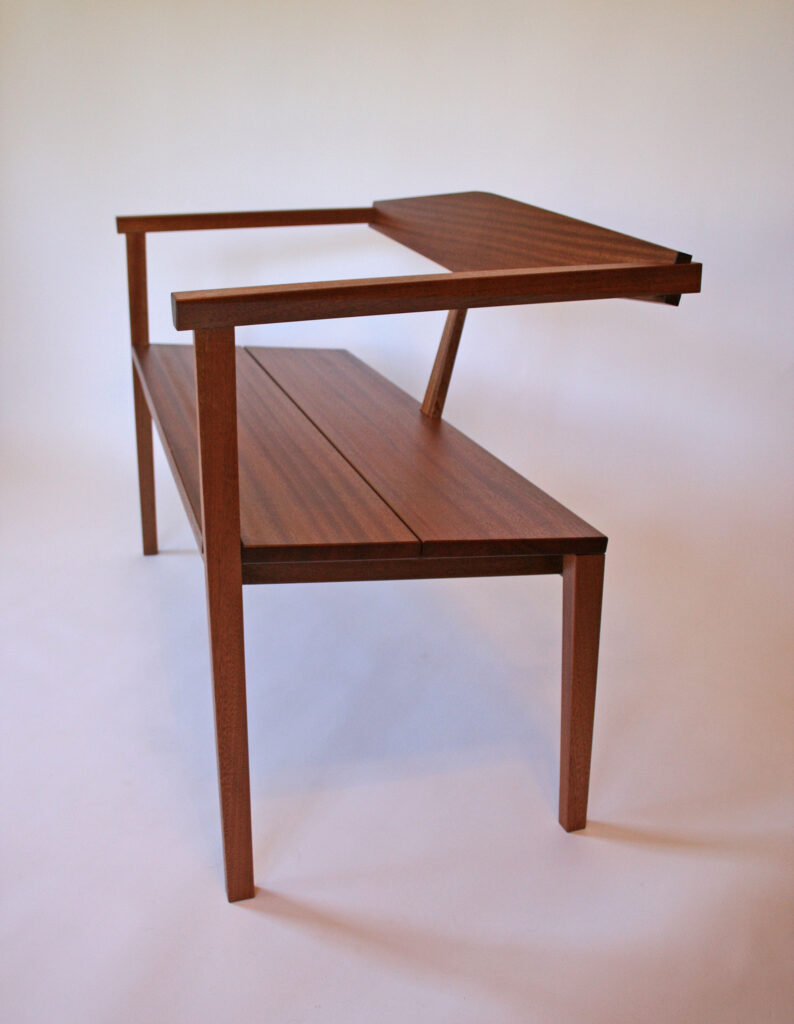
Wish List
Tools, Machines & Accessories:
- Hammer A3 Jointer / Planer.
- New Chop Saw – Not yet researched.
- Plenty more clamps of all varieties.
- Oneida Dust Collector and all the components for a fully fitted dust collection system.
- A real workshop!
Timber:
- Live edge Walnut
- Figured Walnut
- Highly figured Maple
Makers with whom I would love to spend quality time
- Mark Juliani at The Centre for Furniture Craftsmanship
- Adam Rogers at Thomas Moser – Handmade American Furniture
A big thank you and congratulations to Christina for joining us and being our first craftswoman on the Rare Woods Woodworker Sessions USA!
You can contact her at www.christinamvincent.com. Please also follow this wonderful young maker on Instagram @christinamvincent.