Welcome to the Rare Woods USA Woodworker Sessions interview series. Here, we hope to discover more about what makes our woodworkers tick, how you became involved in the craft, how and why you build your pieces and maybe learn a few secret techniques and tips along the way!
Our interviewer, a woodworker since the age of 8, Tobias Lochner is no stranger to the workshop. Find out more about him here.
Our sincere thanks go to Chuck Thornton from C.P Thornton Guitars in Sumner, Maine for sharing his passion and talent with us in the 5th issue of the Woodworker Sessions USA.
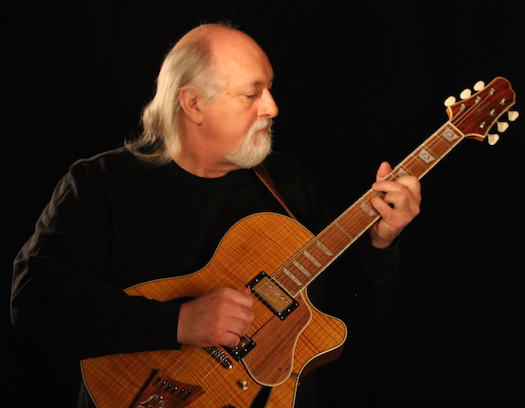
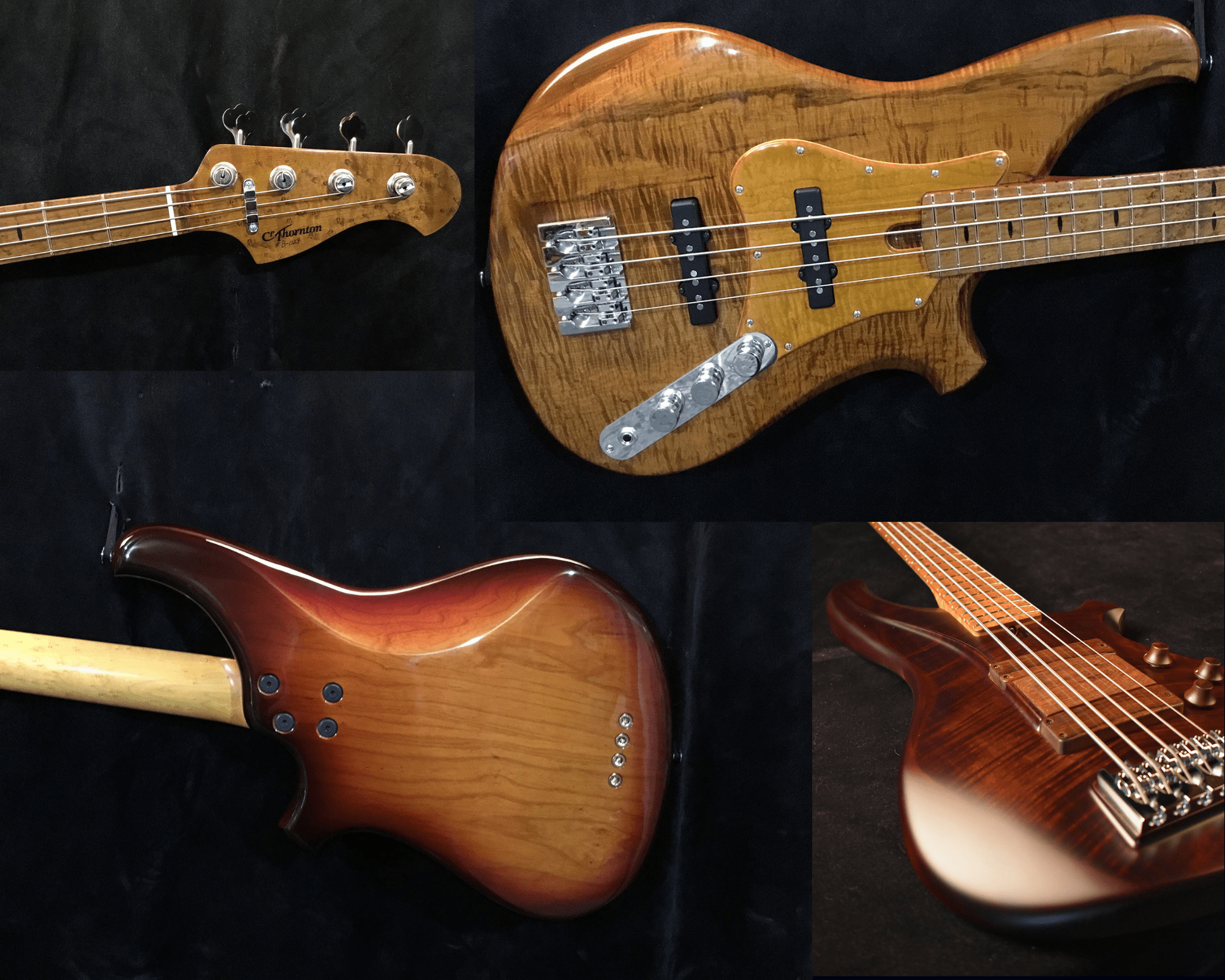
Tobias: Please tell us about yourself, your career and your family.
Chuck: I am Chuck Thornton of CP Thornton Guitars and I have been designing and building electric guitars and basses since 1985. I was born in 1956 and grew up on a farm in Maine. My dad was an extremely hard working man and taught me the importance of good work ethics.
My mom taught me the basics of playing the guitar when I was still quite young, but seeing the Beatles on the Ed Sullivan Show put me over the edge and that’s when I really knew that I wanted to learn how to play the thing properly!
So here I am, 57 years later and I still haven’t really learned how to play, but it it sure has been plenty of fun trying!
In the fall of 1980 and the winter of ’81, I attended Berklee College of Music. In 1983 and 1984, I built a home for my young family and my son still lives in this house.
In October of ’84, I woke up one morning and realized that I was more of a bass player than a guitarist, but I didn’t own a bass… This is how I became a luthier!’
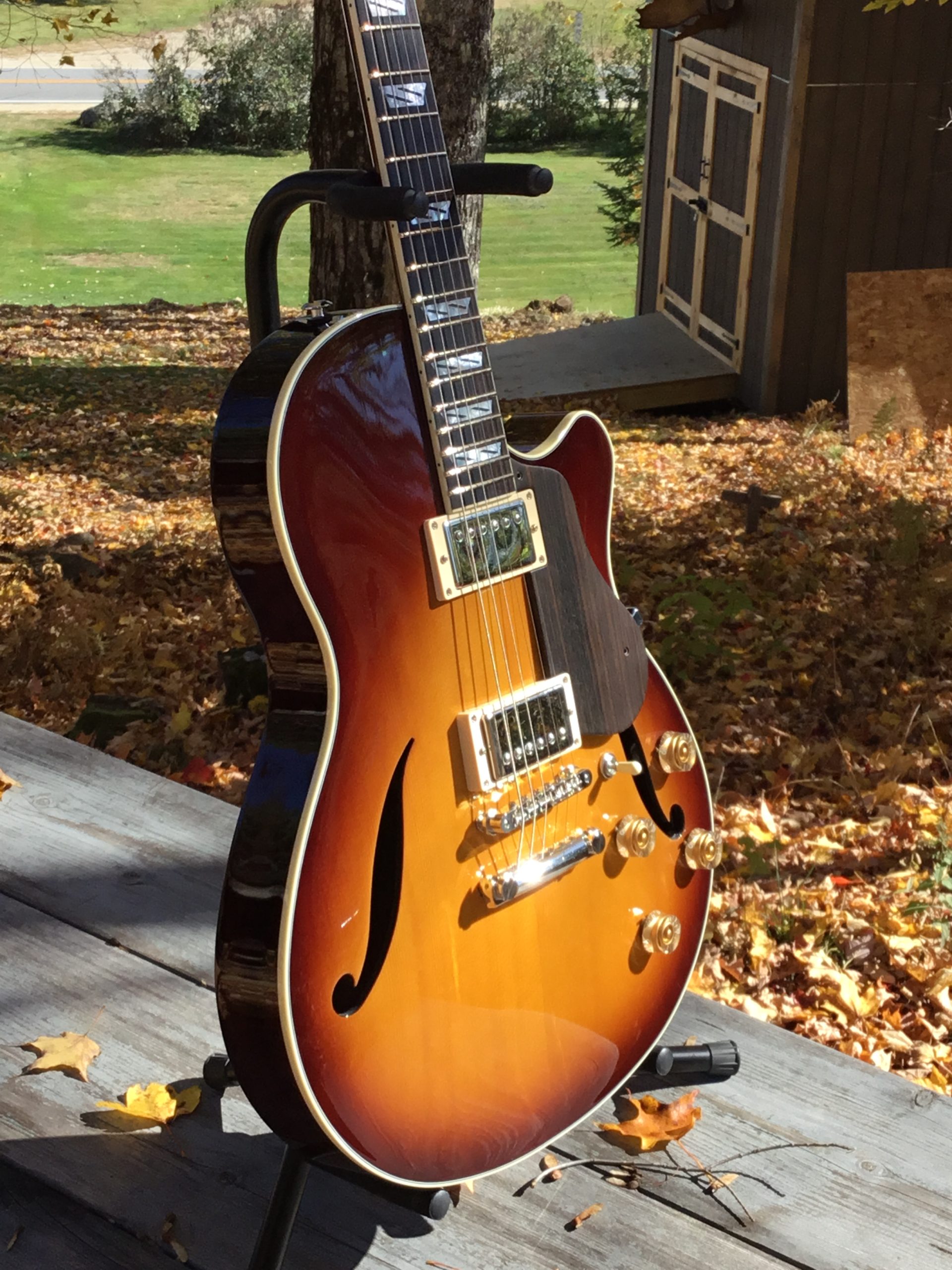
Question #2
Tobias: How did you get started doing woodwork and how long have you been a woodworker?
Chuck: I think that I was about eight years old, when my dad bought me a sabre saw for Christmas and taught me how to make wooden swords and guns, which I would take to school for my friends and I to play with.
From the eighth grade through to my senior year, I took woodworking shop class at school, I never did make a guitar at school, however I did make a percussion cap pistol!
When I was fourteen, I helped the family build our largest barn which was 240 feet long by 40 feet wide and was three stories tall. At that age, I was was employed mostly as the “hold this guy” or the “run and get that guy”, but I distinctly remember hammering countless nails, ten hours a day, seven days a week for my entire summer vacation and I earned $500 for the whole vacation.
After high school my focus was mainly music, which led me to live in different areas of the US, until I moved back to Maine in ’83.
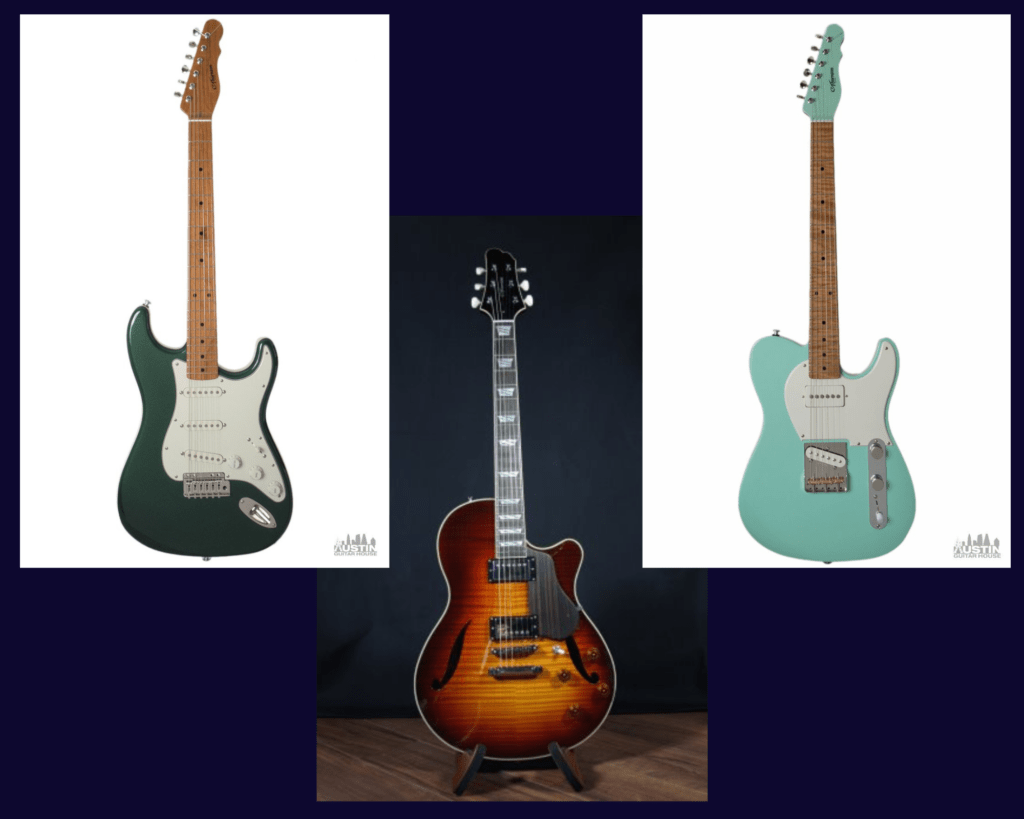
Question #3
Tobias: What was the first item you made and which is your favorite piece?
Chuck: As mentioned above, the first pieces that I made were toy guns and swords, but the percussion cap pistol that I built in school still hangs on my wall. In 85, when I built my first bass, I began the woodworking path which I am still on today. From 1985 to ’87, I built eight basses with bolt on necks. I purchased the neck and built the bodies. It was in 1987, that I started building the entire instruments myself. Between 1987 and 1992, I built fifty-five of these basses.
In ’93, I went to work for Dana Bourgeois, building his acoustic guitars, although my main job was not so much the woodworking aspect, but rather the fretwork and setup of the completed instruments.
In 1996, I went to work for Jon Cooper who is a master violin maker, building both violins and cellos.This was completely different for me as when I was with Dana, I was working at the end of the process, whereas with Jon Cooper, I was working at the beginning of the process, prepping wood, bending sides, making end blocks and side blocks, pre-carving the outside and inside of the violins’ tops and backs, doing the initial carve on the scrolls and pre-carving the necks. Jon would then take my work and finish carve everything the way that he wanted. He also had me build a violin for myself from start to finish, which was a truly amazing journey in itself and was extremely generous of him.
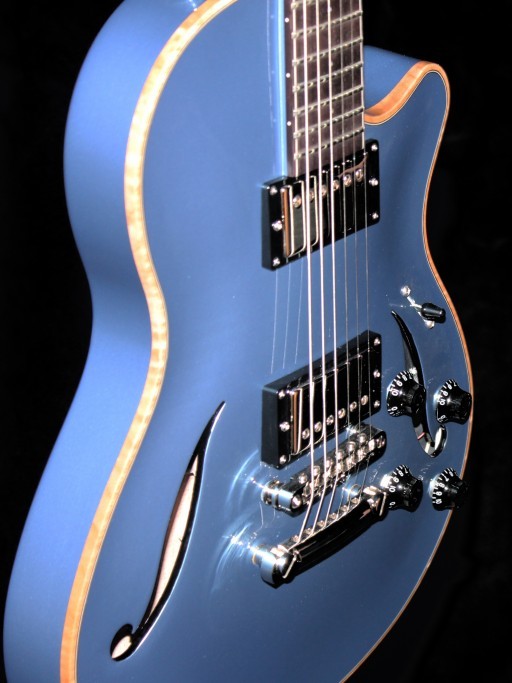
Question #4
Tobias: Which styles of furniture do you enjoy the most:
Chuck: I have never built furniture, but I truly have great respect for those who do. I have been collecting antique furniture for the past 12 years and the workmanship in some of these pieces never ceases to amaze me! I have an Eastlake buffet from around 1895 that is absolutely beautiful.
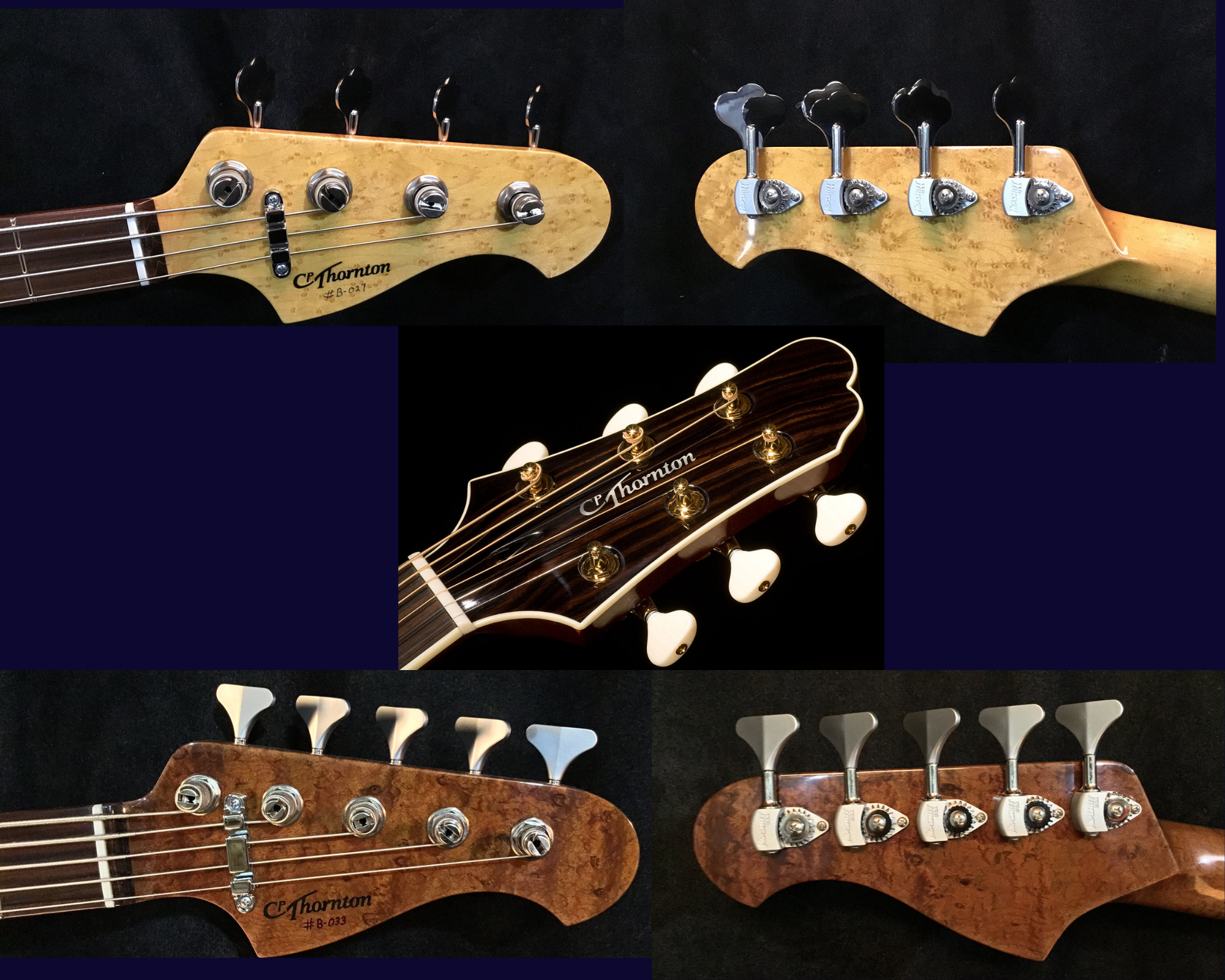
Question #5
Tobias: Which are you favorite local and favorite exotic timbers to work with?
Chuck: The woods that I use for building guitars have as much to do with the tone of the instrument, as they have to do with visual appeal.
For native woods, I use Curly Red Maple, Curly and Birdseye Rock Maple, Big Leaf Maple from our West Coast, Claro Walnut from California, Swamp Ash from Louisiana, Nootka Cedar from Alaska, Alder from our Northwest Coast and Sitka Spruce from Alaska.
I make extensive use of exotic species including Brazilian Rosewood, Indian Rosewood, Macassar Ebony, Indian Ebony, Honduran Mahogany and African Mahogany.
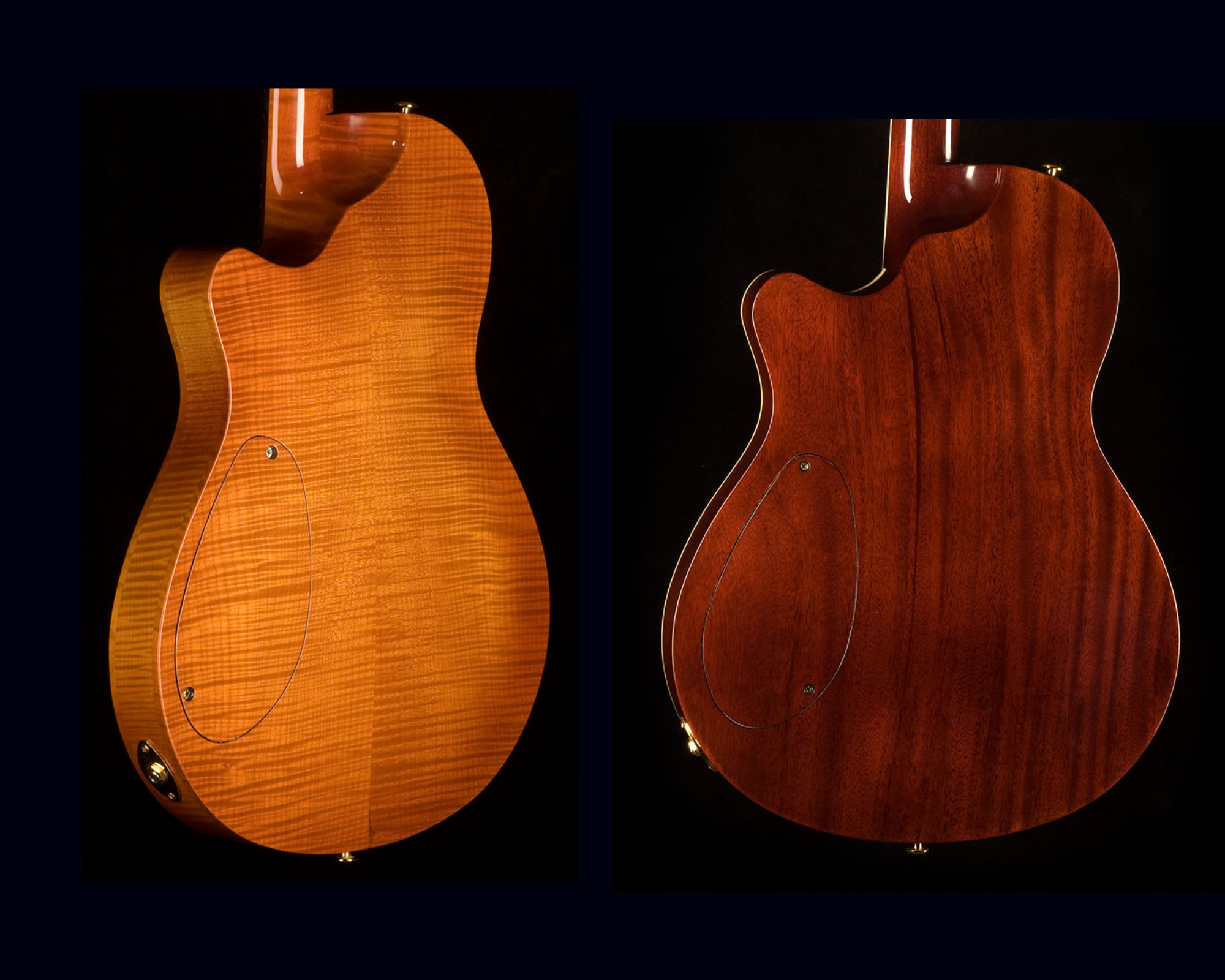
Question #6
Tobias: Please list your most used hand tools and tell us why they are your “go to” tools.
Chuck: The parts for my guitars and basses that I design are carved out on a CNC machine, so my hand tool requirements are limited to hand sanders, a couple of really sharp bench chisels and a knife for creating a 90º angle between where the neck of my semi-hollowbodies meets the body of the instrument. Hand drills. powered screw guns with clutches & a 3″ pneumatic orbital buffer for final finish polishing.
I utilize lots of different sizes and shapes of sanding blocks, scrapers, a soldering iron for the electronics as well as a variety of nut files, straight edges, reamers, calipers and a Dremel tool.
Question #7
Tobias: Can you list your favorite power tools & machines and tell us why?
Chuck: I have a room in my shop where I prep my woods to go to the CNC. The tools and machine in this room are as follows: Large re-saw bandsaw, 16″ jointer, 6″ jointer, 16″ planer, 32″ belt sander, drill press, router table and various routers. I also have a variety of marking and layout tools in this room as well.
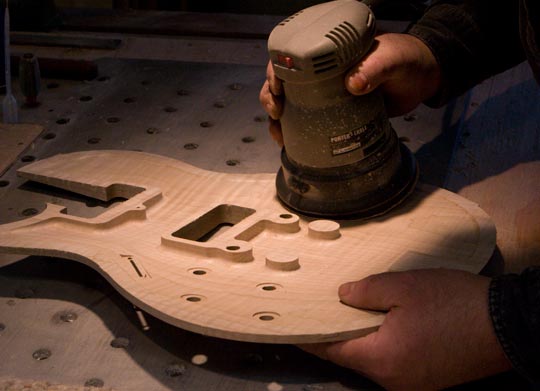
Question #8
Tobias: What is it about working with wood that you find most enjoyable?
Chuck: The fact that wood is like snow flakes, there are no two pieces exactly the same. I really love jointing and planing off the top surface of a piece of wood and revealing it’s natural beauty.
I adore the smell of Brazilian Rosewood, but not the smell of Nootka Cedar. For me, applying the first coat of finish and witnessing the figure in the wood come to life is always a true pleasure. Also, watching a vibrancy of a sunburst hand rubbed finish beginning to show the different colors and depth. I love hearing a guitar for the first time, and then again in a few years after it has opened up and come into its own.
I think if it as “The wood woke up and realized it wasn’t a tree anymore, but a beautiful musical instrument”!
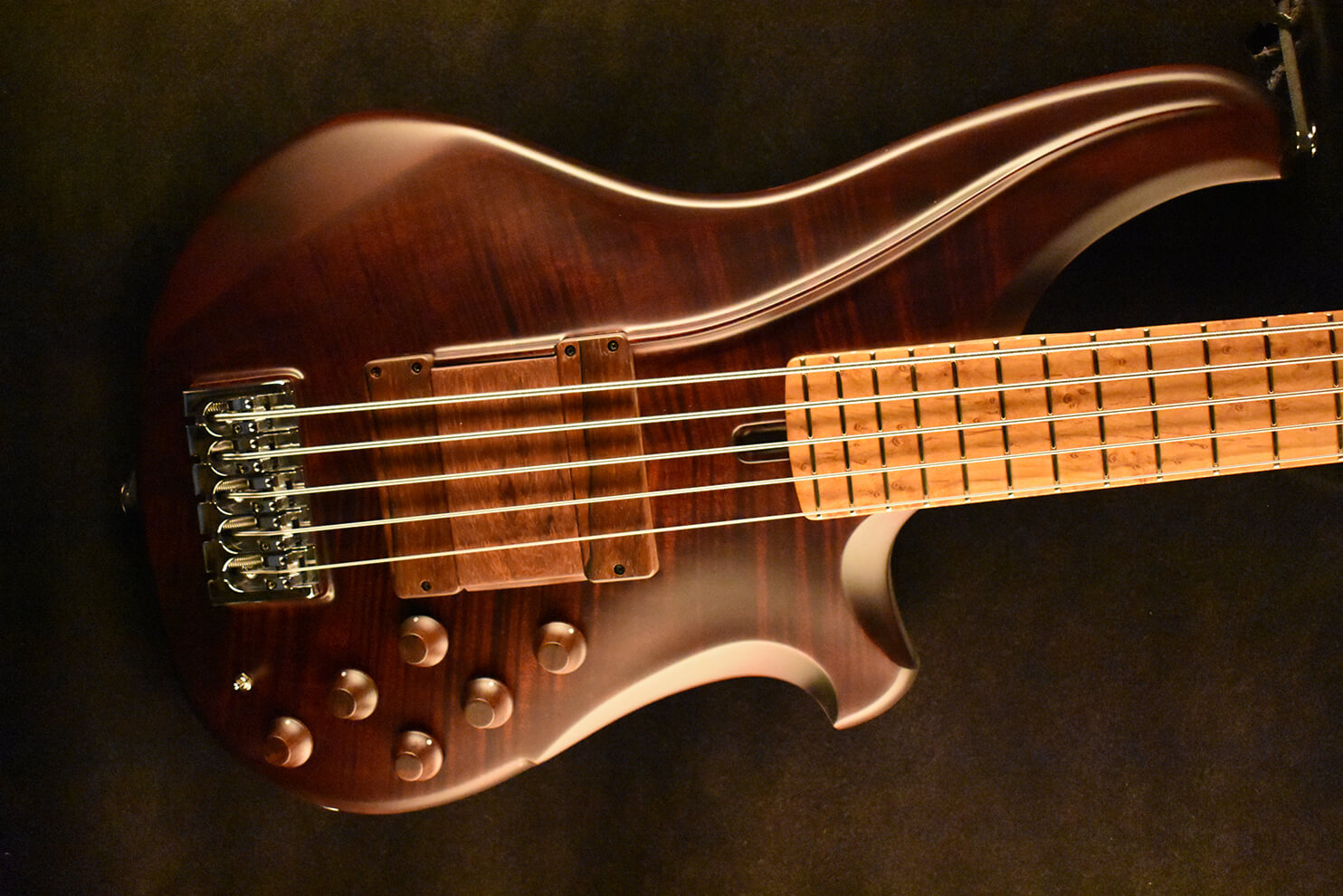
Question #9
Tobias: What type of workshop do you have?
Chuck: My workshop is attached to my house and covers about 2300 square feet. The wood comes in through an overhead door and is stored on metal shelves and under a 12 foot workbench until it is fully acclimated to the shop.
The wood is then processed in one room where I have the 16″ jointer, 6″ jointer, 16″ planer, resaw, bandsaw, drum sander, router table and dust collection system. After this, the wood then goes to be carved on CNC machinery that I sub-contract. When my parts come back, they are laid out on a different 12′ bench, so as to be matched with the other parts the guitar or bass. If I am building a semi-hollowbody instrument, it is at this stage that I would glue all the individual parts together. I have another room where I do my final finish carving, sanding and fret jobs.
Once the final sanding and inspection is done, the guitars go into the dry room to be hung, ready for finishing. This room is a multi-purpose area with a floor space of 20′ x 20′. I also use this room as my music room, where I have guitar and bass amplifiers allowing me to test my instruments. Included in this room are my stereo system and a 16 channel recording area.
There is a dedicated finishing room fitted with a Binks paint booth, a steel cabinet for storing paints, a bench for taping and a small bench for mixing colors. All the paint guns hang on the wall at the mixing bench.
When the instruments are finished and dry, I take them one by one into a separate room where I do the finish sanding, buffing and polishing. In this room I have a bench dedicated to finish sanding, a cabinet for finishing sandpapers which includes 15 micron, 1500 grit & 3000 grit wet & dry papers. This room also has a 1-1/4″ arbor buffer and a 3″ orbital buffer.
After final buffing, the guitars continue to hang in the dry room until they they get set up, which happens in the next room where I keep all the mechanical and electronic guitar parts for the final assembly and setup process. This room contains four benches, one where I solder the electronics, a second one for fitting parts to the guitars, an all-purpose bench and finally the bench where I set the guitars up and make them play.
When I brought the electrician in to wire up my lighting, he said that I must make sure that my benches are exactly where I want them so we don’t have to move lights and cabling around after the initial installation. This got me thinking that the benches should each include their own lighting, so I created a way to have my lights attached to the benches so that I can rotate and set them exactly where I need the illumination.
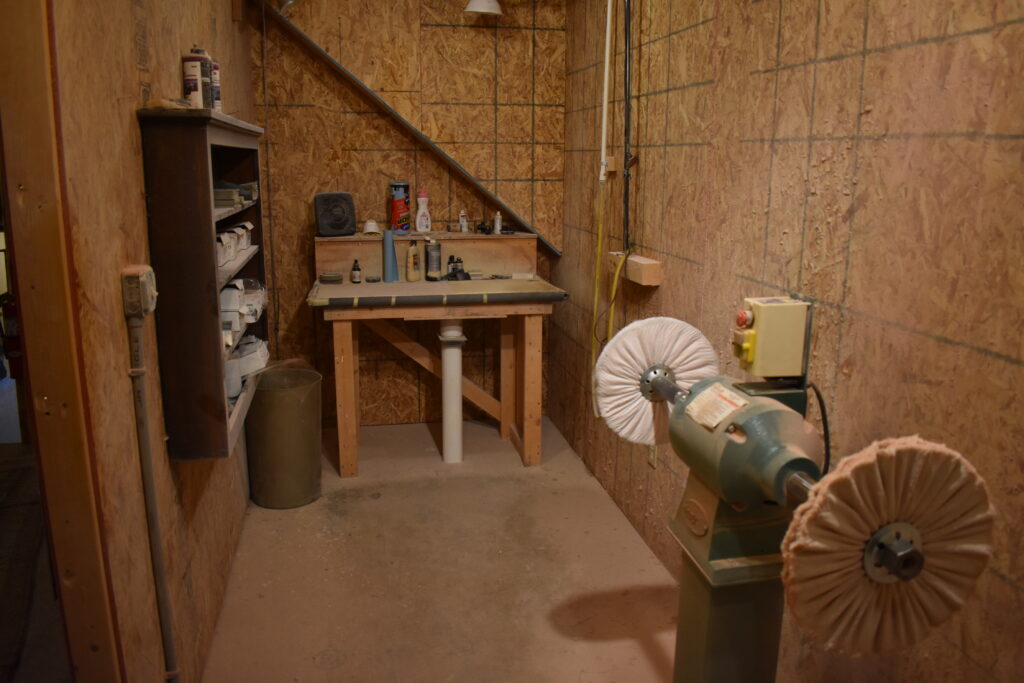
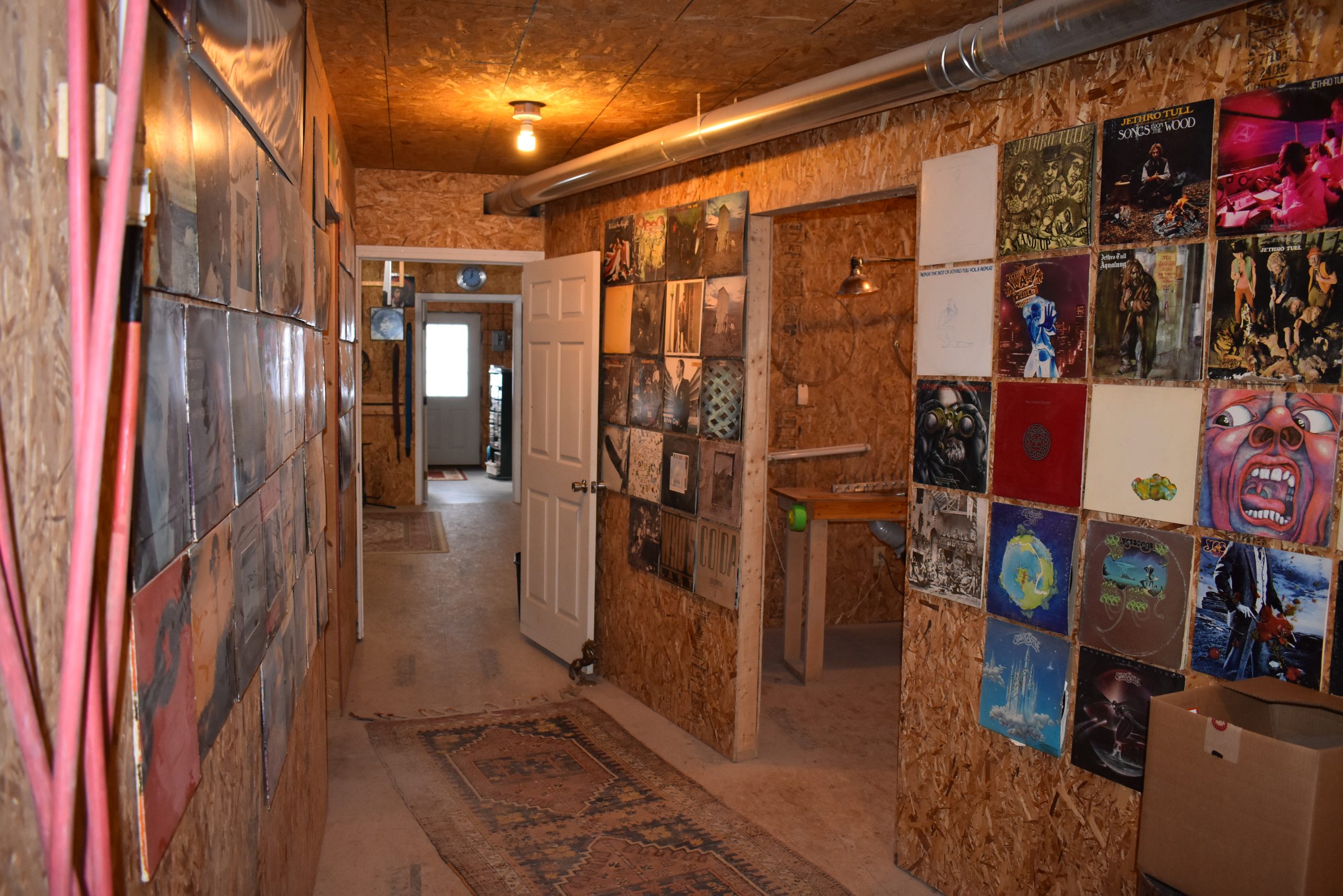
Question #10
Tobias: What is your clamp line-up and why?
Chuck: I have Pony clamps in my processing area for gluing book-matched pieces together for tops, as well as for gluing slip matched pieces together for solid body guitars and basses. I also own about fifty Irwin Quick-Grip clamps for gluing tops and backs onto sides for my semi-hollowbody instruments and a number of custom self-built clamps for gluing fingerboards to their necks.
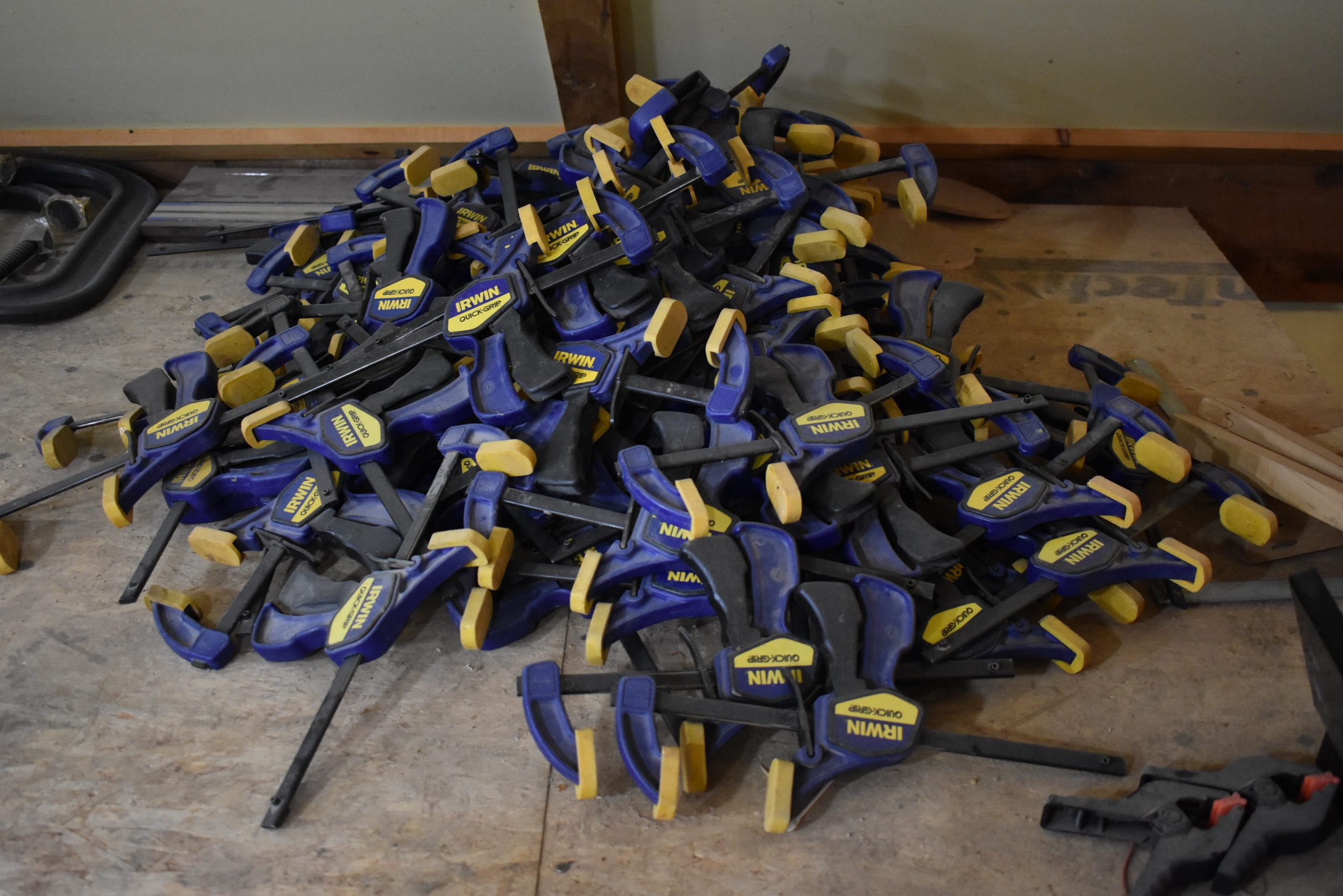
Question #11
Tobias: Which glues and adhesives do you use and why?
Chuck: This is a short list. I use fish glue because it dries fast and exhibits almost no creep. I also use 1/16″, 1/8″, 1/4″, 1″ and 2″ masking tape for masking fretboards during the fret work and for taping up when doing more than one color on a guitar body and headstock.
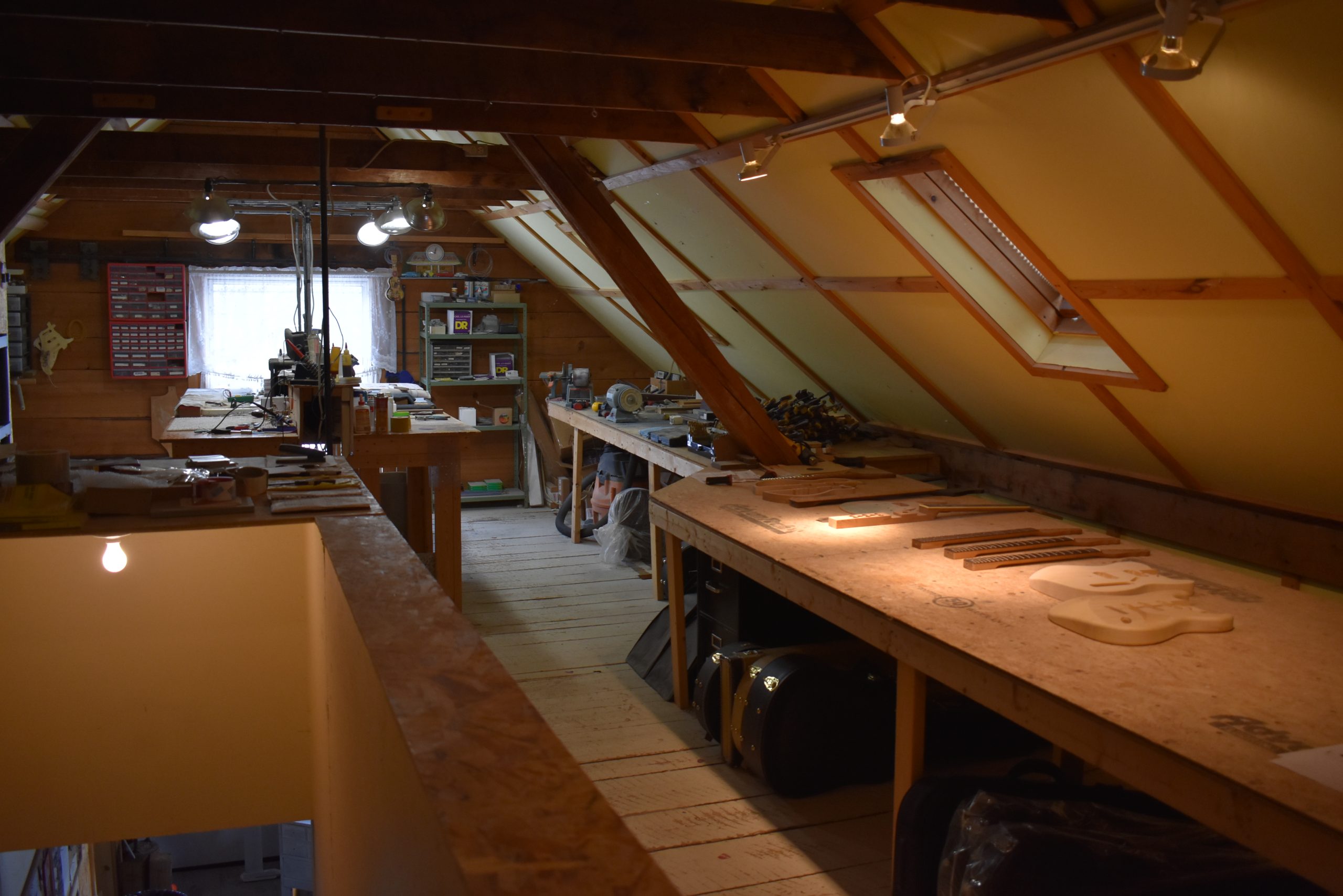
Question #12
Tobias: Which woods (exotic & local) have you not yet used and why are you interested in building with them?
Chuck: For guitars, I think that I have used most of the woods that work well for the instruments, however I have just sourced some Marblewood and Bocote that I can’t wait to use in building bass guitars for their beauty as a top wood and fingerboard wood. Their average weights and hardness are comparable to other woods that I have used for these instruments.
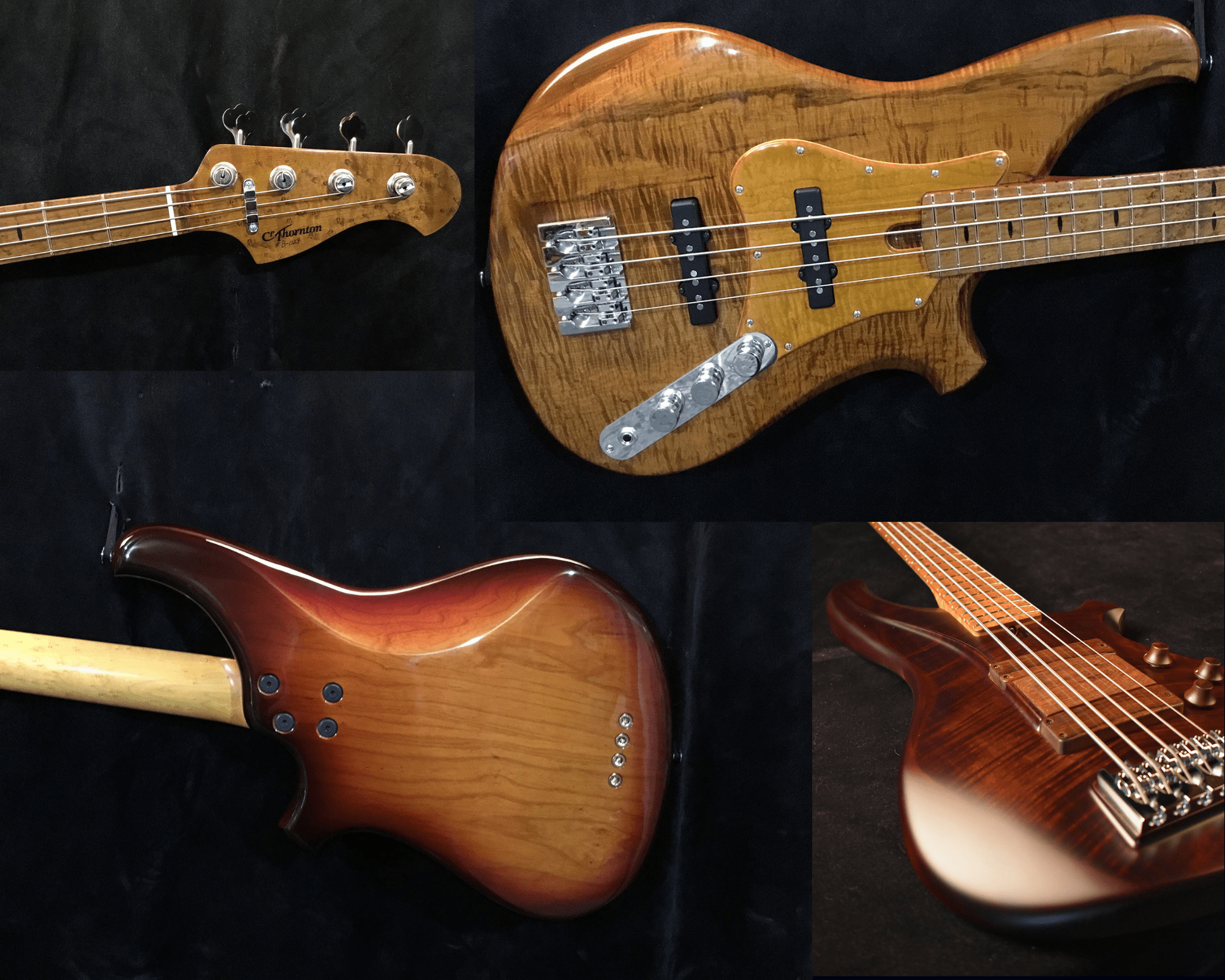
Question #13
Tobias: What and whom are your sources of inspiration for your woodwork?
Chuck: As for people who inspire me, my father, Dana Bourgeois, Jon Cooper and a guy named John Slobod who came to work with us at Bourgeois Guitars in 1994. When I saw his first guitar, I thought that this chap had a lot to learn and man, learn he did! His woodworking ability now is second to none.
My real inspiration is derived from musical instruments themselves. Not only do they need to look right, but they also need to sound right and play right.
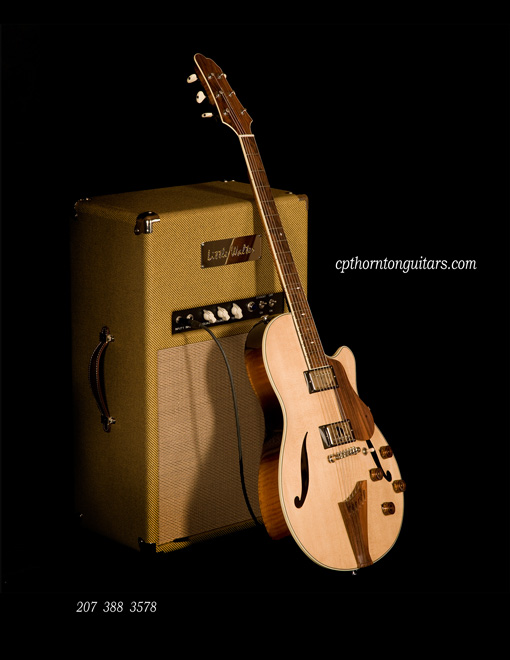
Question #14
Tobias: How do you design your pieces? Do you use CAD of SketchUp? Do you sketch out by hand?
Chuck: When I first create a design concept, I draw it out in full scale and once I have the overall look of what I am after, I hire a programmer to program my design into Master Cam and create the required tool paths for the CNC.
Question #15
Tobias: What are your finishing regimes, what products do you use and which are your favorite processes?
Chuck: How I finish and what I finish with depends entirely on the instrument that I am building. On my solid body models with the torrefied Rock Maple necks, the necks get a hand rubbed oil/varnish finish which is very thinly applied. The bodies of these models get two-tone 1950’s American car colors. A lot of my semi-hollowbody guitars receive a sunburst finish using aniline dyes suspended in nitrocellulose lacquer.
Most of my bass guitars receive a matte acrylic urethane finish.
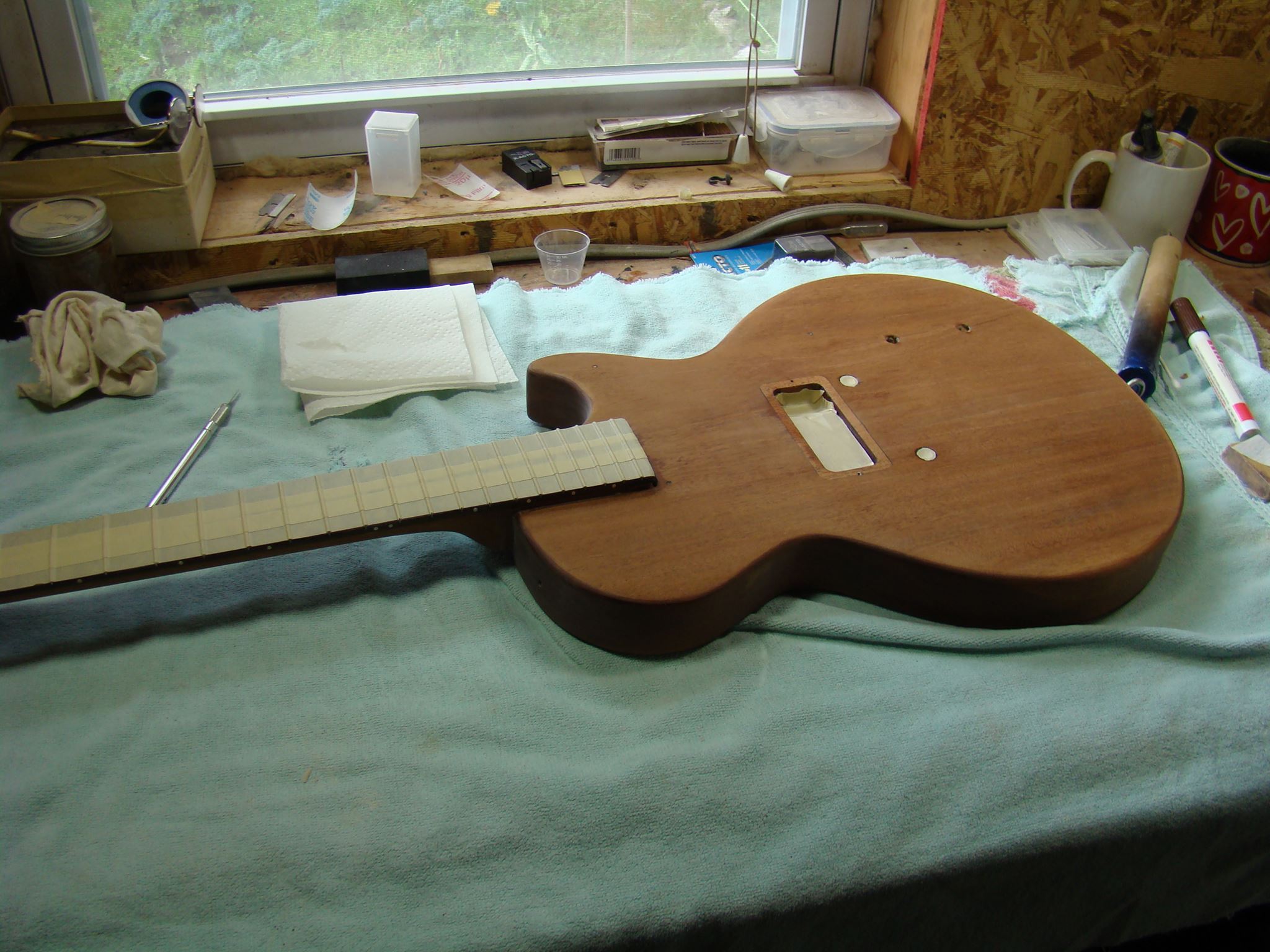
Question #16
Tobias: Which part of working with wood do you dislike the most?
Chuck: The Dust!
Question #17
Tobias: What is your favorite music to listen to in your workshop?
Chuck: It depends largely on my listening mood on a particular day. Sometimes, I’ll listen to older Jazz-Fusion all day, the next day might be Country and then 60’s & 70’s Rock & Roll. I think that I am the same as most people, as I like to listen to music that I grew up with.
One of my favorite bands since the early 70’s is Steely Dan. One day the phone rang and it was Walter Becker of Steely Dan. He invited me to a concert in Boston and asked me to bring any guitars with that I would like to show him. At the time, I only had one for sale, so I took it with and showed Walter and he bought it on the spot! Over the course of the next couple of years, he bought ten guitars from me.
Some years later, I had just finished a batch of guitars and posted pictures of them on my website. Within a few days of posting the pictures, Walter called and asked if the Gold Tp Contoured Legend was available for sale, and I told him that it was sold and had already shipped to it’s new owner. He asked if I would call the owner and see if he would sell it to him, which of course he did! Walter sent him Steely Dan concert tickets for him and his wife, played the instrument at the show and called my client to thank him profusely for selling him the guitar.
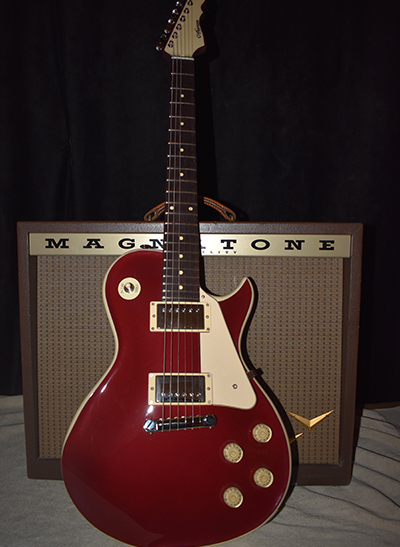
Question #18
Tobias: What is your tool sharpening regime?
Chuck: I don’t have one, I just sharpen as needed.
Question #19
Tobias: What custom jigs and tools have you developed for your woodworking?
Chuck: I have a set of custom clamps for gluing fingerboards to the necks of my guitars. I also have many custom jigs and fixtures designed and built by a couple of CNC programmers and operators that I sub-contract to.
Question #20
Tobias: What is the next piece that you are going to build and why?
Chuck: I am planning on designing a headless bass guitar. I really like the idea of a shorter instrument for players who have to get around in cities.
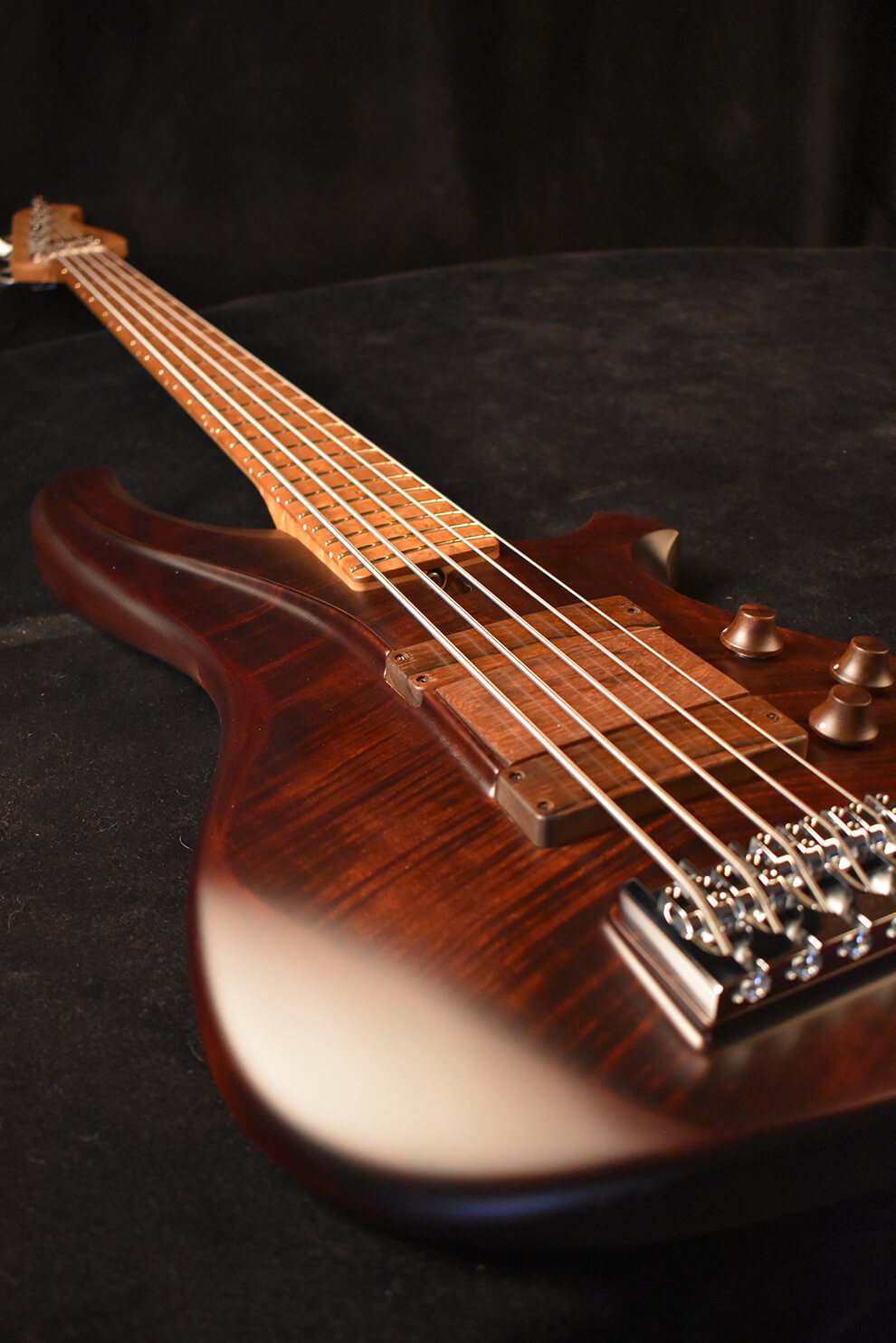
Tool Wishlist
Chuck: I really don’t have much of a wishlist other than my own CNC machine.