Welcome to the Rare Woods USA Woodworker Sessions interview series. Here we hope to discover more about what makes woodworkers tick, how you became involved in the craft, how and why you build your pieces and maybe a few secret techniques and tricks as well!
Our interviewer, a woodworker since he was 8 years old, Tobias Lochner is no stranger to the workshop. Find out more about him here.
We are most grateful to David Knittle of the Knittle Studio for joining us for our 2nd Woodworker Sessions USA! David’s woodcraft niche is unique and his passion shines brightly in every piece that he creates. It is extremely seldom that we come across a woodworker whose specialty lies not in independent furniture items, but rather in those created to support and enhance the display of unique and meditative objects.
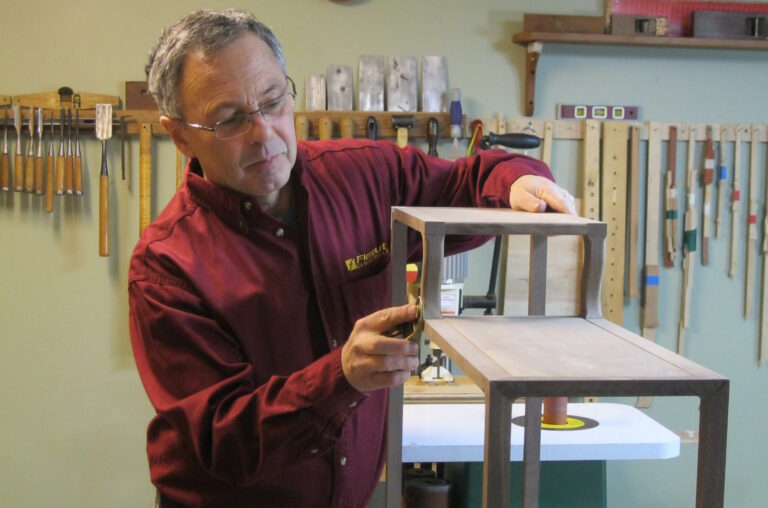
Question #1
Tobias: Welcome to The Woodworker Sessions and thank you for joining us! Please would you tell us a little about yourself?
David: I am a full-time professional woodworker. My wife, Cathy and I live in beautiful Northern Vermont. We have four adult children (three boys and a girl) living throughout the USA. We enjoy hiking, kayaking, camping and fishing, which are a few of the reasons that we settled in Northern Vermont. My hobby is creating and caring for bonsai and I also occasionally teach classes on the subject.
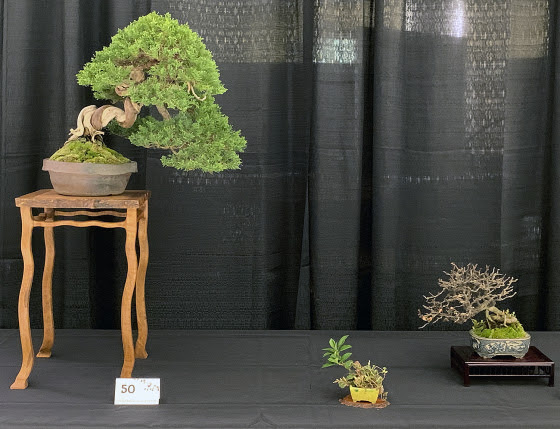
Question #2
Tobias: How did you get started doing woodwork and how long have you been a woodworker?
David: I became interested in woodworking while on a construction project in 1982. A cabinetmaker was hired to build cabinets and doors onsite and I volunteered to assist him. When the job was over, I decided to start building custom furniture.
My early work was influenced by Sam Maloof and I attended a few classes that he taught. I later met George Nakashima and became fascinated with Japanese woodworking. Around the same time, I developed a keen interest in bonsai and oriental art. As my hobby grew, bonsai artists began asking me to build display stands for their bonsai and related art, such as viewing stones and sculptures.
Over the years, building bespoke display stands developed into a large percentage of my work. During that past seven or eight years, it has been all that I have had time to build!
Beginning in 2003, I took a few years off and worked as the operations manager for the Flexcut Carving Tool Company. My good friend, David Bennett founded the company and asked me to help him when it grew too large for him to manage on his own. When David retired and sold the business, I went back to woodworking.
Question #3
Tobias: What was the first item you ever made and which is your favorite piece?
David: The first piece I built was a Cherry end table. My favorite piece is definitely my stand for displaying five small bonsai. The posts and frames are made from Indian Rosewood and the panels are Morado, which is sometimes known as Bolivian Rosewood.
Five Tree Shohin Bonsai Stand. Pseudo Bamboo Indian Rosewood Posts & Frames. Morado Panels.
My client won Best Display Award at the 2018 National Bonsai Show
Question #4
Tobias: Which style of furniture do you enjoy building the most?
David: Without doubt, Japanese style furniture! I have built quite a few Tansu, the storage chests typically used in traditional Japanese homes. Most of my work revolves around interpretations of traditional Japanese designs.
Question #5
Tobias: Which are your favorite local lumber species and which are your favorite exotic lumber species to work with?
David: My favorite local woods are definitely Cherry and curly Hard Maple. I also really enjoy working with Walnut when I can find it properly air-dried. As far as exotics go, Indian Rosewood and Macassar Ebony are my absolute first choice!
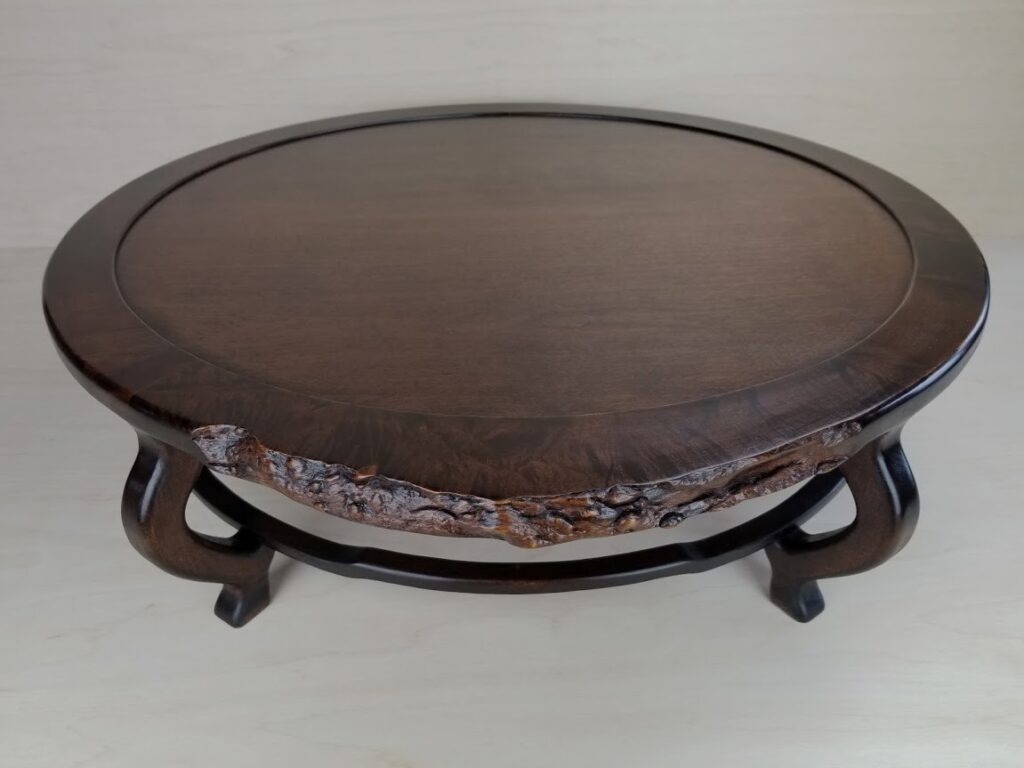
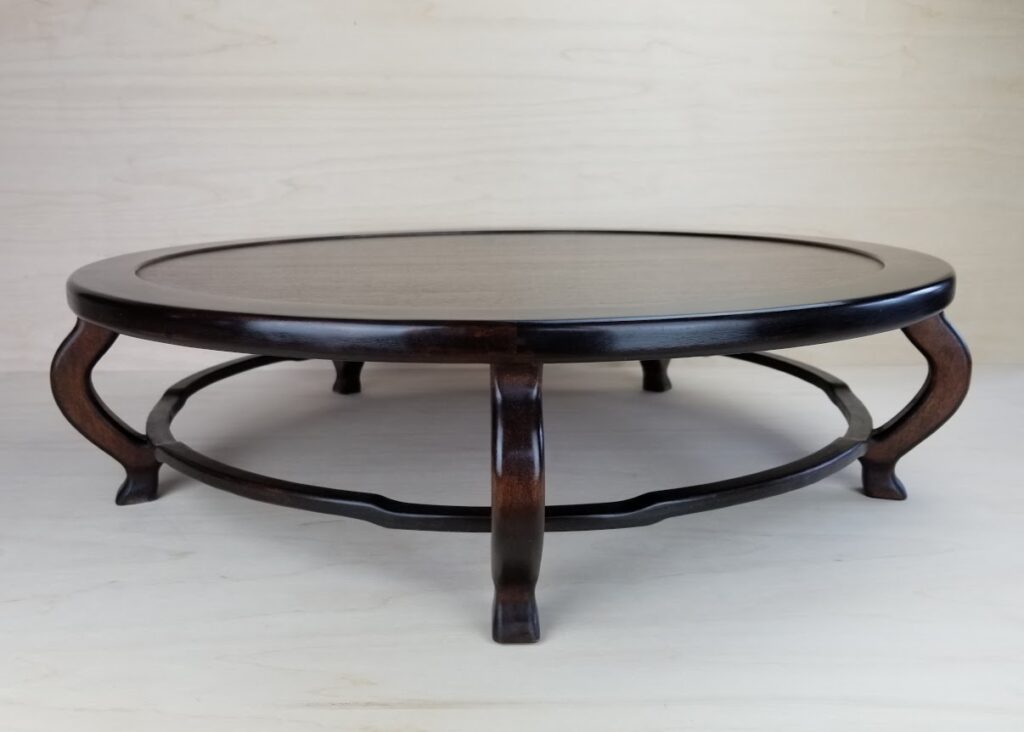
Question #6
Tobias: Please tell us about your most used hand tools and why they are your go-to tools?
David: My all round favorite tool is a Lie-Nielsen Toolworks block plane. It is compact, yet heavy enough for me to wield with ease and extremely fine control. I also have a number of Japanese chisels which I love and I would be lost without my Iwasaki carving files.
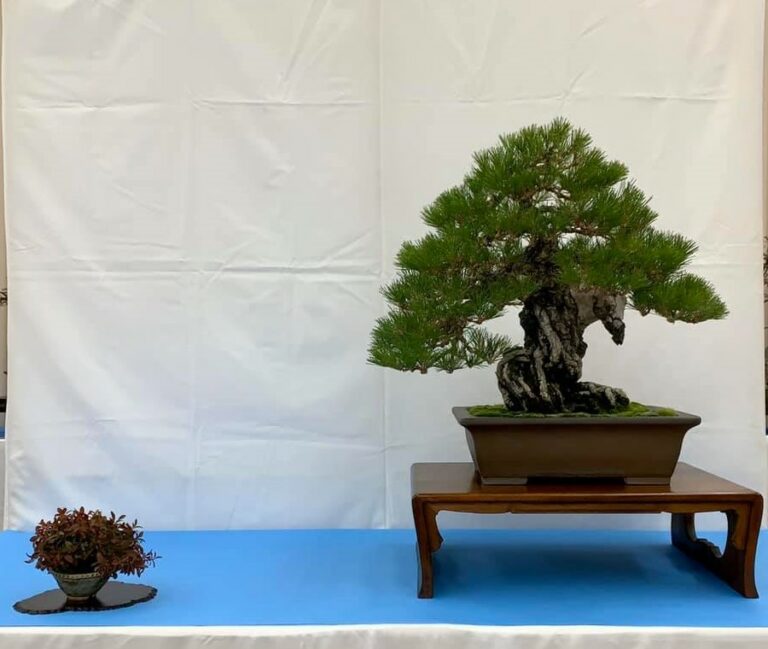
Question #7
Tobias: Can you list your favorite power tools and machines and tell us why?
David: My shop is equipped with all of the basic power tools and machines: band saws, table saw, jointer, planer and drill press. I tend to use the table saw predominantly, due to its versatility.
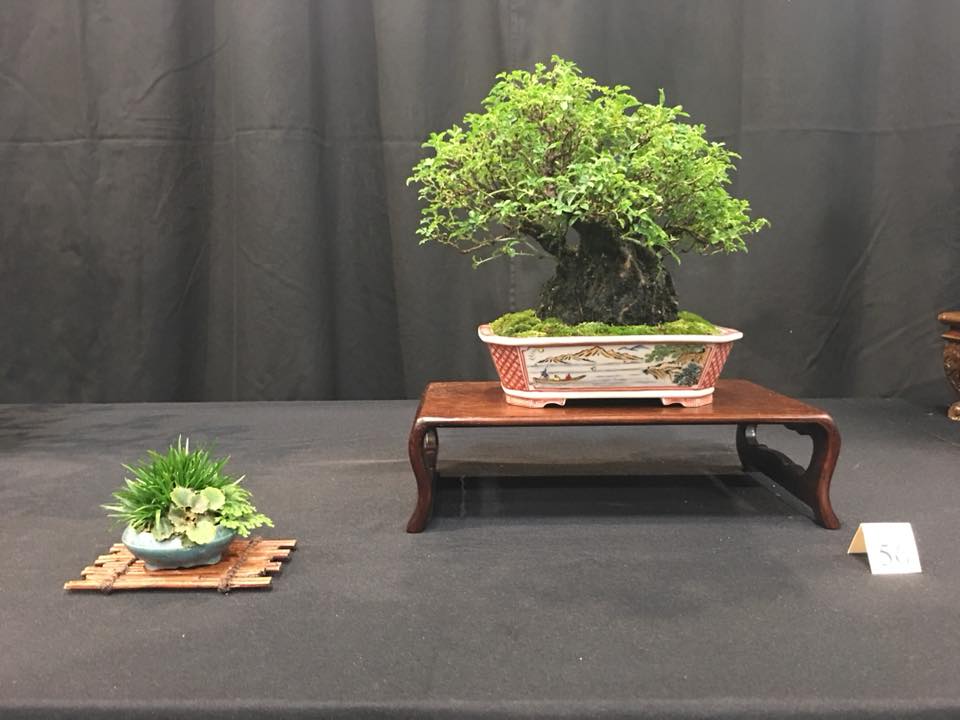
Question #8
Tobias: What is it about working with wood that you find most enjoyable?
David: I love working with wood because it is so variable and versatile. Density. movement, graining and color all play their part. My work is designed to enhance the object being displayed upon it. Choosing the right wood to accomplish that is wonderfully rewarding.
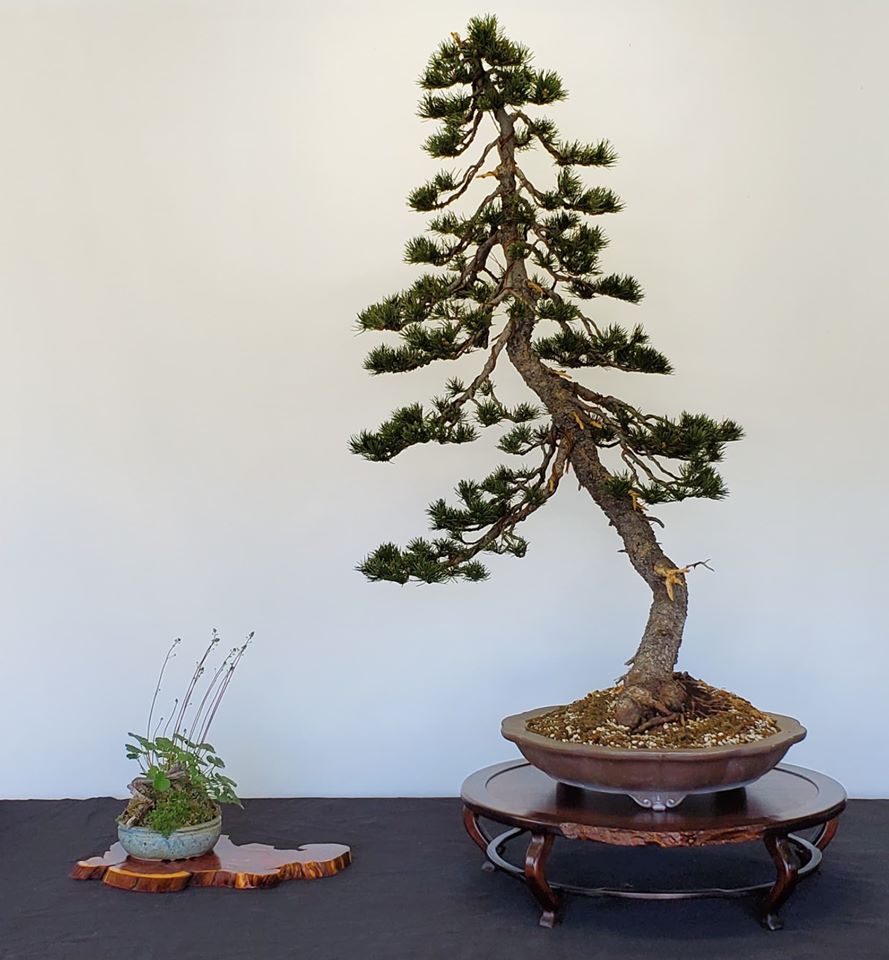
Question #9
Tobias: What type of workshop do you have: stand-alone / garage / basement / etc? What size is your shop? Can you tell us about how your workshop has evolved over time and why? What is the layout and workflow that you have developed (workbenches / assembly benches / lighting / dust extraction / wood storage / tool storage etc)?
David: We bought our current house and property in 2013. There was no place for me to work, so we had a building constructed for me to use as my shop. I was able to design the space to suit my specific requirements for electrical outlets, lighting and access.
My workflow is usually roughing in the parts on the bandsaw, then stickering the parts for a while to sort out any residual stress that may still be present. Next in the process is to joint all of the parts flat and square and to plane them to final dimensions. After that, I generally cut my final joinery on the table saw.
Assembly and finishing work is accomplished on a four foot square torsion box that I use as a workbench. Most of my work is quite small, so this setup suits me very well.
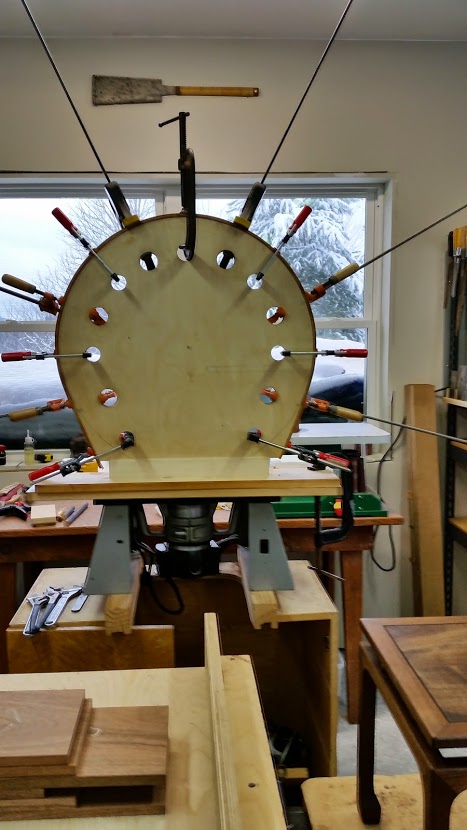
Question #10
Tobias: What is your clamp line-up and why?
David: I have an assortment of bar clamps including 4′ aluminum bar clamps that I use for glueing up panels. For frame and panel glue-ups, I use the Bessey KP block framing system.
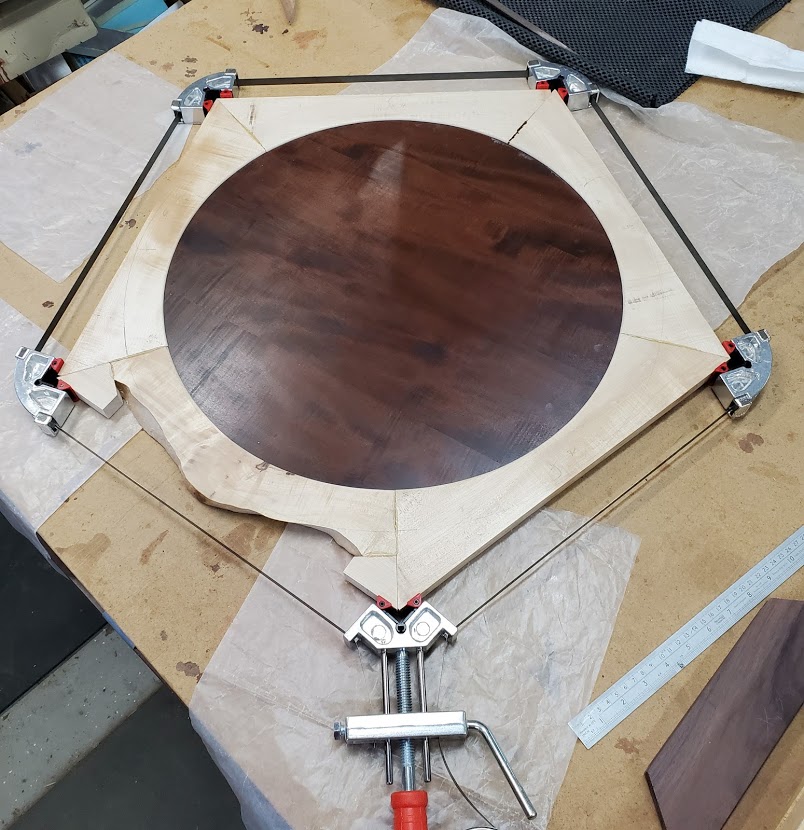
Question #11
Tobias: What adhesives and glues do you use and why?
David: Titebond III is my go-to wood adhesive. For complicated assemblies, I use System Three T-88 epoxy as it has a 45-60 minute open time, allowing me to make absolutely sure that the entire assembly is perfect.
My multi-level bonsai tree stands usually take around 25-30 minutes to assemble, as they can be difficult to get squared up.
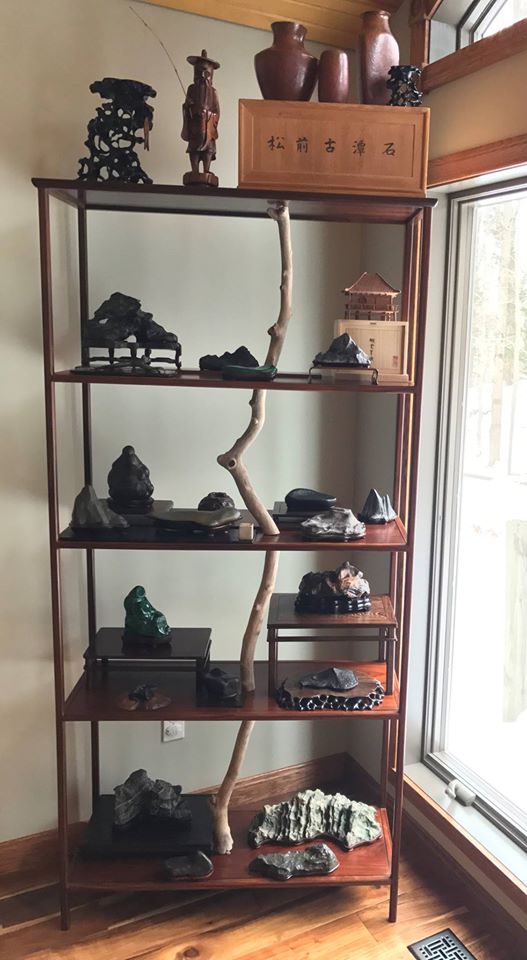
Question #12:
Tobias: Which woods (local and exotic) have you not yet used and why would you be interested in trying them out in you work?
David: I recently purchased some Granadillo. I don’t have a project in mind for it yet, but I am really looking forward to working with it. Granadillo is very dense and features beautiful multi-colored graining and highlights. I will most probably use it for panels, whilst employing a more linear grained wood for the frames.
I also have a large flitch of Zelkova that was cut in New Jersey. I want to use it for the panels of a Tansu when I can find some free time. (I bought it 35 years ago and it has moved with me many times!).
Question #13
Tobias: What and whom are your sources of inspiration in your woodwork?
David: James Krenov and Sam Maloof influenced my early work and later on I became more influence by George Nakashima. I spent a lot of time studying oriental furniture in museums.
In 2010, I was most fortunate to spend three days studying under Kunio Kobayashi when he was in the US. He is one of the instructors at the Katayama School of Keido in Japan. This is a school that teaches traditional Japanese display and it has helped me dramatically in my work.
Question #14
Tobias: How do you design your pieces? Do you use CAD or SketchUp? Do you sketch out by hand, etc?
David: I sketch all of my pieces out by hand. Once I am comfortable with a design, I draw an accurate scale drawing from my sketches. Most often, I am working with an artist who has an object that they wish to display. Some of them have a really good idea are what they are looking for.
Many ask me for my guidance and advice, often sending me a photograph with the dimensions of their tree or object and then we go back and forth refining ideas until we settle on a design, wood species, colour, finish, etc.
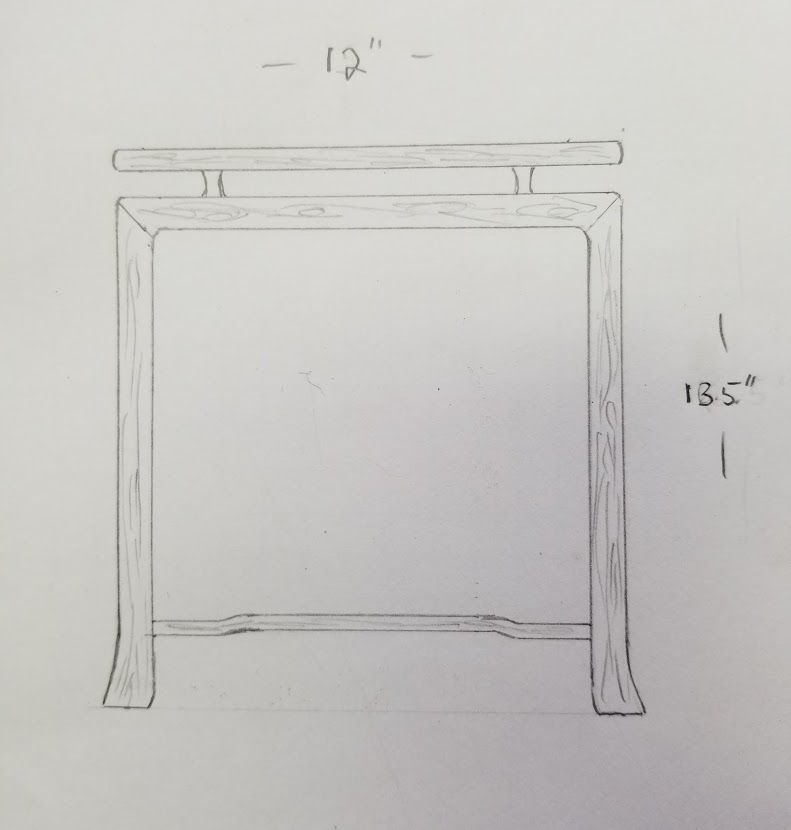
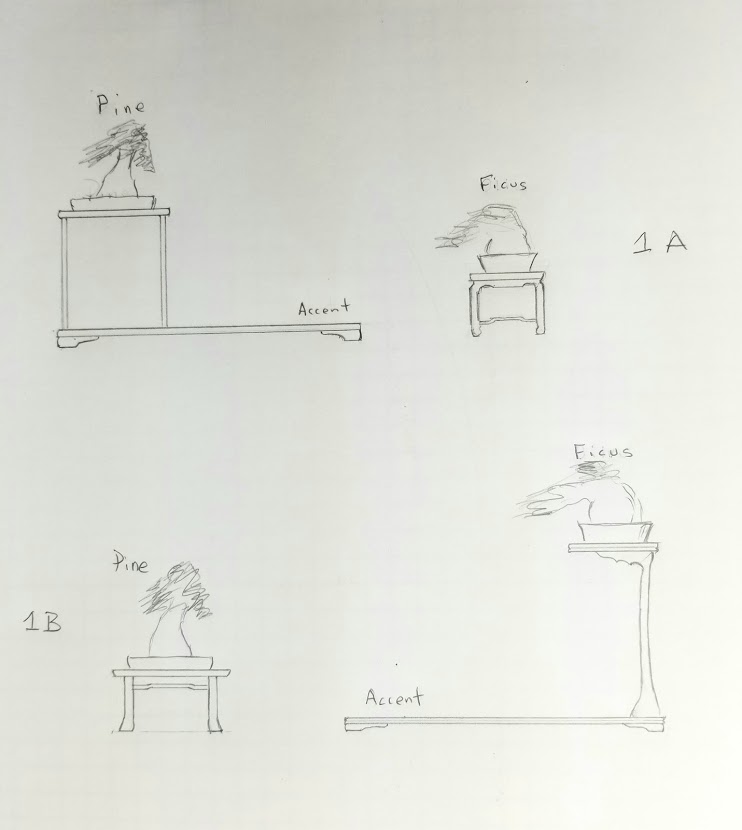
Question #15
Tobias: What are your finishing regimes, which products do you use and which are you favorite processes?
David: I sand most woods to 280 grit. Most often, I am coloring them lightly to enhance the grain, however on occasion, I need to enhance the color quite drastically with water based aniline dye stains.
Some of the more oily exotic species are first treated with a couple of coats of thin shellac to seal of the oils and resins. my topcoat is a blend of Epifanes tung oil based varnish and a small amount of raw tung oil. I thin this blend with a solvent and use it like a penetrating oil, applying four to six coats, depening entirely on the type of wood. After the final coat has cured, I rub it out with Renaissance Wax.
Question #16
Tobias: Which parts of your woodworking do you dislike the most?
Kevin: Definitely doing the finishing, as I dislike the solvents. I do tend to have a love/hate relationship with my finishing blend. I love seeing the color and grain pop out, but I hate the solvents and chemicals in the finish.
I am mildly allergic to these chemicals and get flu-like reactions from them. My shop has good ventilation in the warmer months and I do wear a respirator. It is more of a problem in the cold weather when the shop is closed up.
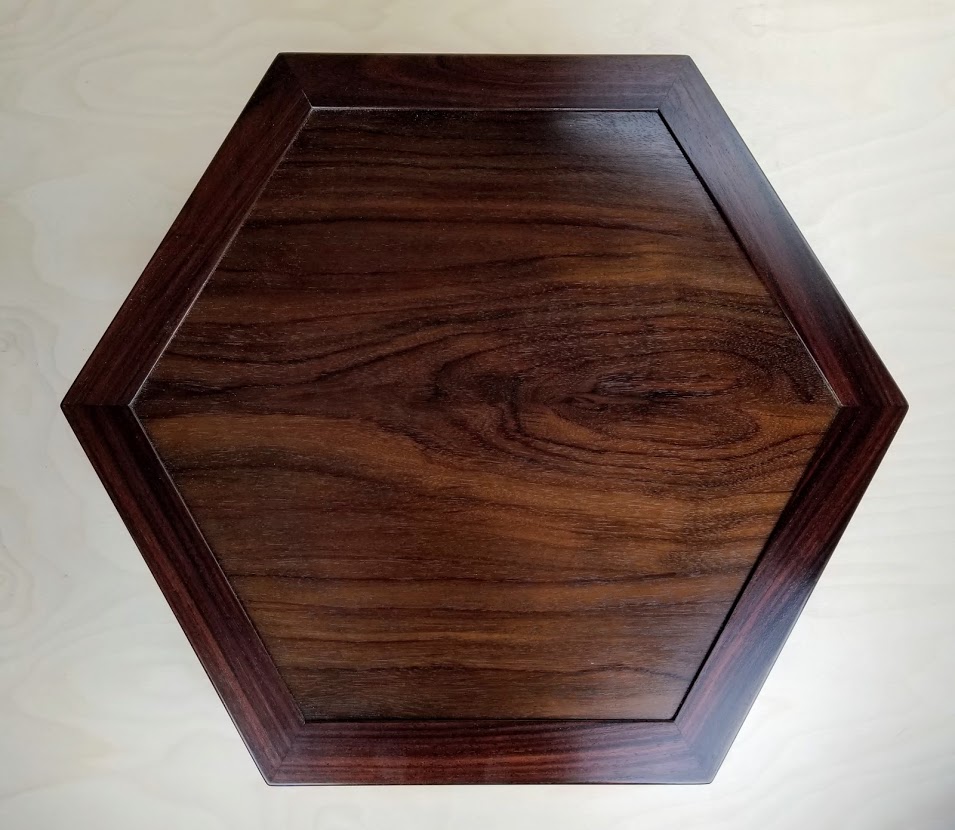
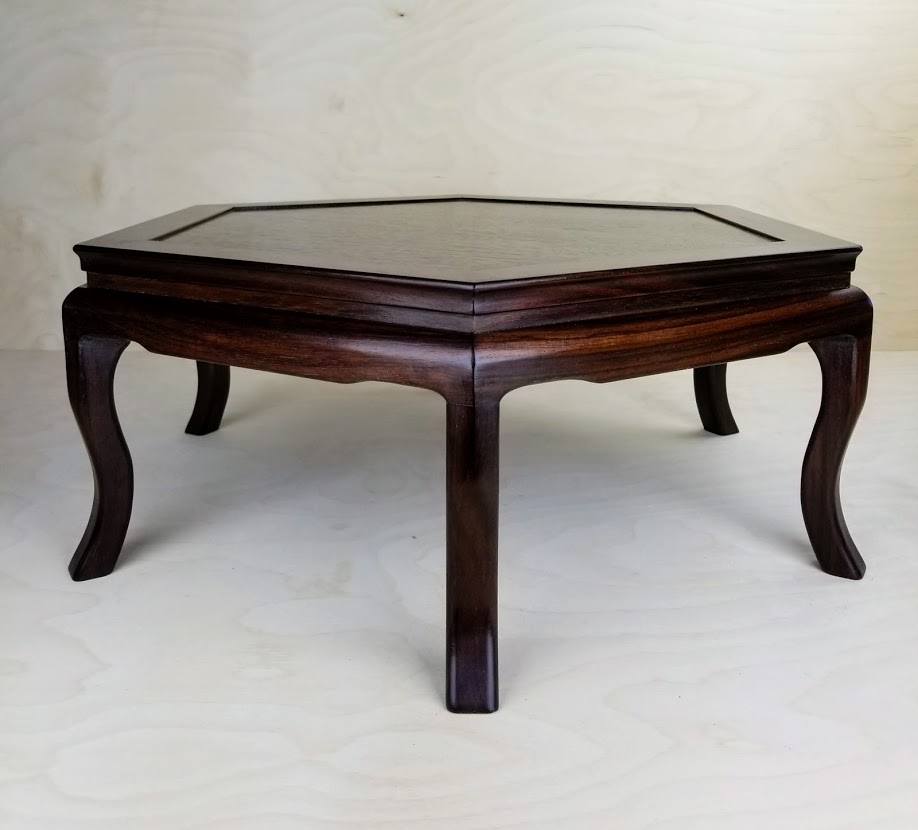
Question #17
Tobias:What music do you enjoy listening to in your workshop?
David: Folk rock! I enjoy Neil Young, Bob Dylan, The Eagles,. Tom Petty & the Heartbreakers and Eric Clapton.
Question #18
Tobias: What is your tool sharpening regime?
David: I use Japanese waterstones to sharpen all of my tools. I also use an electric Makita horizontal whetstone grinder fitted with a 1000 grit wheel for when I need to remove a lot of metal or fix any damaged edges.
I use an array of water slipstones to sharpen my gouges and V tools and I use flat whetstones to sharpen and hone flat chisels and carving knives.
I have 400, 800, 1000, 1200, 2000n and 3000 grit Japanese whetstones. I also use a range of feather files to sharpen my hand saws.
As I rarely use any honing guides or jigs, I could not find mine to take a picture of them!
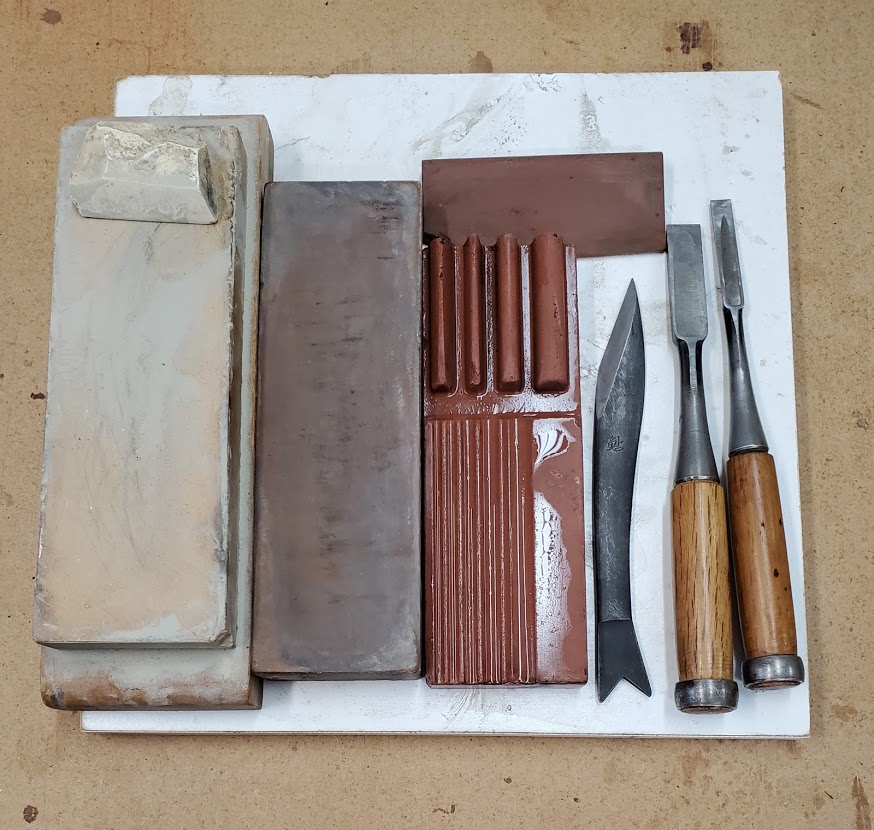
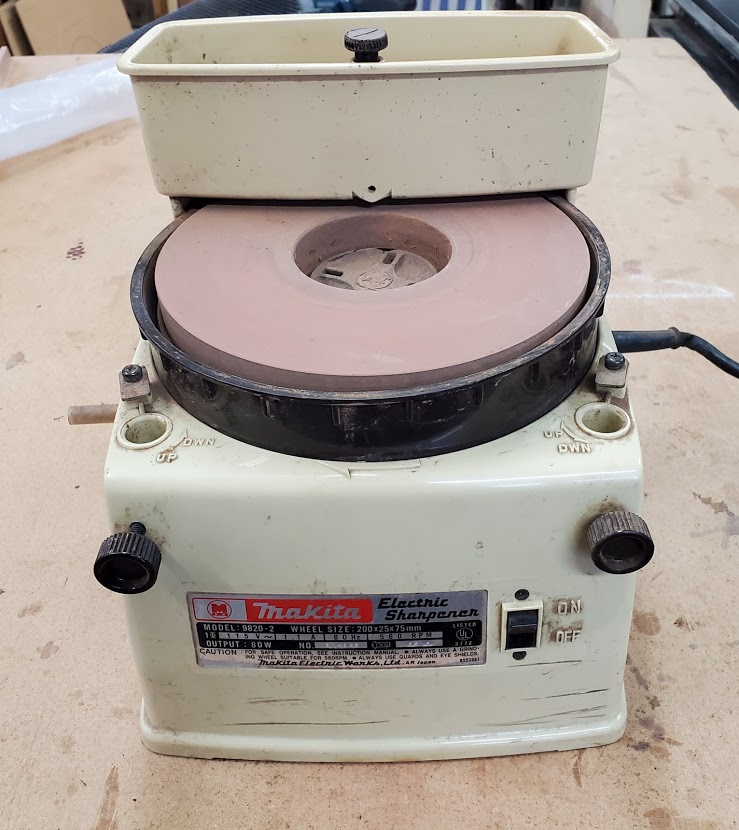
Question #19
Tobias: What custom jigs or tools have you developed for you woodworking?
David: I have quite a large array of custom jigs that I have developed over the years. A few of them are specifically for cutting joinery, but most of them are designed to assist in the assembly of complicated pieces.
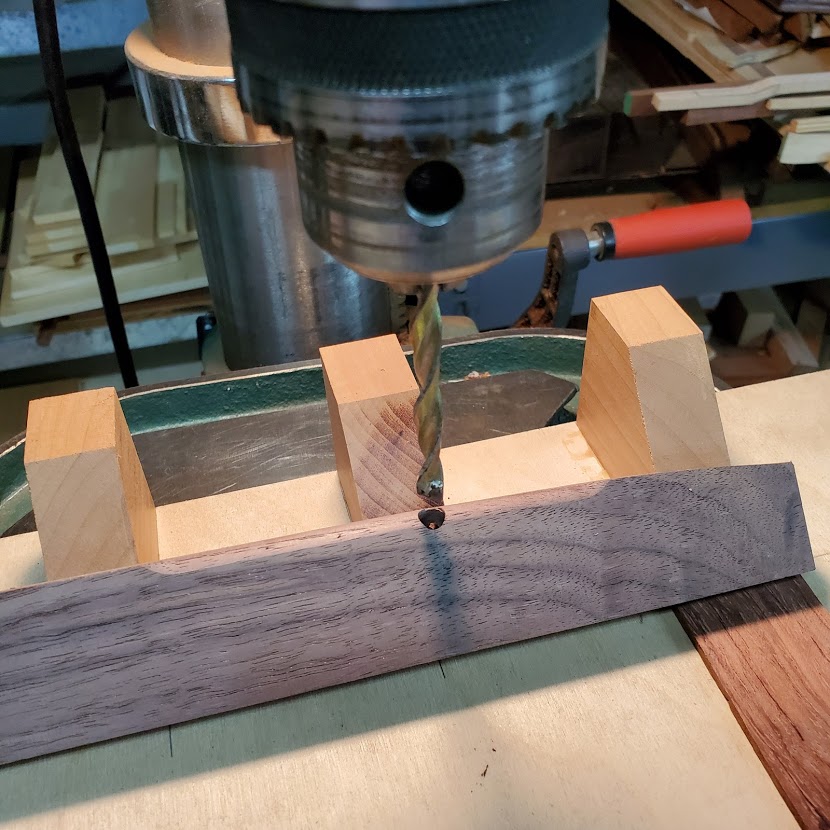
Question #20
Tobias: What is the next piece that you are going to build and why?
David: I am in the beginning stages of building a hexagonal shaped Cherry display stand for a large bonsai that will be exhibited at the National Bonsai Exhibition. The piece is my modern interpretation of a classic Chinese table. I bought the curly Cherry a few months ago for this project. I will be darkening it slightly on this project, but not enough to hide the wonderful grain and highlights.
Tool Wishlist
- Wide Belt Sander (although I would have difficulty fitting it into my workshop)
- Japanese Dovetail Chisels (Mine went missing in a move)
- An assortment of Auriou files and rasps
- A Japanese saw specifically for hardwoods
Lumber Wishlist:Local
- Dogwood
- Figured Big Leaf Maple flitch
- Birdseye Maple
- Air dried Walnut
- Alaskan Yellow Cedar
Lumber Wishlist: Exotic:
Makers with whom I would love to spend quality time
Mira Nakashima, who took over when her father George Nakashima passed away. (www.nakashimawoodworkers.com) and Austin Heitzman of Portland Oregon. (www.austinheitzmanfurniture.com)
Many thanks to David Knittle for sharing his creativity and uniques woodcraft with us at Rare Woods USA. If you are or know of an interesting woodworker in your area that would enjoy being featured in the Rare Woods USA Woodworker Sessions series, please drop us an email at info@rarewoodsusa.com.