Our South African operation runs 23 low temperature dehumidification kilns to dry wood. They work well for most 1 inch wood but get a bit iffy on thicker sizes. They are also incredibly costly to run (on average $266 / cubic meter compared to cost of $70 in USA and €80 / cubic meter in Europe (and this is after labor costs in South Africa that are 10% of the USA).
We use them less and less these days but where we are unable to source wood in kiln-dried form we do need to resort to doing the hard work ourselves heavy. This is generally painfully slow and pretty expensive – approximately eight men for two days to load and four hours to unload and four to six weeks in a kiln that is constantly consuming costly electricity.
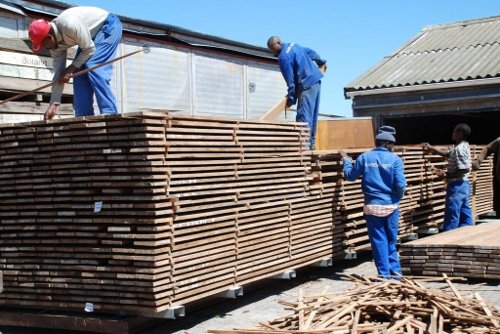
Kiln drying can involve a huge amount of back-breaking labour
We were very fortunate to already have two functional kilns in the Maine facility when we acquired it, but the technology was old (Irvington Moore) and relied on principle of an integrated mill – when the Thurston dowel mill operated everything from the bolt mill to dowel-making created off-cuts and waste which fuelled the boiler which, together with the hydro plant, in turn provided power and heat for the building and processes. Now that we are basically a buy, sort, market and resell facility, the waste is not created and the whole process breaks down.
The kilns have not gone to waste however. Instead we have converted them into much needed storage space and an extended machine shop. This is a win-win situation for everybody, as we will use efficient local custom kiln-driers for specialist work, and we have used plenty of local contractors for the conversion process.