Welcome to the Rare Woods USA Woodworker Sessions Interview Series.
Here, we endeavour to discover more about what makes our woodworkers tick, how you became involved in the craft, how and why you build your pieces and maybe glean a few tips and secrets along the way!
Our interviewer, a woodworker since the age of 8, Tobias Lochner is no stranger to the workshop.
The 13th issue of The Woodworker Sessions USA features Randall Mayse of Maine Fine Furniture in Rockport, Maine.
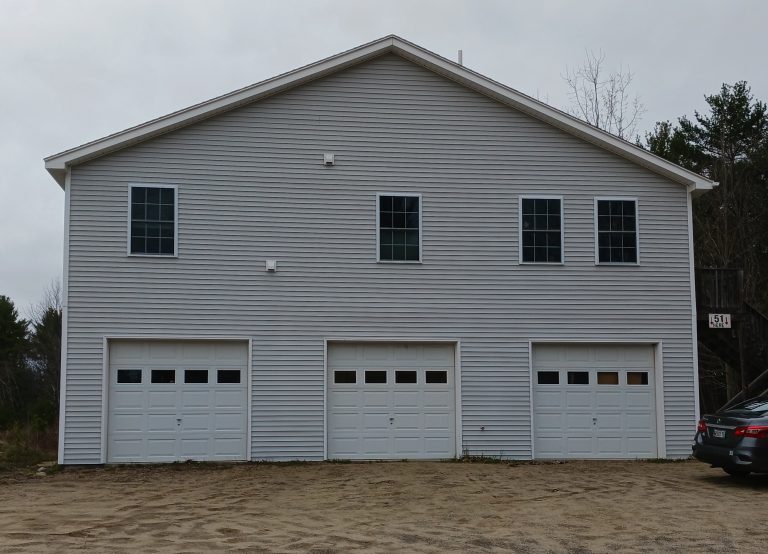
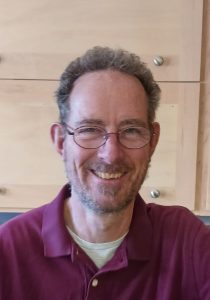
Question #1
Tobias: Hello Randall, thanks so much for joining us. Please tell us about yourself, what is/was your career, about your family and how you became a woodworker.
Randall: Hi Tobias. Thank you for inviting me to the Woodworker Sessions.
Both my dad and my grandfather made furniture and they passed that hat on to me along with their work ethic. My two kids are all grown up now with lives of their own, so life is about me and my partner, Marie. We enjoy gardening, sitting in the swing with an ice coffee and getting rejuvenated by walking our wood lot.
My career was mostly as a machinist and tool maker, which was excellent training for planning projects and it also pacified my creative side, although the connection to wood was still missing.
In 2000, a job fair and a tour at Thos. Moser Cabinetmakers in Auburn, Maine, set me on my path to become a real woodworker! It was here that I learned patience, persistence and what quality really looks like. I am forever grateful for my time spent there and the incredible wealth of knowledge that was passed on to me by my trainers.
Not yet retired, most days you will find me working 8am to 6pm, cutting chips and making sawdust. Some may say that I am a workaholic, hardly taking a day off… To me, I am in heaven with the smell of wood and the hum of my machines.
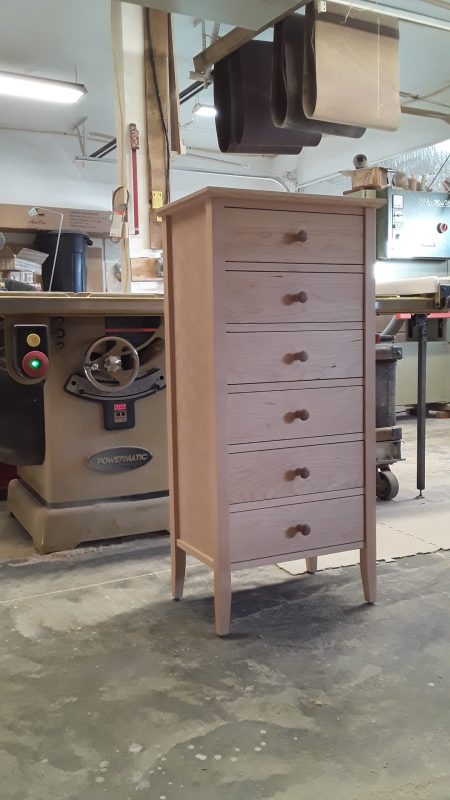
Question #2
Tobias: How did you get started doing woodwork and how long have you practiced the craft?
Randall: My interest in working with wood started as a young boy at 7 or so, whittling with a jack knife making knives, spoons and other small items.
While in Jr. High School, I bought an AMT lathe and fell in love with turning, so I guess that you can say that I have been a lifelong woodworker.
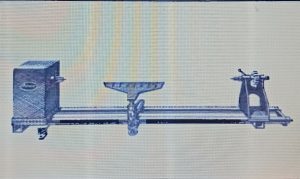
Question #3
Tobias: Which was the first “real” piece of furniture that you ever made and which is your favorite?
Randall: The first item that I made was a Black Walnut spiral lamp when I was in Jr. High School.
I do have many favorite pieces, but an eight drawer Shaker inspired Black Walnut dresser with Maple drawer fronts and side panels, including hand made drawer pulls would definitely be my most favorite creation!
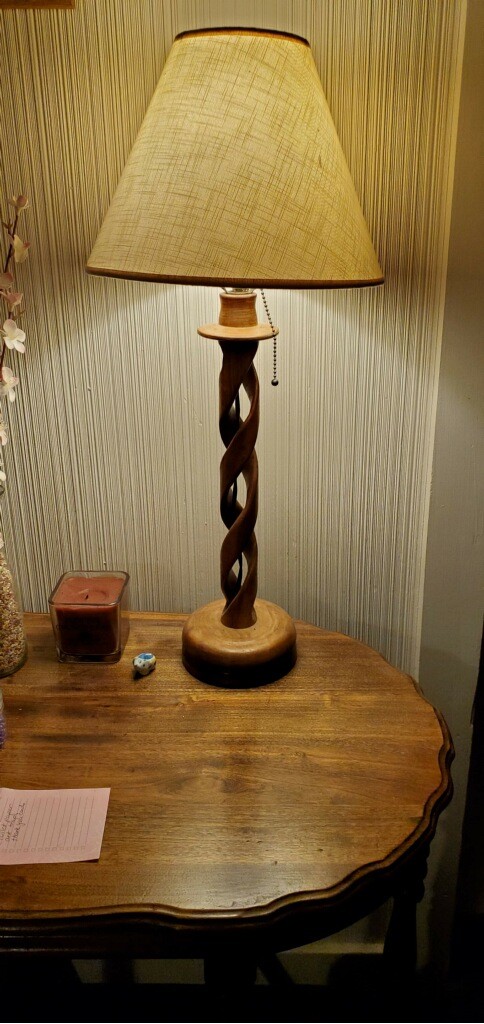
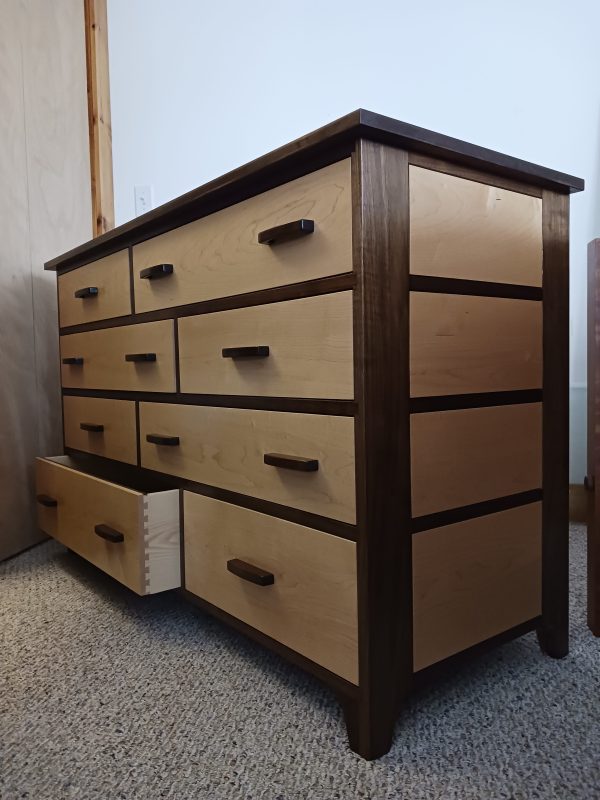
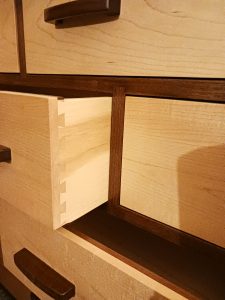
Question #4
Tobias: Which style of furniture do you most enjoy building?
Randall: I would say that the style of furniture I most enjoy building is of my own design, which is heavily Shaker inspired because of the beauty and simplicity. I really do get a big charge out of anything that I have not built before and working through to its completion.
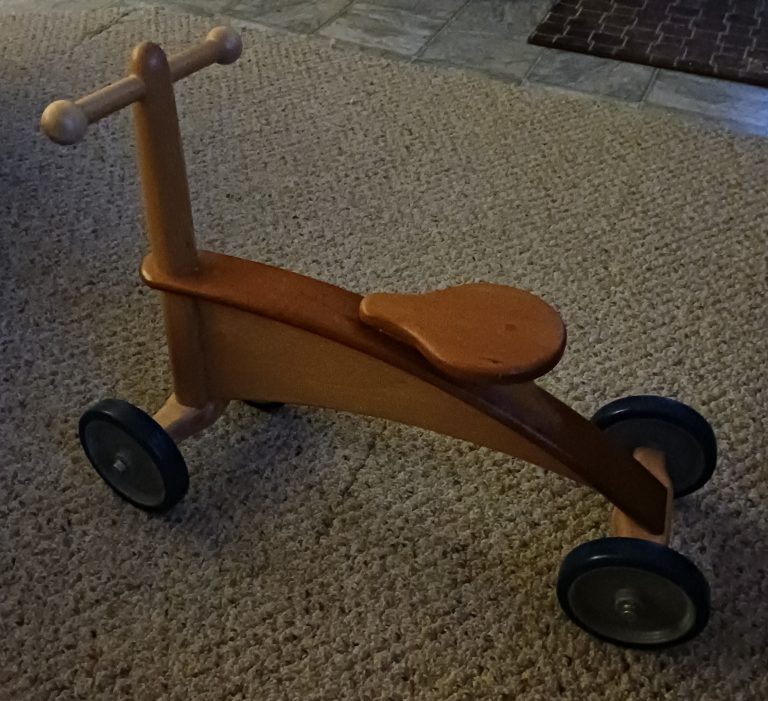
Question #5
Tobias: Which are your favorite local lumber species and which are your favorite exotics to work with?
Randall: Although I work intensively with Maple, White Oak and Black Walnut, my favorite local lumber species is Cherry! I love matching the color and grain as close as possible to make the piece look “just so”. Exotic woods have not yet become a priority, however I do have some Wenge for which I am currently considering a design. Purpleheart is another exotic that I would love to work with, given the opportunity.
Question #6
Tobias: Please list your most used hand tools and tell us why they are your “go-to” tools?
Randall: My most used hand tools are my Lie-Nielsen set of bench chisels, Lie-Nielsen block plane, Veritas saddle square and Starrett combination square. I “go-to” these tools because the quality, accuracy and workmanship is unparalleled and the chisels and plane hold a really sharp edge, making them a joy to use.
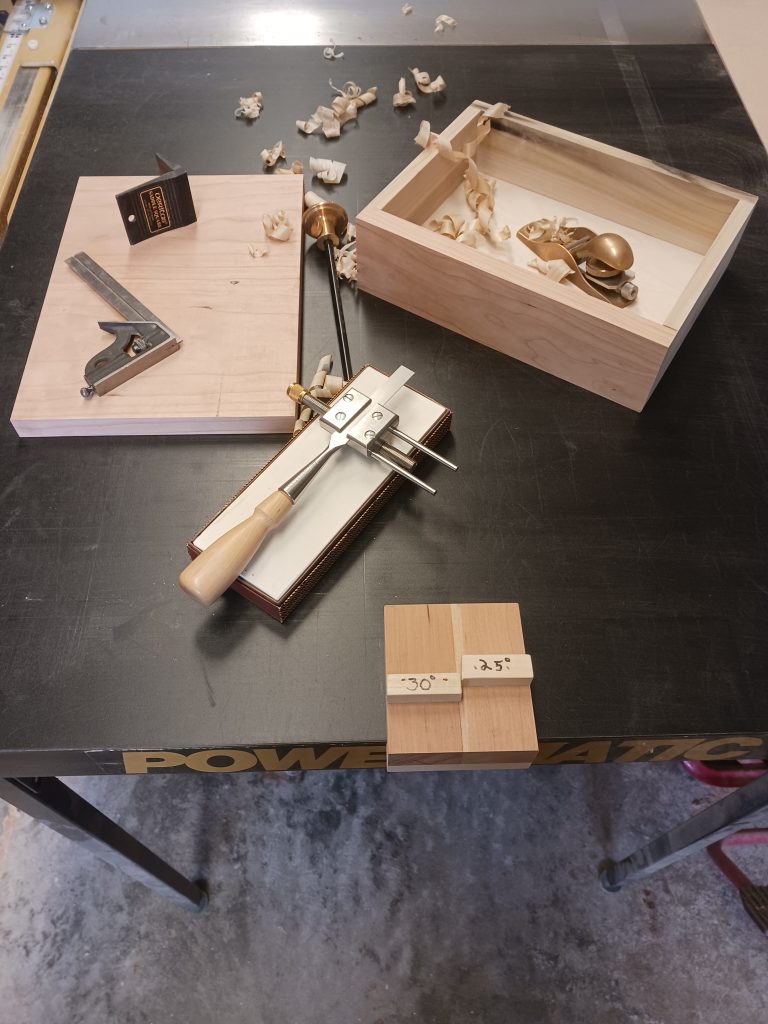
Question #7
Tobias: Can you list your favorite power tools and machine and tell us why they are your favorites?
Randall: My favorite power tools are my Faye & Eagan 6 x 24 planer that was made in 1915 that I purchased prior to building my shop as an incentive to myself, and my SCMI 25″ wide belt sander which together with the planer enables me to mill stock up to 24″ wide!
My newly acquired Powermatic table saw is definitely on the list because of its power and accuracy! I am also proud of my profile sander that I built from plans in an old Shopnotes magazine using a Bridgeport mill I bought to compliment my woodwork. I use it to make jigs and do close tolerance work.
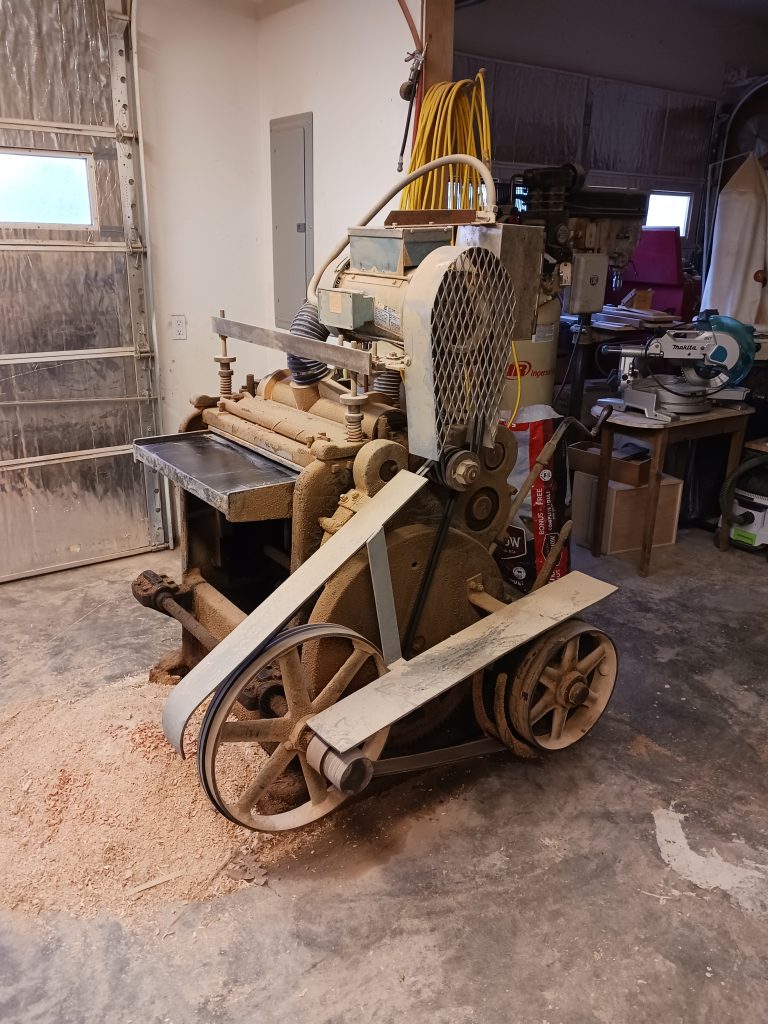
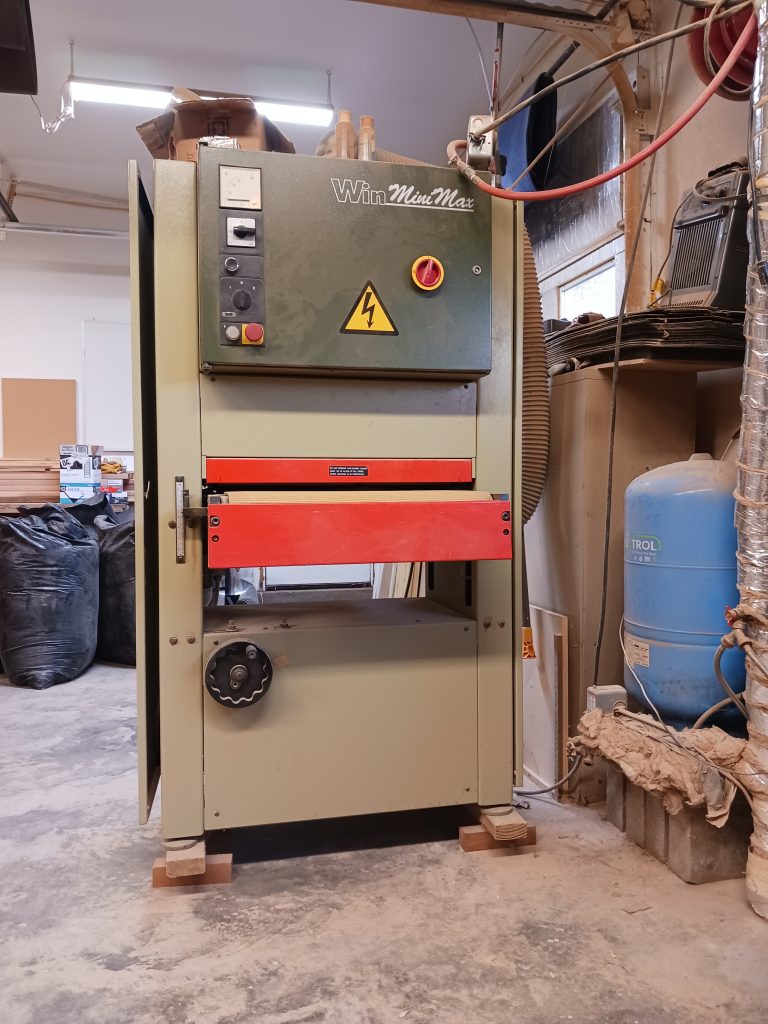
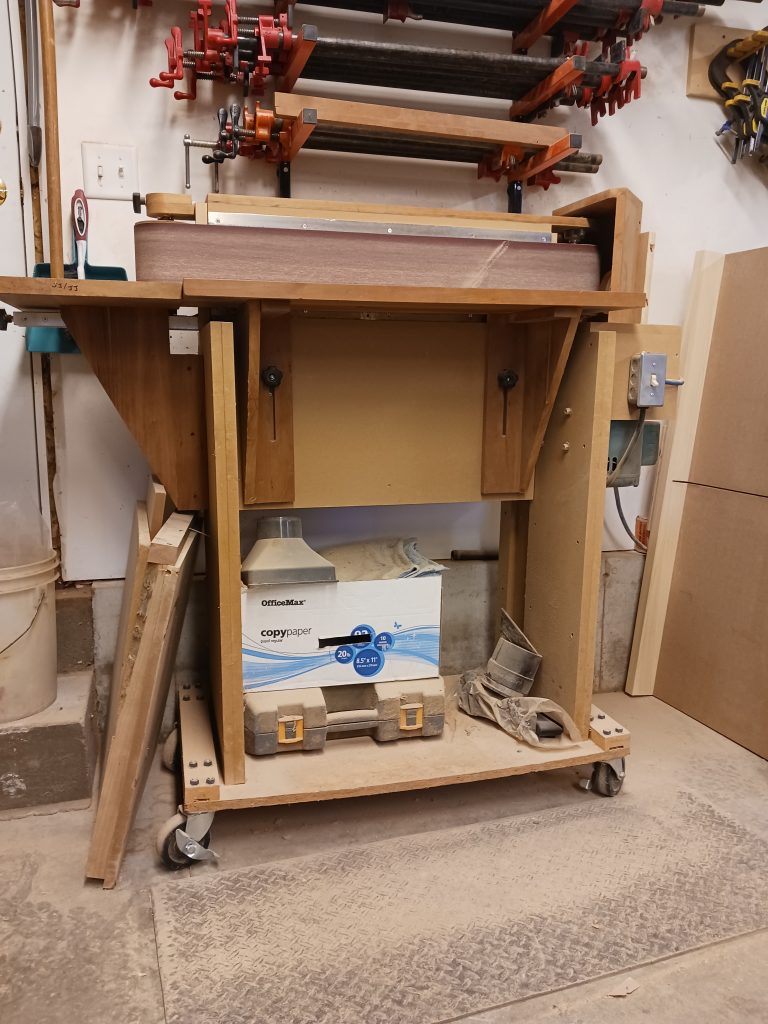
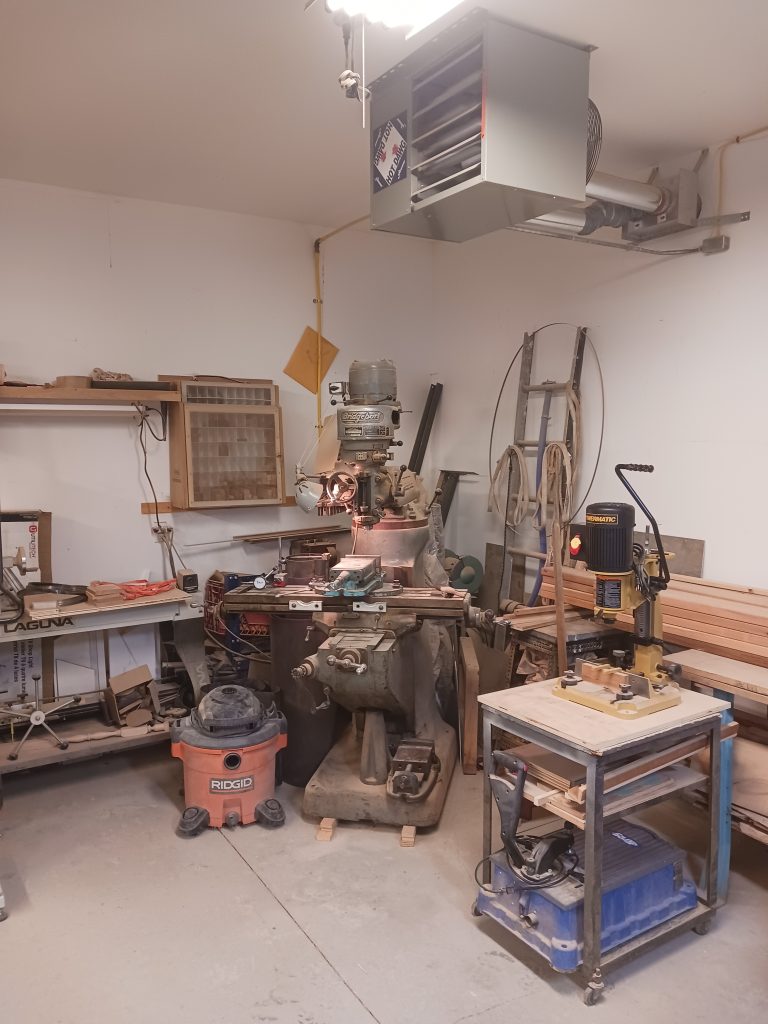
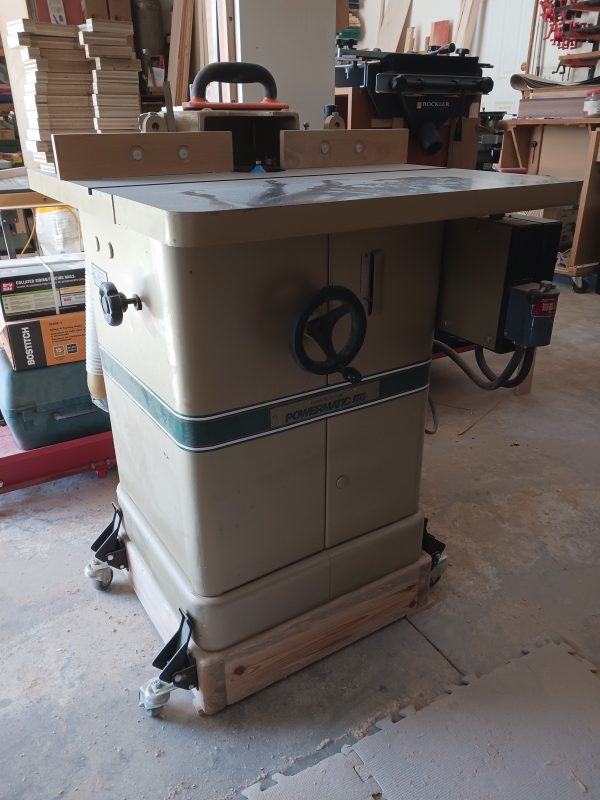
Question #8
Tobias: What is it about working with wood that you find most enjoyable?
Randall: Wood has a life, unlike metal. It’s difficult to explain, it’s more about the feeling of the wood in your hands and the wonderful smells when you are cutting it. There is an energy, a warmth, the possibilities that it holds and the infinite range of things you can do with wood. Importantly, wood has an intimate allure of creating something beautiful and long lasting. I love the creative process of sketching out an idea and then bringing it to life.

Question #9
Tobias: What type of workshop do you have and how and why has it evolved over time?
Randall: In 2007, after purchasing my big planer, I started felling trees and collecting lumber to build my shop. At that time, I had mostly carpentry tools, a contractors table saw, a radial arm saw, a drill press and a bunch of generic hand tools. I like to keep my debt and stress levels low, so while working as a machinist, the furniture contracts that I did, effectively paid for the equipment I needed.
A little at a time, my shop was tooled up with a better table saw, Jet drum sander, 8″ Delta jointer and a shop made router table and edge sander.
The opportunity to build wholesale for Shaker Furniture of Maine in 2015, allowed me to work in my shop full time as a production manufacturer. More upgrades were quickly in demand!
A Powermatic shaper replaced the router table, a new Powermatic table saw, Laguna 14″ bandsaw for resawing, lathe and Versa duplicator, an Inca 10″ jointer I absolutely love and an 18″ upcut saw that will effortlessly cut a 15″ wide piece of 8/4 Cherry in seconds were all added to the shop. The wide belt sander replaced the drum sander. I do however, feel myself being drawn more and more to quiet work in the future, with a transition to hand tools and less production equipment.
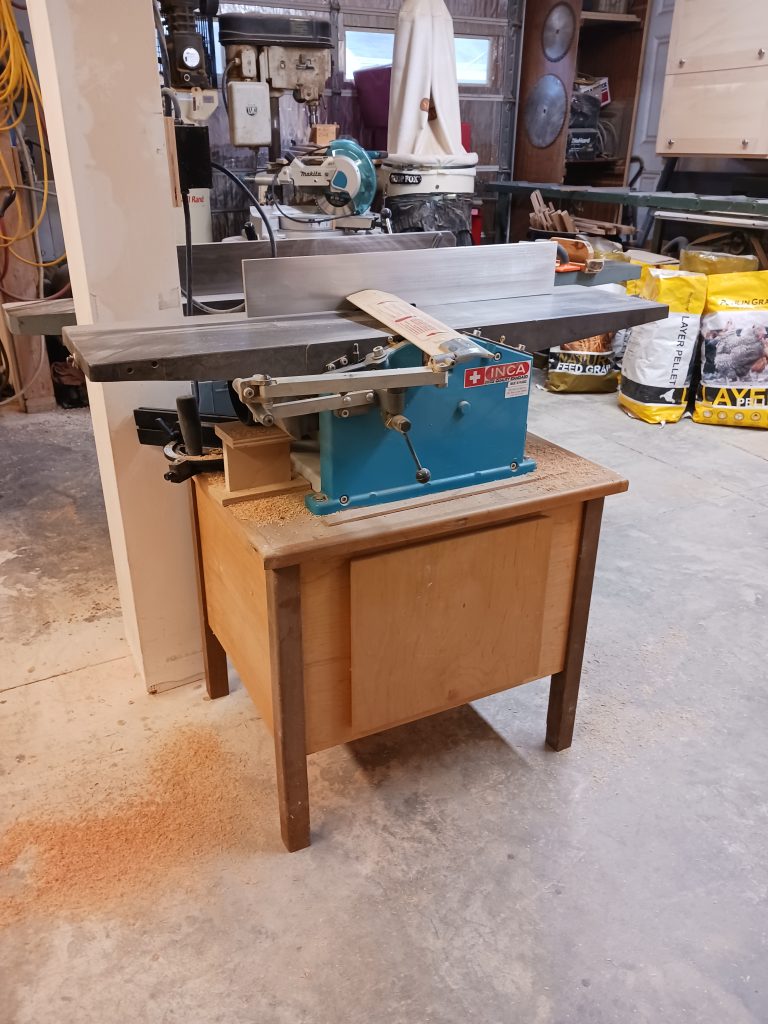
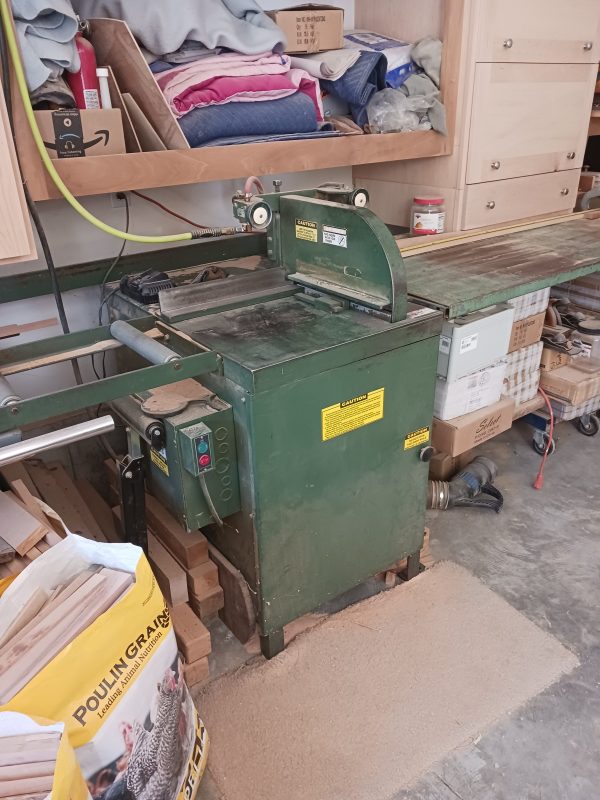
Question #10
Tobias: What is your clamp line-up and why?
Randall: I have a wide variety of clamps in my shop, but the clamps that I use the most now are Bessey’s pipe clamps. They come with pads, have feet for support and the lengths can be changed, using longer pipes when required.
I have assorted sizes of Jorgensen wooden jaw clamps and quick grips of various lengths. Merle band clamps and a few squeeze clamps round out the clamp rack.
Sometimes, for a quick fix for a small repair, a piece of tape does the trick! My clamp selection has grown and changed as my shop requirements have evolved. Sometimes, single-use plywood clamps are useful for a specific situation where a normal clamp cannot be employed.
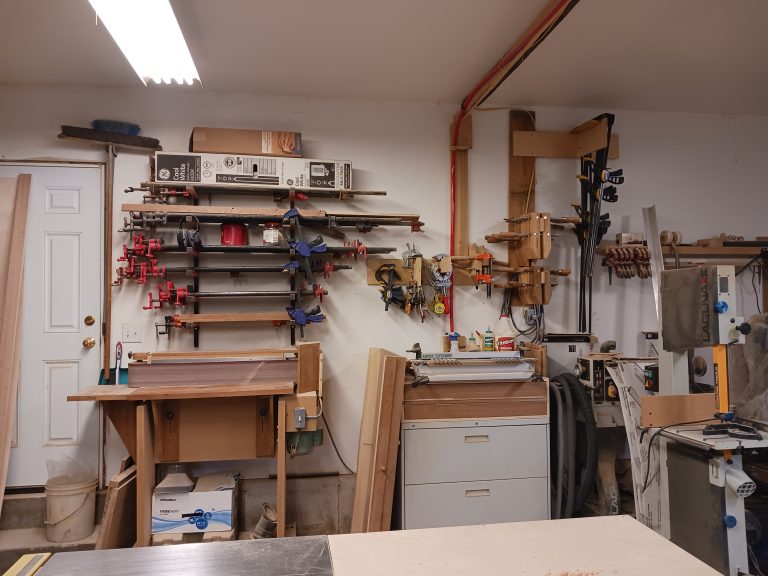
Question #11
Tobias: Which adhesives and glues do you use and why?
Randall: Fine Woodworking magazine #294 has a great article titled “An Instructor’s Guide to Glue” by Bob van Dyke. I keep the copy in my shop as a reference for when I need to expand my glue choice. Generally, with the furniture that I am making, 90% of it is glued together with Titebond Original. The other 10% would be Titebond III or epoxy where required. I have plans to do do bent lamination and veneer work in the future and for that, the glue guide says to use urea formaldehyde which I am very much looking forward to.
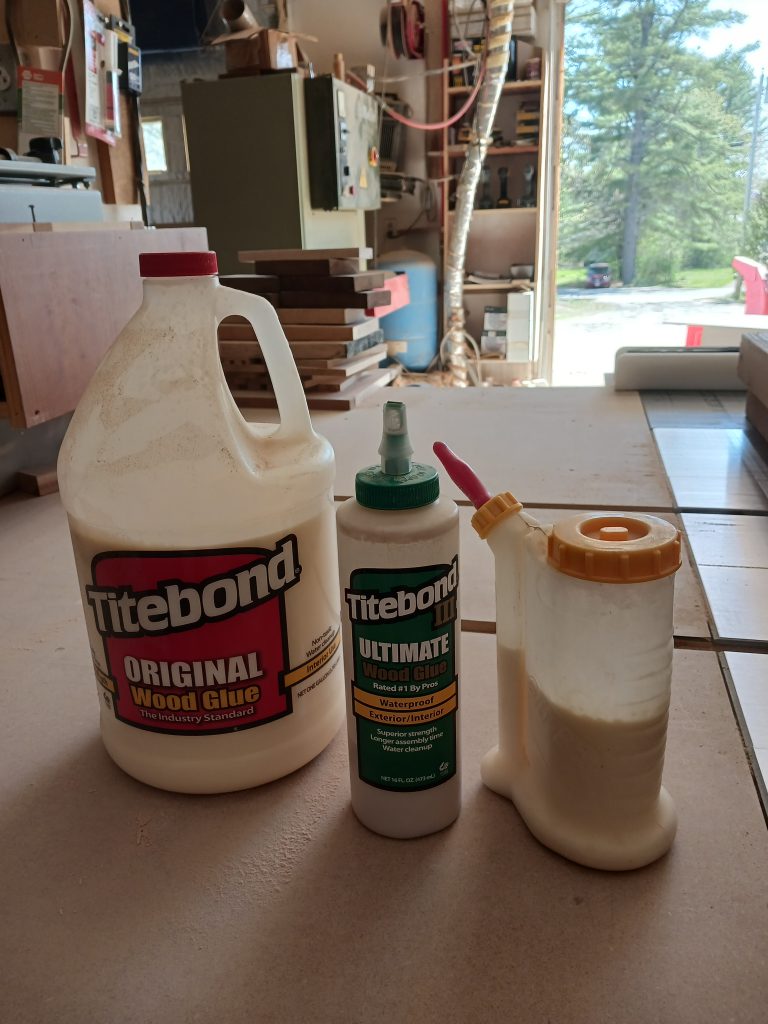
Question #12
Tobias: Which woods (local & exotic) have you not yet used and why would you be interested in building with them?
Randall: There is a huge range of choice when deciding which wood to use to create a beautiful piece of furniture. I enjoy species with dynamic appearance, crazy grain and variagated color. I have a piece of Spalted Maple and I am not sure what I’ll do with it yet. It is very light and punky, so whatever I use it for will definitely be a challenge!
My thinking on exotic woods is that a little goes a long way to add highlights and excitement. I really like the look of Snakewood and I know that it will be fun to learn how to work with it.
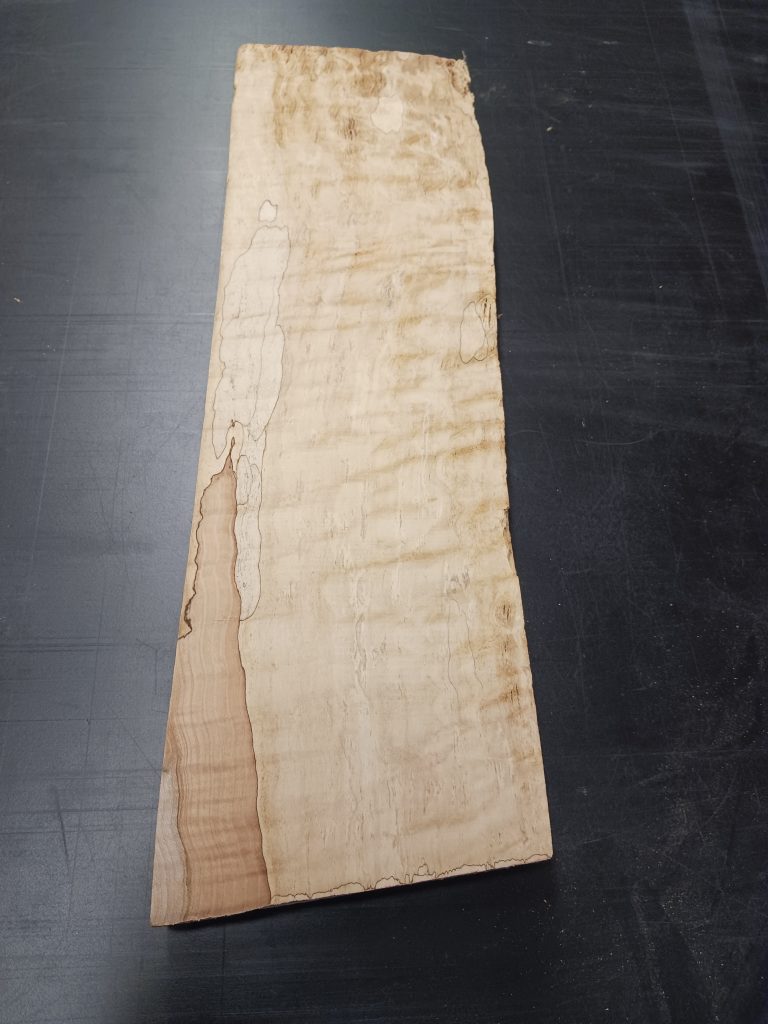
Question #13
Tobias: What and whom are the sources of inspiration for your craft?
Randall: The first person that inspired me was my grandfather. He was a builder, loved working with his hands and made many beautiful, useful and interesting things. Nowadays, it doesn’t matter whose work I am looking at, famous or novice, I first feel the the appreciation for its creative appeal. My “reverse engineering” then kicks in to understand how it was made and what techniques were utilized. Even while watching TV, I’m always looking for the furniture in the program to pick up on something unique.
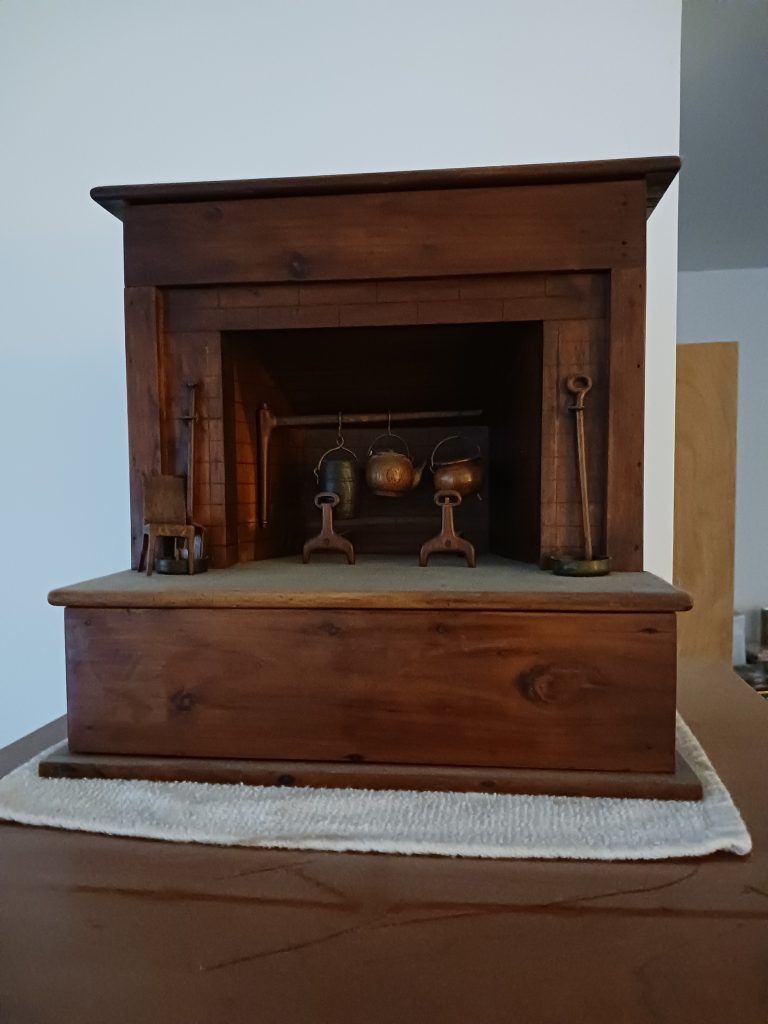
Question #14
Tobias: How do you design your pieces? Do you use CAD, SketchUp or traditional methods?
Randall: A long time ago (in another life) I took a drafting class, drawing with pencil and paper. What I retained from that is being able to visualize in three views. I utilize this in rather crude sketches to enable me to solidify various aspects of a design and to gauge the overall appearance. Then I make copious notes to extrapolate the rest of the required information.
On many occasions, there is an incubation process, where I may change certain things, sometimes even during the build, if I feel that I can improve the functions or aesthetics of the piece.
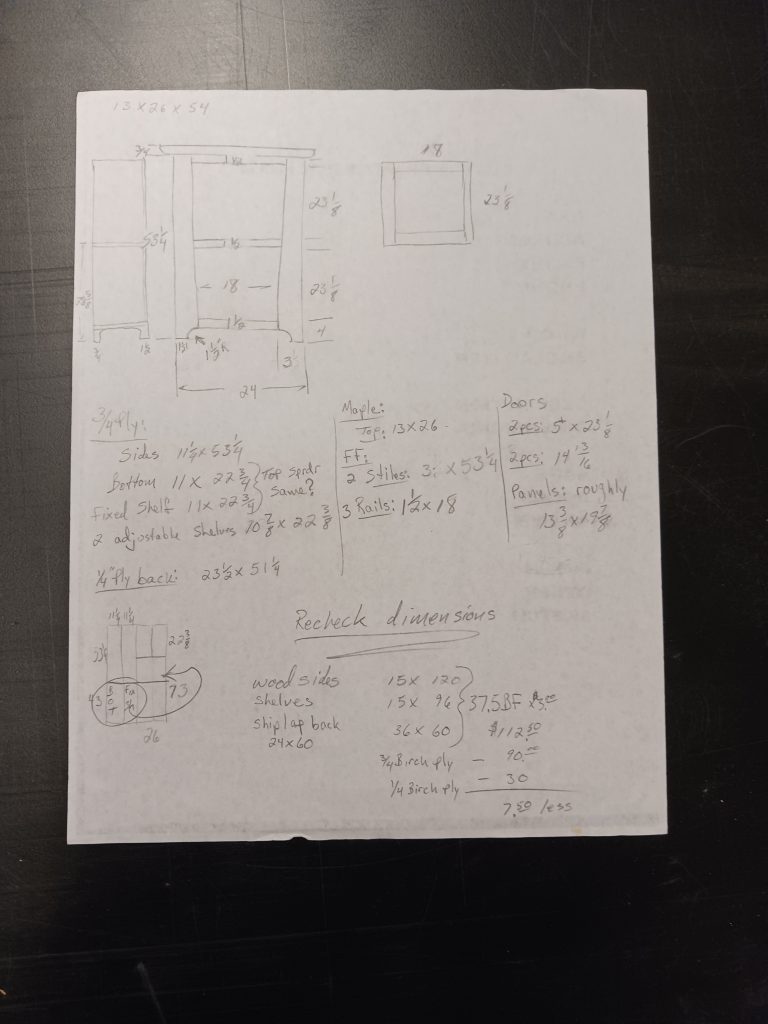
Question #15
Tobias: What are your finishing regimes, which products do you use and which are your favorite finishes?
Randall: Most of what goes out the door of my shop is unfinished, to then be sprayed with lacquer in a professional spray booth as per the customer’s request. If the piece is required to have a rubbed finish, I do this in-house. Sometimes, the finish is just a coat of linseed oil and wax, or a Danish oil satin finish.
I made a bedroom set and finished it by wet-sanding with Liberon Finishing Oil with 220, 320 and 400 grit to fill the grain and leave a lovely smooth shine. I also like experimenting with milk paint, thinning it down for a stain or grain filler to add highlights of different colors and make the grain pop.
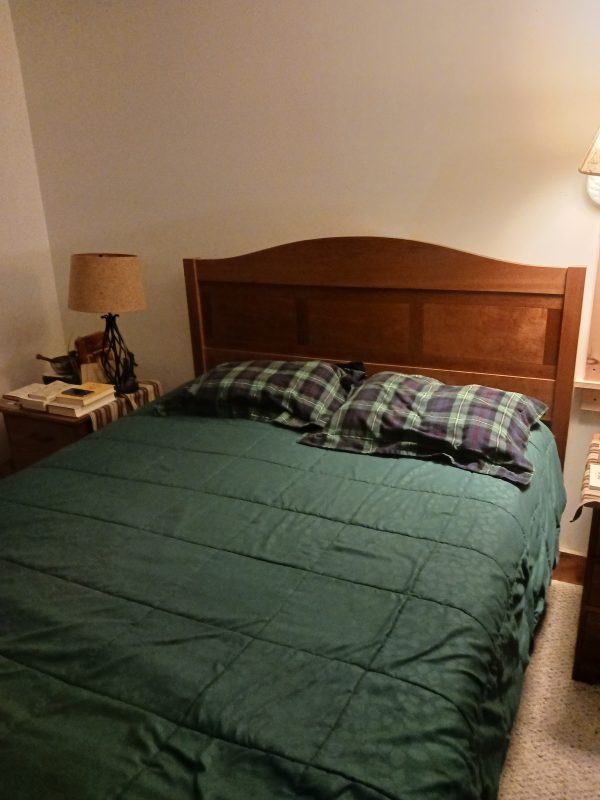
Question #16
Tobias: Which parts of working with wood do you dislike the most?
Randall: The worst part of woodworking has to be the dust. In the beginning, I would shop-vac every machine, but it seemed I was doing more vacuuming than woodwork. I run a production shop and therefore time is money, so there is a level of dust that seems to never go away, no matter how much I clean.
Dealing with cut-offs is an issue as well. I have a hard time letting go of wood that I know could be used for some small project, even if I don’t have time to use it. Sometimes, they pile up on surfaces and get in the way, until I have time to make corner blocks or just give them away.
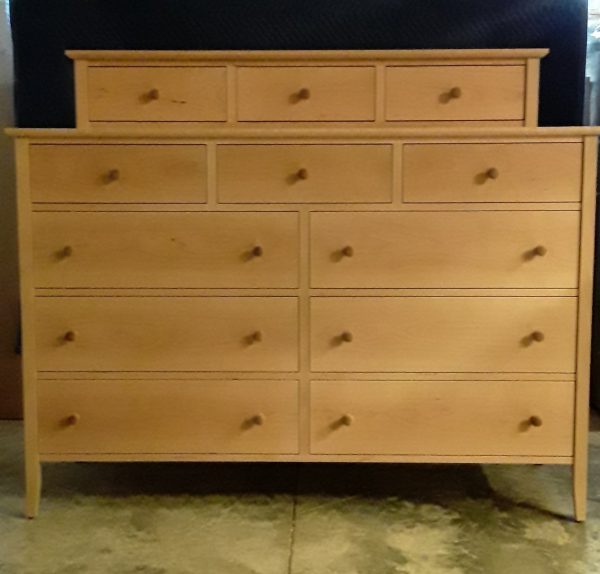
Question #17
Tobias: What is your favorite music to listen to while working in the shop?
Randall: If I’m not running a machine, I listen to a radio station that plays just about everything except rap and headbanging music, but when I really need to think or concentrate, silence is the best music.
Question #18
Tobias: What is your tool sharpening regime?
Randall: Tool sharpening and honing is a fundamental skill that every woodworker must learn properly!
I send out saw blades, planer blades and shaper cutter for sharpening. For in-house sharpening, I use 220 grit PSA paper on my jointer bed, followed by 1,000 and 10,000 grit waterstones with my Lie-Nielsen honing guide.
Question #19
Tobias: What custom jigs or tools have you developed for your woodworking?
Randall: Recently, I took on a job to make trim for pergola posts and needed to glue up the corner 45’s. After a couple of unsuccessful attempts, I came up with a quick and easy wedge system that worked out really well.
When I had to cut a large number of mortise and tenons, I found a jig demo on You Tube and modified the design for my own requirements. Another jig that I made to rout dados and dovetails in casework for shelves and drawer dividers, had to be modified to make custom bead board door panels to match an existing old set.
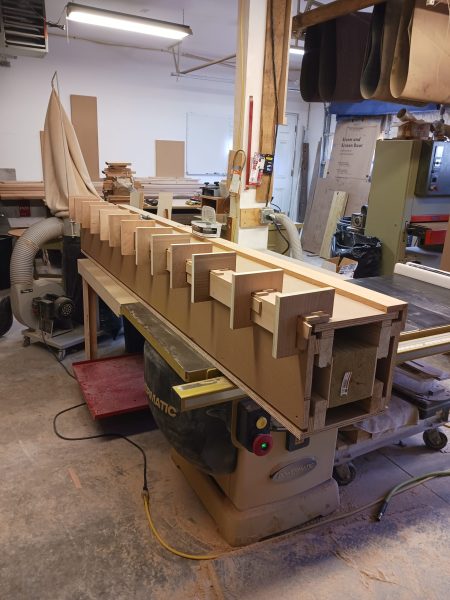
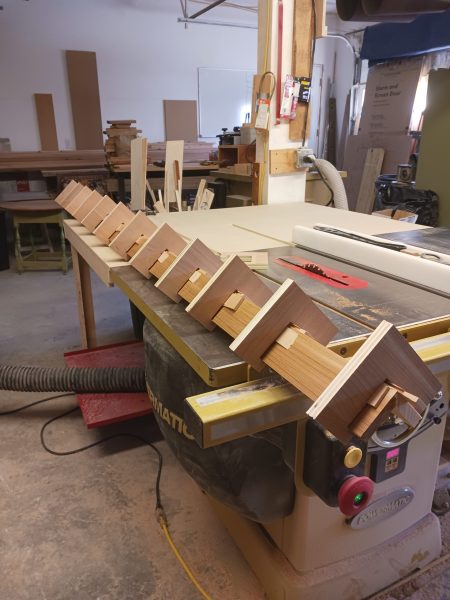
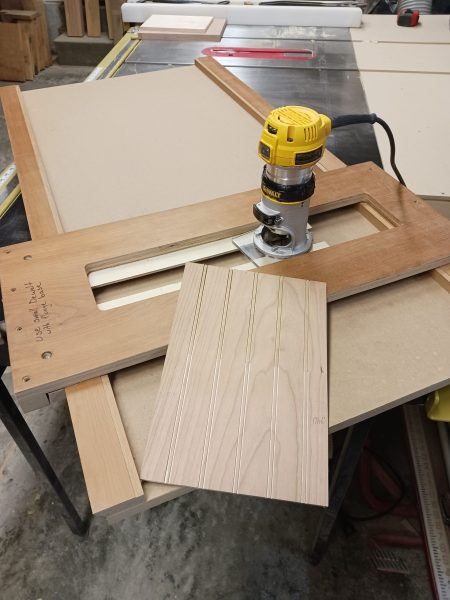
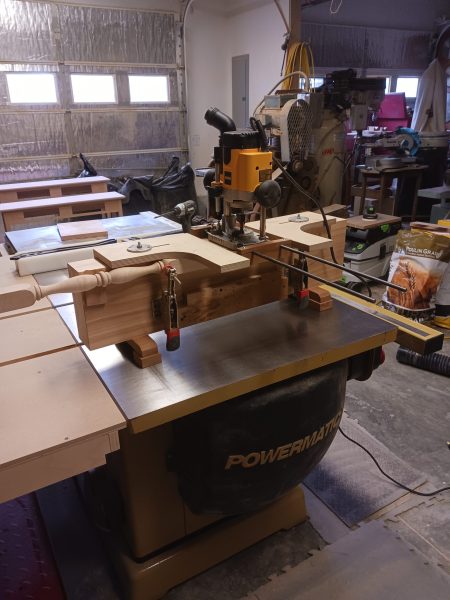
Question #20
Tobias: What is the next piece you are going to build and why?
Randall: My next piece is a project that I have wanted to do for a long time. It is a blanket box with a drawer and a hidden till, as payment to my maintenance guru who bails me out whenever I need help fixing or setting up equipment. The design is Shaker style, made from Cherry with graduated dovetails – small to large, top to bottom. I have chosen to make the dovetails different sizes as a challenge and for a unique appearance.
I am close to retirement age and have been thinking of transitioning toward more hand tool work and away from production work. The first hand tools project will be a real workbench! Adding to my hand plane collection and gearing up to do some labor intensive, but slow work such as sculpting and inlays is also on my list as well.
As far as lumber goes, I think Purpleheart and Birdseye Maple will make a great combination in a sideboard that I drew up plans for. I also have a big Oak log, sawed and stickered, just waiting for special project down the line, maybe a Mission style set of tables and a living room set!
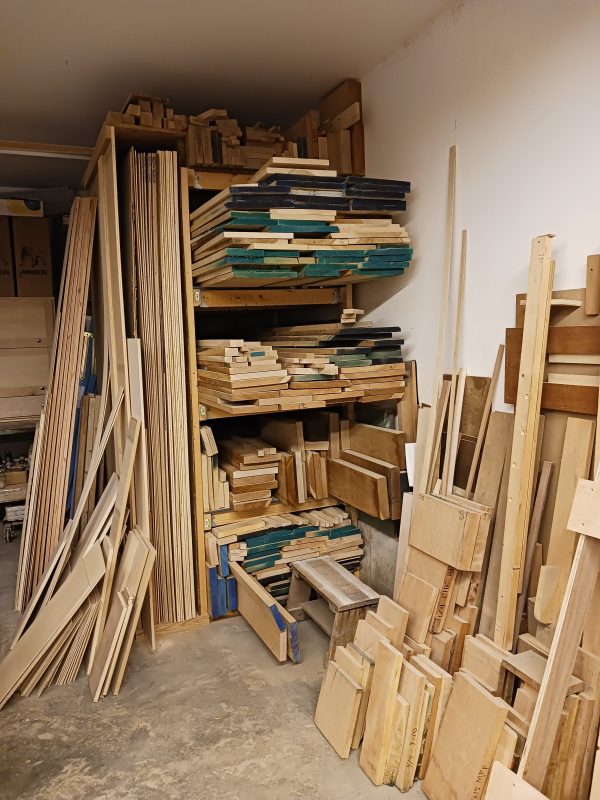
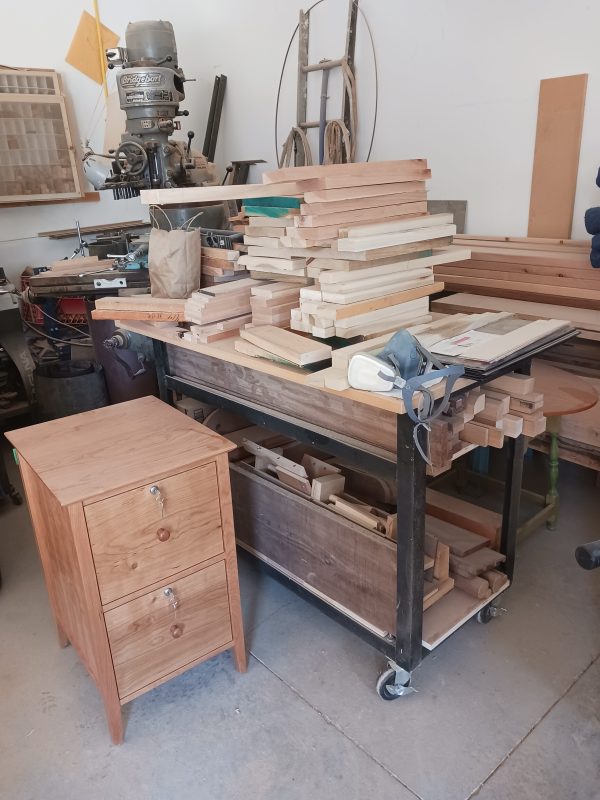
Tool Wishlist
In addition to expanding the hand plane collection, on my Tool Wishlist is a good CNC router. My machinist background informs my understanding of just how useful it could be, expanding my creativity in design.
Lumber Wishlist
I don’t have a “Lumber Wishlist”! Instead, I have a “Time to use the lumber that I have been hoarding” list! It consists of the aforementioned Oak log, a rack full of Hard Maple and a bunch of odd pieces of Ash and Black Walnut. To these, I would like to add appropriate exotic woods for accent work.
Makers with whom I would love to spend quality time
If given the opportunity, I would love to spend real quality time with Christian Becksvoort, a Maine local. I have read his articles in Fine Woodworking magazine and watched many of his videos. He has an immense range of woodworking knowledge to share.
Also, Tom McLaughlin, another contributor to Fine Woodworking, has a similar personality and wealth of knowledge as well.
Links
Our sincere thanks go to Randall Mayse for joining us on The Woodworker Sessions USA. We really appreciate being allowed into the Maine Fine Furniture workshop.
Please feel free to comment and you are also most welcome to suggest other woodworkers that you would like to be featured on The Woodworker Sessions USA!
Hi Randall. Thanks so much for sharing your passions and your woodshop with all of us. Please don’t forget to send us a pictutre or two of the new blanket chest when it is complete!
I couldn’t read the article. The text is very faint.